Category:712 Structural Steel Construction
Steel Girder Bridge, Testing, Load Rating |
Report 1999 |
See also: Innovation Library |
Approved Products |
Qualified Protective Coatings for Machined Finished Surfaces |
712.1 Construction Inspection for Sec 712
The important feature of structural steel inspection include such items as:
- (a) inspection of handling, unloading, storing, and erecting of the various members to make sure they are not subjected to excessive stress
- (b) erection with proper camber, adequately supported

- (c) use of the required number of pins and erection bolts to hold all members rigidly in place
- (d) welding or bolting in such a manner that the designed stress and desired appearance is maintained. Any high strength bolts used as temporary erection bolts must be replaced with new permanent bolts.
Successful structural steel erection work will directly relate to skill of the workmen and thoroughness of the inspector. Welders must be qualified by passing required tests. Even though no tests are required for the bolting crew, the inspector has authority to insist that an experienced crew be used.
Fabrication Inspection Reports for structural steel and other metal products such as hand rail and similar fabrication are made by the Bridge Division shop inspector. Copies of this report are mailed to the resident engineer. The inspector should examine the report and study the remarks section. When steel arrives, check it against the list of corrections required of the fabricator, as noted on the report. The shop inspector often depends on field inspection to assure that shop corrections were made prior to shipment. Should material arrive with corrections not made, the inspector should immediately inform the contractor that material will not be accepted until corrections are completed. Refer to EPG 1080 Structural Steel Fabrication for more information regarding shipping releases and fabrication inspection reports.
712.1.1 Expansion Joints
Expansion joints include all devices by which expansion due to temperature is dissipated within the joint instead of being transmitted to adjacent elements. Expansion joints will normally be provided for bridge superstructure steel, bridge decks and handrails. For this instruction, joints in floors and handrails will also be considered.
Prior to Setting Expansion Joints:
- Check vertical and horizontal dimensions.
- Check condition of joint upon delivery and provision for storage until installation.
- Check filler material for closed joints.
- Compute temperature correction.
During Construction:
- Set joints according to temperature correction.
- Align finger type joints exactly to ensure free movement without lateral contact.
- If compressible fill material is specified, joints to be filled must be clean and all paint or rust adhering to the structural steel must be removed to obtain necessary adhesion for a waterproof joint. Provide bottom support to prevent it from falling out of the joint, if loosened.
- Where the plans call for sealing of joints with hotpoured rubber-asphalt type compound, special care and equipment are required to obtain a satisfactory job. Heating of joint material must be done in a special double boiler kettle. Temperature of the material should be maintained at or very near that specified by the manufacturer. The joint must be dry and cleaned with air just ahead of the actual pouring operation. The joint should also be poured high to allow for settlement and contraction of joint material as it cools.
- If sleeve type joints are specified, as in handrails, set the inside element symmetrically with outside so that no localized friction will prevent free action of the sleeve.
- No material shall be allowed to enter the joint to prevent its free movement.
After Construction:
- After normal dead load has been taken by all elements of the structure, check freedom of movement.
- Check final position of joint against computed position for the current temperature.
- Remove any foreign material which may have entered the joint during construction.
712.1.2 Expansion And Contraction Computations
Expansion joints at ends of continuous units should be set carefully for elevation and opening, as well as checking the meshing of fingers in finger joints. Joint openings are given on bridge plans for a specified temperature, usually 60° F. Should the joint be set at a temperature other than specified, the opening must be adjusted. The coefficient of expansion of steel is 0.0000065 per degree F. Suppose for instance, that a joint opening is given as 1-1/8 in. at 60° F and the sum of the distances each side of the joint to the adjacent fixed shoes in the bridge is 165 ft. Assume temperature of the structural steel to be 95° F when this joint is set. The correction is found by multiplying the difference in degrees coefficient of expansion of steel; that is:
- (95° - 65°) x 165 ft. x 0.0000065 per degree
- = 35 x 165 x 0.0000065
- = 7/16 in.
