751.32 Concrete Pile Cap Intermediate Bents
751.32.1 General
751.32.1.1 Material Properties
Concrete | |||
---|---|---|---|
Typically, shall consist of: | |||
Class B Concrete (Substructure) | = 3.0 ksi | ||
= 10 |
In addition, Class B-1 Concrete (Substructure) may also be used in special cases (See Project Manager).
Modulus of elasticity,
Where:
- f'c in ksi
- wc = unit weight of nonreinforced concrete = 0.145 kcf
- K1 = correction factor for source of aggregate
- = 1.0 unless determined by physical testing
Modulus of rupture,
- LRFD 5.4.2.6
Where:
- f'c is in ksi
Reinforcing Steel
Minimum yield strength, | = 60.0 ksi | |
Steel modulus of elasticity, | = 29000 ksi |
751.32.2 Design
751.32.2.1 Limit States and Factors
In general, each component shall satisfy the following equation:
Where:
= Total factored force effect | |
= Force effect | |
= Load modifier | |
= Load factor | |
= Resistance factor | |
= Nominal resistance | |
= Factored resistance |
Limit States
The following limit states shall be considered for bent design:
- STRENGTH – I
- STRENGTH – III
- STRENGTH – IV
- STRENGTH – V
- SERVICE – I
- FATIGUE
See LRFD Table 3.4.1-1 and LRFD 3.4.2 for Loads and Load Factors applied at each given limit state.
Resistance factors
- STRENGTH limit states, see LRFD 5.5.4.2
- For all other limit states, = 1.00
751.32.3 Details
751.32.3.1 Front Sheet
Note: | The following are details and dimensions for the plan view of a typical pile cap bent on the front sheet of the bridge plans. Details and dimensions for an encased concrete pile cap bent are similar. |
Details for unsymmetrical roadways shall require dimensions tying Centerline Lane to Centerline Structure. |
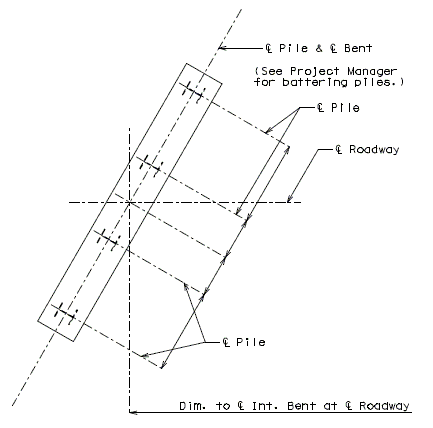
751.32.3.2 Typical Pile Cap Bent
![]() | |
Part Elevation | Part Section |
---|---|
Applicable for both HP piles (shown) and CIP piles |
![]() |
Use 2'-6" minimum or as determined by the superstructure requirements or the minimum support length required for seismic criteria (expansion joint bents only) (3" increments) or the minimum beam width required to meet pile edge distance requirement. |
![]() |
= 3’-0” (Min.) for Wide Flange, Double-Tee Girders, Prestressed Girders and Plate Girders. |
![]() |
Check the clearance of the anchor bolt well to the top of pile. Increase the beam depth if needed. |
![]() |
If the depth at the end of the beam, due to the steps, exceeds 4'-6", the beam bottom should be stepped or sloped. |
![]() |
Use 3/4" drip groove where expansion device is located at bent. Continue to use 1-1/2" clear to reinforcing steel in bottom of beam. 3/4" drip groove shall be formed continuously around all piling at 3" from edge of beam. |
![]() |
Minimum of 3 piles at 10'-0" cts., maximum spacing (1" increments). |
![]() |
Piles shall not be battered. |
751.32.3.2.1 Sway Bracing
(Use when specified on Design Layout or when required by design.)