Since the temperature when setting the joint was greater than 60° F, at which the joint was computed, the correction of 7/16 in. should be deducted if the joint is to give 1-1/8 in. opening at 60°. The opening at which the joint should be set at 95° would be 1-1/8 in. less 7/16 in. or 11/16 in. Likewise if the temperature at which the joint is set should be lower than that given on the plans, the correction should be added to the joint opening to give the required opening at plan temperature. Both sides of each joint should be set in place and checked for alignment and fit before any permanent connections are made to either side to ensure: (1) smooth riding surface, (2) proper depth of concrete slab, and (3) a joint which will operate correctly with expansion and contraction movements of the bridge.
For bearing devices, specified temperatures will be used as the basic temperature on which to base an allowance for expansion or contraction. Rockers and rollers should be vertical and masonry plates in a neutral position for full dead load at this specified temperature. The masonry plates shall be placed in this position for all degrees of temperature but the rockers shall be tipped in the proper direction and the rollers placed in the required position to compensate for the amount of expansion or contraction of steel at the time they are placed.
712.1.3 Bearings
Bearings are devices for transferring superstructure loads to bridge seats. They include masonry bearing plates, elastomeric pads, shoes, rockers, rollers, and combinations of them some of which may be teflon coated. Anchors are the means of preventing movement of bearing devices on bridge seats and include anchor bolts, bars, or structural shapes. Earthquake retainers are provided on some bridges to prevent the bearing devices from moving off the bearing area.
Prior to setting of Bearings or Anchorage:
- Check vertical and horizontal dimensions.
- Check condition of bearing upon delivery and provisions for storage until installation.
- Inspect bridge seats to ensure that they are finished to receive bearings.
- If anchorages have been cast in place during construction of bridge seat, check for accuracy.
- Compute temperature correction.
During Construction:
- Anchor bolt wells which are formed will be detailed on the bridge plans typically. Holes for anchor bolts may be drilled as a contractor option and will be noted on the plans typically. Either wells or holes must be kept free of water in freezing weather.
- Position of anchor bolts with respect to expansion bearing details shall correspond with the position indicated for the temperature at time of erection.
- Formed wells or drilled or formed holes will be backfilled after anchors are set with non-shrink grout completely filling the space in the hole.
- Correct any irregularities in bearing plate areas of bridge seat.
- Set bearing plates in exact position with full uniform bearing on contact surface.
- Unless otherwise specified, contact surfaces shall be painted in accordance with the specifications. Compressed rubber and fabric pads shall be placed under the bearing plates as shown on the plans.
- Rocker or roller, if used, shall be set in the position dictated by temperatures at time of setting.
- Where expansion bearings include sliding plates of different coefficients of friction, care must be taken not to reverse the position of the two plates with respect to each other and to the bridge seat.
712.1.4 Welding
712.1.4.1 Field Welding
712.1.4.1.1 Field Welder Cards
Specifications require that field welders shall be certified by an established facility with an accredited American Welding Society (AWS) certification program defined in the current AWS Standard QC4. Welders shall be certified per the current QC7 Standard for AWS Certified Welders. The code of acceptance shall be AWS D1.5: Bridge Welding Code for welding of steel products and AWS D1.2: Structural Welding Code-Aluminum. Welders who have successfully completed the certification program will be issued an AWS Welder Card. AWS also has an agreement with the Ironworkers Union that allows them to be accredited test facilities for Ironworkers Union members that meet the same requirements of QC4 and QC7. A copy of the AWS Welder card and the Ironworkers Union card are shown:
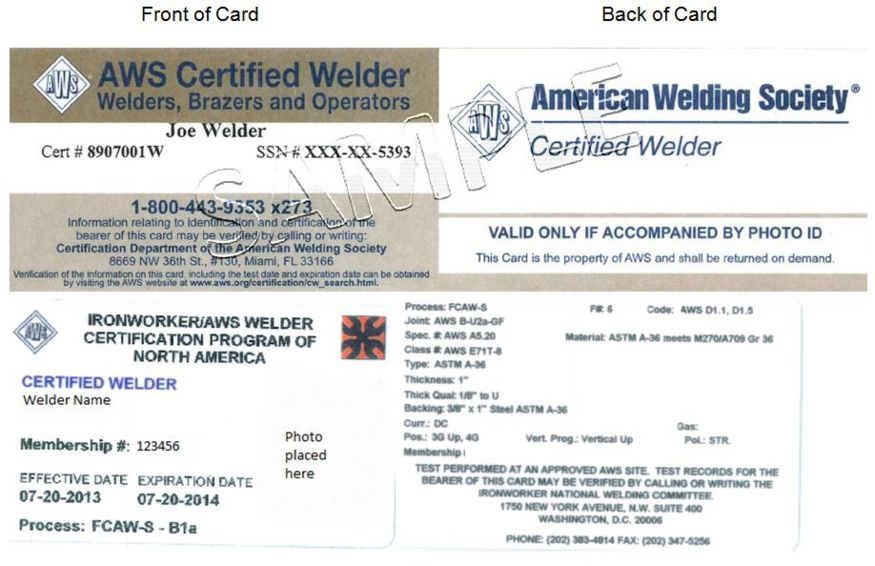
The AWS website has a link that provides guidance on interpreting the information that is shown on the back of the cards furnished by both AWS and the Ironworkers Union. A link to the AWS website that provides both locations of accredited test facilities (ATF) and interpretation of the welder card information is available.
MoDOT field welder cards that were issued prior to June 30, 2013 are still permissible for use on MoDOT projects until the expiration date on the card. If there are questions regarding the validity of a MoDOT field welder card, the Bridge Division should be contacted to confirm if the welder certification is valid. MoDOT personnel will no longer be required to complete and submit a “MoDOT Welder Qualification Report” to the Bridge Division.
AWS certification shall be considered in effect indefinitely provided that the welder remains active in the process that they are qualified for without an interruption greater than six months and there is no specific reason to question the welder’s ability to produce quality welds. Certification maintenance is the responsibility of the welder and shall be presented to the engineer upon request. The welder shall present a copy of their AWS or Ironworkers Union card to the engineer prior to welding. Welders that have tested within six months of welding on a project may have a temporary certification letter provided by the test facility that may be used while the card is being produced. Certification maintenance shall be in accordance with AWS QC7 and the supplement QC7G. Questions regarding the validity of temporary cards may be directed to the Construction and Materials Division.
If the engineer has reason to question the ability of the welder, a retest should be requested. Retests shall be conducted by an AWS accredited test facility.
712.1.4.1.2 Field Welding Minimum Certifications
For inspection purposes some of the specific types of work and the minimum required position certification are as shown in the following table:
Type of Work | Required Position Certification |
---|---|
Steel Pile Splices (HP & Shell Piles) | 2G |
Steel Pile Points (HP & Shell Piles) | 2G |
Stay-in-Place Form Support Angles | None |
Girder/Beam Flanges to Bearing Plates | 2G |
Stiffeners | 3G |
Anything else not listed | 3G unless otherwise specified by the Engineer. |
A welder qualified for one position also qualifies for performing other welds as shown in the following table:
Certified Position | Qualified to Perform |
---|---|
1G | 1F, 2F, 1G |
2G | 1F, 2F, 1G, 2G |
3G | 1F, 2F, 3F, 1G, 2G, 3G |
4G | 1F, 2F, 4F, 1G, 4G |
3G & 4G | All Groove and Fillet Positions |
1F | 1F |
2F | 1F, 2F |
3F | 1F, 2F, 3F |
4F | 1F, 2F, 4F |
3F & 4F | All Fillet Positions |
KEY: 1=flat, 2=horizontal, 3=vertical, 4=overhead, G=groove, F=fillet |
Examples of the weld positions for groove welds and fillet welds are as follows:
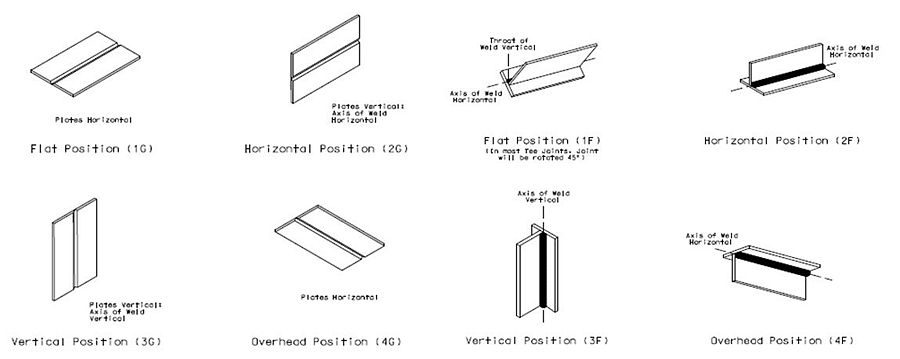