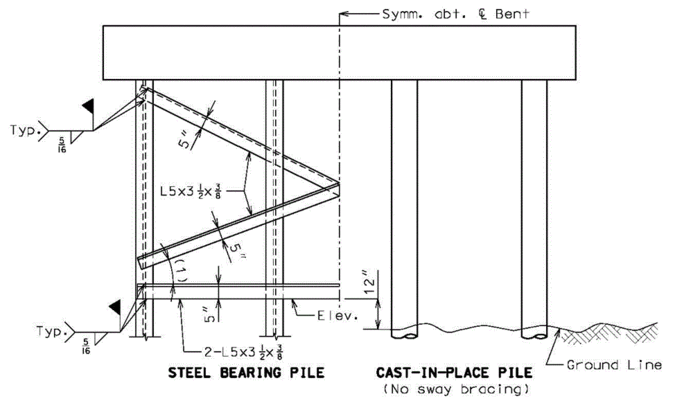
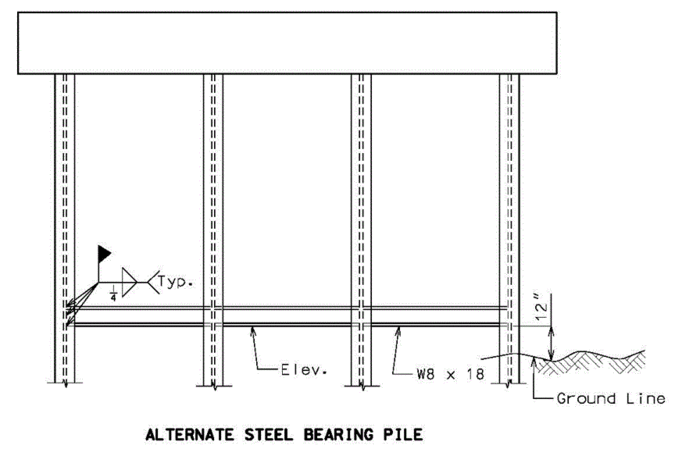
Guidance for use of sway bracing for steel bearing pile:
(1) When angle slope of bracing becomes less than 15° to the horizontal, omit the diagonal angles and use the horizontal angles only (except on four pile bents, then use alternate shown above).
Note: In case of a large number of piles, see the Structural Project Manager.
751.32.3.3 Encased Pile Cap Bent
Consideration shall be given to EPG 751.1.2.20 Substructure Type before using this type of structure.
![]() |
![]() |
Part Section |
---|
![]() |
Use 2'-6" minimum or as determined by the superstructure requirements or the minimum support length required for seismic criteria (expansion joint bents only) (3" increments) or the minimum beam width required to meet pile edge distance requirement. |
![]() |
= 3’-0” (Min.) for Wide Flange, Double-Tee Girders, Prestressed Girders and Plate Girders. |
![]() |
Check the clearance of the anchor bolt well to the top of pile. Increase the beam depth if needed. |
![]() |
If the depth at the end of the beam, due to the steps, exceeds 4'-6", the beam bottom should be stepped or sloped. |
![]() |
Height by design. Embed encasement 2 ft. (min.) below the top of the lowest finished groundline elevation, unless a greater embedment is required for bridge design. |
![]() |
Minimum of 3 piles at 10'-0" cts., maximum spacing (1" increments). |
751.32.3.4 Closed Concrete Intermediate Diaphragms
See EPG 751.22.3.7.4 Bent Details for intermediate bent details required for closed concrete intermediate diaphragms.
751.32.4 Reinforcement
751.32.4.1 Typical Pile Cap Bent
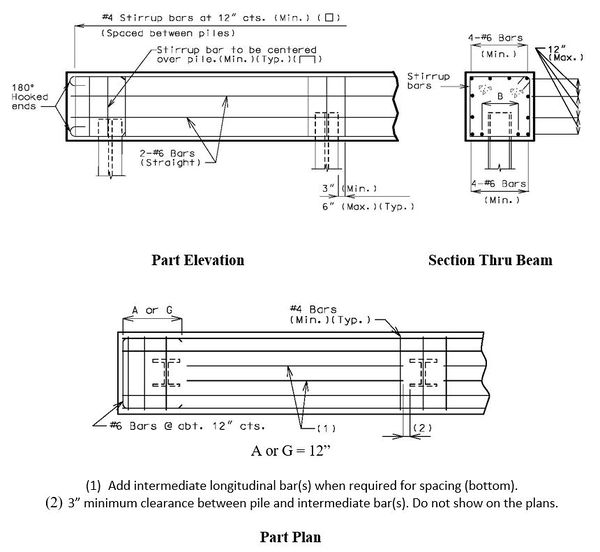
Note: | Locate #4 bars "![]() ![]() |
For epoxy coated reinforcement requirements, see EPG 751.5.9.2.2 Epoxy Coated Reinforcement Requirements. Details of protective coating and sloping top of beam to drain shall be used when below an expansion device. | |
When dimension “B” is required to be greater than 15” to clear piles by 1 ½”, typical when HP14 and CIP14 or larger diameter piles are used, add intermediate longitudinal bar(s) between piles. The spacing between intermediate bar(s) and full length bars shall not be greater than required by crack control provisions. Ends of intermediate bar(s) shall be hooked. |
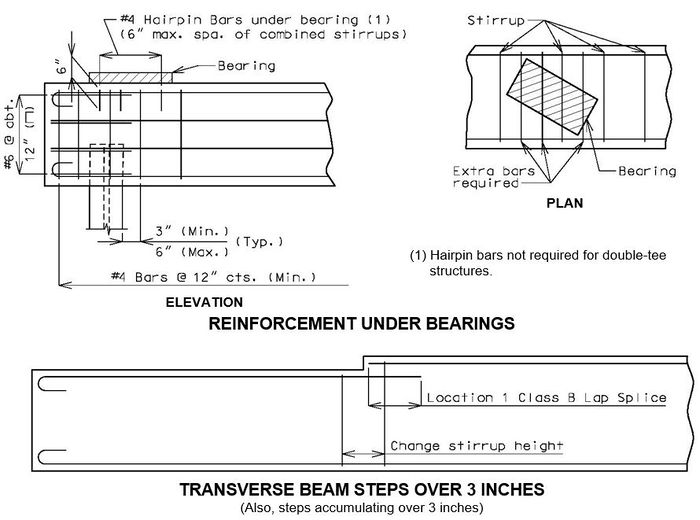
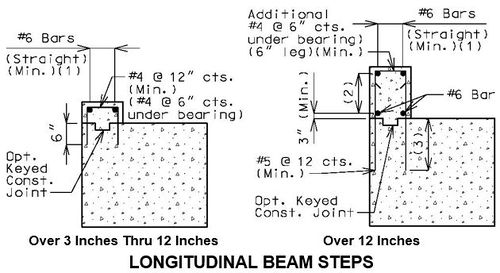
- (1) 6” (Max.), add #6 bars as needed.