In most cases, a welder may elect to take one of two test plate thicknesses. A limited thickness test will be taken on a 3/8 in. test plate. This will qualify a welder for groove welds of a maximum plate thickness of 3/4 in. and fillet welds on plates of unlimited thickness. An unlimited thickness test will be taken on a 1 in. thick plate and qualifies the welder for unlimited plate thickness for both groove welds and fillet welds. The welder’s card that is to be presented at the job site will show both the test plate thickness as well as the plate thickness limitations.
712.1.4.1.3 Shear Connector Welding
Current practices by the contractor utilize the installation of shear connectors by field personnel. Most shear connector welding is completed by an automated welding process. AWS does not have a qualification procedure established in QC7. Instead, welders are to be qualified in accordance with AWS D1.5 Clause 7.7 by MoDOT field personnel. Shear connector welders may be qualified by conducting a preproduction test. This test involves the welder welding two shear connectors to a test plate or to the production plate. The test specimens shall be visually inspected to ensure a full 360° weld. After the welds have cooled, the shear connectors are then bent to an angle of approximately 30° from the original axis by either striking with a hammer or placing a pipe over the shear connector and then bending. If the shear connector does not exhibit a complete weld or a failure occurs in the weld of either shear connector, the welder shall adjust the automatic welding machine and retest on a separate weld test plate. The welder may not retest on the actual production plate.
Before shear connector production welding in the field begins with a particular welder set-up, a specific shear connector size or type, and at the beginning of production for a particular shift or day, a preproduction test shall be conducted. The preproduction test is to be conducted on the first two shear connectors welded to the production plate or may be conducted on a separate test plate of the same thickness (+/- 25%). The acceptance method is the same as given earlier for the welder test.
Once shear connector production welding has commenced, any welds that do not exhibit the full 360° weld may be repaired using a 5/16 in. fillet weld for shear connector diameters up to one inch and 3/8 in. for diameters greater than one inch. The repair weld shall extend 3/8 in. beyond the end of the area to be repaired.
712.1.4.1.4 Acceptable Field Welding Processes
MoDOT permits only two specific welding processes for field welding on steel bridges. These processes are shielded metal arc welding (SMAW or commonly known as stick welding) and flux cored arc welding (FCAW). The preferred method for field welding is SMAW. SMAW on steel products that will be coated are to be welded with E7018, low hydrogen electrodes. SMAW on uncoated steel products (weathering steel) should be welded with E8018, low hydrogen weathering steel electrodes. FCAW on steel products should be completed with a self-shielded process where no shielding gas is used. This will be noted on the welder’s card as FCAW-S. Gas shielding for FCAW should be discouraged due to the additional requirements to provide protection of the weld area from gas dispersion caused by the wind.
Welding of aluminum products in the field may be completed using gas metal arc welding (GMAW or commonly known as MIG welding) or with SMAW with special aluminum electrodes. Like FCAW welding using gas shielding, the weld area must be protected to prevent shielding gas dispersion when welding with GMAW. GMAW is the preferred method of welding aluminum by AWS. However, SMAW may be used provided that special care is taken during welding to control the welding parameters and that all welding slag is removed.
712.1.4.2 Shop Welding
Fabrication shops shall qualify welders in accordance with the governing welding code for the specific process as required in Sec 1080.3.3.4. It is the responsibility of the fabrication shop’s quality control personnel to ensure that the welder’s test documentation and period of effectiveness are documented and maintained. The Bridge Division maintains a list of welder certifications for shop welders for facilities that material is inspected by the Bridge Division.
712.1.5 High Strength Bolts (Sec 712.7)
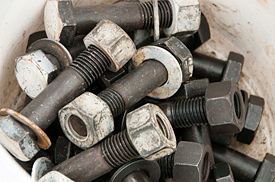
Bolts, nuts, and washers must meet applicable requirements of AASHTO as noted in Sec 1080.2. AASHTO M164 has been removed from service and AASHTO refers back to ASTM A325 for high strength bolts. ASTM A325 bolts shall be used on bridge connections unless other types of bolts are specified in the contract. To facilitate easy identification of high strength bolts, the following figure shows some of the typical markings that ASTM requires by their specification.
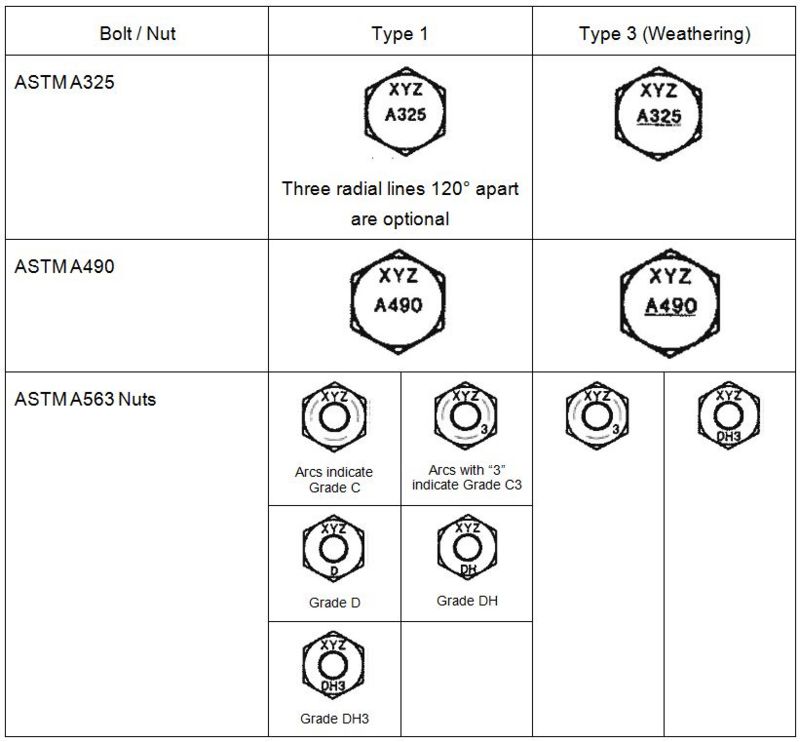
Note: XYZ represents the manufacturer’s identification mark.
A permissible alternate type of nut may be furnished. Such nuts would be marked with the symbol 2 or 2H and the manufacturer's symbol.
Bolts tightened by the calibrated wrench or turn-of-nut method should be checked following the procedures outlined in the Standard Specifications.
The sides of bolt heads and nuts tightened with an impact wrench will appear slightly peened. This will indicate that the wrench has been applied to the fastener.
712.1.5.1 Bolted Parts
Sec 712.7.1 covers cleaning of parts to be bolted. Bolts, nuts, and washers will normally be received with a light residual coating of lubricant. This coating is not considered detrimental to friction type connections and need not be removed. If bolts are received with a heavy coating of preservative, it must be removed. A light residual coating of lubricant may be applied or allowed to remain in the bolt threads, but not to such an extent as to run down between the washer and bolted parts and into the interfaces between parts being assembled.
712.1.5.2 Bolt Tension
A washer is required under nut or bolt head, whichever is turned in tightening, to prevent galling between nut or bolt head and the surface against which the head or nut would turn in tightening, and to minimize irregularities in the torque-tension ratio where bolts are tightened by calibrated wrench method. Washers are also required under finished nuts and the heads of regular semi-finished hexagon bolts against the possibility of some reduction in bearing area due to field reaming. When oversized holes are used as permitted by the contract, a washer shall be placed under both the bolt head and the nut.