- (2) 9” (Max.), add #6 bars at each face as needed.
- (3) Location 2 development length, f'c = 3 ksi:
- 21" (uncoated)
- 32" (epoxy coated)
See EPG 751.5.9.2.8 for development and lap splice lengths not given or lengths for scenarios other than those shown. Provide standard hooks if required.
751.32.4.2 Encased Pile Cap Bent
Supplemental details for encased pile cap bents are provided.
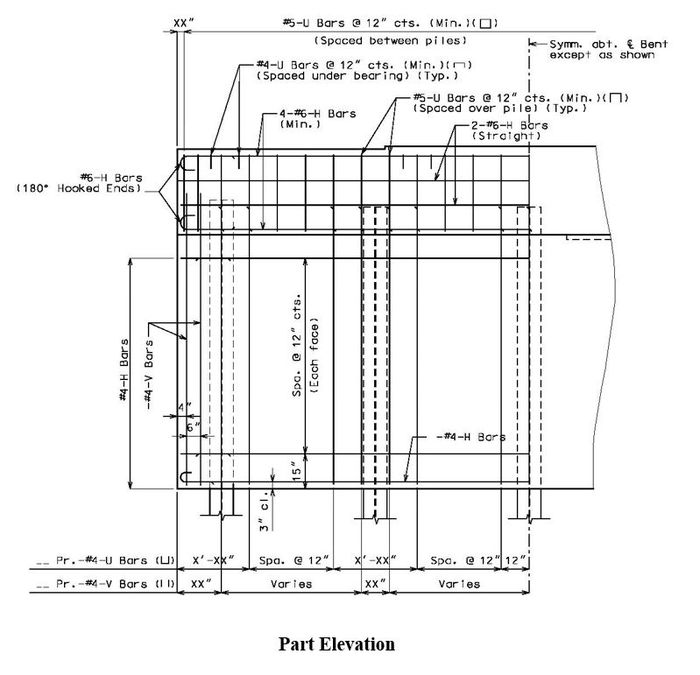
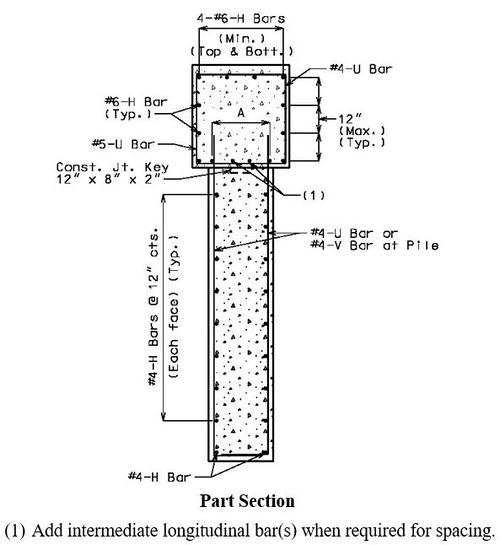
Note: | When dimension “A” is greater than 18” add intermediate longitudal bar(s) between piles. Ends of bar(s) shall be hooked. Keep 3” minimum clearance between the pile and intermediate bar(s) and do not show on the plans. |
![]() |
Part Plan |
Note: | Locate #4 bars "![]() ![]() |
For epoxy coated reinforcement requirements, see EPG 751.5.9.2.2 Epoxy Coated Reinforcement Requirements. Details of protective coating and sloping top of beam to drain shall be used when below an expansion device. |