Standard Specifications require that bolt torque and impact wrenches be calibrated by means of a device capable of measuring actual tension produced by a given wrench effort applied to a representative sample. Current specifications require power wrenches to be set to induce a bolt tension 5 percent to 10 percent in excess of specified values but the Special Provisions for the project should be checked for a possible revision to this requirement.
The contractor is required to furnish a device capable of indicating actual bolt tension for the calibration of wrenches or load indicating device. A certification indicating recent calibration of the device should accompany it. It is recommended that the certification of calibration be within the past year but if the device is being used with satisfactory results, the period may be extended. More frequent calibration may be necessary if the device receives heavy use over an extended period.
The contractor will generally use either the calibrated wrench method or the turn-of-nut method for tightening bolts as outlined in Sec 712.7. The sides of bolt heads or nuts tightened with an impact wrench will appear slightly peened. This will usually indicate that the wrench has been applied to the fastener. If the wrench damages the galvanized coating, the contractor shall repair the coating by an acceptable method.
712.1.5.3 Rotational-Capacity Testing and Installation of A325 Type 3 High Strength Bolts
Type 3 (weathering steel) bolts behave quite differently than the galvanized bolts used in most MoDOT structures and require additional care to test and install properly.
The contractor must keep bolts stored in sealed kegs out of the elements until ready for use. Storage in a warehouse, shed, shipping container or other weatherproof building is best. The lubricant used on Type 3 bolts dissipates quickly, allowing rust to begin. Kegs should not be opened until absolutely necessary and promptly resealed whenever work stops.
If bolts fail the rotational-capacity test, insufficient lubrication is the most likely cause. Relubrication of A325 bolts is allowed. Several different waxes and lubricants are suggested by FHWA, including Castrol 140 Stick Wax (which has been successfully field tested by MoDOT), Castrol Safety-Film 639, MacDermid Torque’N Tension Control Fluid, beeswax, etc.
For long bolts (L>8d), consider reducing the rotational-capacity turn-of-nut requirement to 1-1/6 turn if bolts fail at 1-1/3 turn. FHWA’s Procedure for Performing Rotational Capacity Test was revised in February 2005 to include this change, which was adopted from ASTM A325-04b (AASHTO M 164).
Galling of the washer may occur, especially with longer bolts. This can be reduced by lubricating the contact area of the bolt face at the washer with an approved lubricant. If this face is lubricated for testing, it must also be lubricated during bolt installation.
Failure of the bolts due to galling of the washer can also be prevented by turning the nut in one continuous motion during testing. For larger diameter bolts, this can be a problem. Torque multipliers amplify this effect. If many larger diameter bolts will be tested, ask the contractor to purchase an electric gear reduction wrench with reaction arm. The Skidmore will need to have a reaction kit installed. This wrench will produce better results and save time spent performing tests (and, therefore, lower costs).
For long bolts, (L>8d), use proper spacer bushings on the back of the Skidmore to avoid excessive use of spacers between the washer and front plate of the Skidmore. Stacking spacers can cause bending of long bolts, which will cause inaccurate results, false failures and potential damage to the Skidmore. Consult the Skidmore user manual for maximum allowable spacer lengths.
712.1.6 Non-destructive Testing
In certain instances, non-destructive testing (NDT) may be required to be conducted on steel components of a bridge. The contractor will be responsible for providing and certified NDT technician to conduct the testing. This technician will usually be an employee of a third party inspection agency. Certification for NDT technicians will be in accordance with the requirements of The American Society for Nondestructive Testing (ASNT) Recommended Practice SNT-TC-1A. MoDOT does not maintain an approved list of NDT technicians. The Bridge Division does review certifications for testing agencies and keep a list of personnel of these agencies with their respective certifications.
For projects that require NDT in the field, the inspector should collect the information from the contractor as to who will be providing the NDT services. The inspector should then contact the Bridge Division to determine if the NDT technician’s certifications have been reviewed. If the certifications have not been reviewed, the contractor should submit the certifications to the Resident Engineer to be forwarded to the Bridge Division. These certifications should include, as a minimum, the technicians test scores, work experience, and annual eye exam results.
At the Resident Engineer’s option, they may choose to keep a list of personnel who have performed NDT work for a quick reference for future projects. However, the Resident Engineer and the inspector should always request to see the current eye exam results prior the technician providing the NDT on these future projects.
712.2 Materials Inspection for Sec 712
712.2.1 Scope
This guidance establishes procedures for inspecting and reporting those items specified in Sec 712 that are not always inspected by Bridge Division personnel or are not specifically covered in the Materials details of the Specifications.
712.2.2 Procedure
Normally all materials in Sec 712 will be inspected by Bridge Division personnel. Bolts, nuts and washers accepted by PAL may be delivered directly from the manufacturer to the project without prior inspection. When requested by the Bridge Division or construction office, the Construction and Materials Division will inspect fencing and other miscellaneous items. The Bridge Division is responsible for the inspection of shop coating of structural steel at fabricating plants.
712.2.2.1 Project Inspection and Sampling for PAL
Inspecting of PAL material will be as stated in this section and Pre-Acceptance Lists (PAL).
712.2.3 Miscellaneous Materials
712.2.3.1 High Strength Bolts
All bolts, nuts, and washers should be from a PAL supplier in accordance with Pre-Acceptance Lists (PAL). If a supplier proposes to furnish structural steel connectors and is not on PAL, a request is to be made to the Construction and Material Division for acceptance into the PAL program. Once satisfactory submittals have been received, the supplier will be placed on the PAL. Bolts, nuts, and washers, for use other than bridge construction and in quantities less than 50, may be accepted from a PAL supplier without a PAL identification number.
712.2.3.1.1 Manufacturer's Certification. Bolts and nuts specified to meet the requirements of ASTM A307 shall be accompanied by a manufacturer's certification statement that the bolts and nuts were manufactured to comply with requirements of ASTM A307 and, if required, galvanized to comply with requirements of AASHTO M232 (ASTM A153) or were mechanically galvanized and meet the coating thickness, adherence, and quality requirements of AASHTO M232 (ASTM A153) Class C. Certification shall be retained by the shipper. A copy should be obtained when sampling at the shipper and submitted with the samples to the lab.
All bolts, nuts and washers are to be identifiable as to type and manufacturer. Bolts, nuts, and washers manufactured to meet ASTM A307 will normally be identified on the packaging since no special markings are required on the item. Dimensions are to be as shown on the plans or as specified.
Weight (mass) of zinc coating, when specified, is to be determined by magnetic gauge in the same manner as described for bolts and nuts in EPG 1040 Guardrail, End Terminals, One-Strand Access Restraint Cable and Three-Strand Guard Cable Material.
Samples for Laboratory testing are only required when requested by the State Construction and Materials Engineer, or when field inspection indicates questionable compliance. Samples shall be taken according to EPG 712.2.3.2.1.1 ASTM A307 Bolts.
712.2.3.1.2 High strength bolts, nuts, and washers specified to meet the requirements of ASTM A325. Field inspection shall include examination of the certifications or mill test reports; checking identification markings; and testing for dimensions. The certifications or mill test reports, conforming to EPG 712.2.3.1.1 Manufacturer's Certification, shall be retained in the district office. Samples for Laboratory testing shall be taken and submitted in accordance with EPG 712.2.3.2.1.2 ASTM A325 Bolts.
712.2.3.2 PAL Manufacturer Facilities Sampling
Prior to visiting a PAL supplier or manufacturer facility, the Cognos report “PAL Shipments Within Date Range” should be run for the facility to determine what material has been given MoDOT PAL numbers. For each PAL material, the sample shall consist of six pieces rather than determined from lot quantities as given in the following sections. An individual sample shall consist of bolts, nuts, or washers as these are treated as different materials in the PAL system.
712.2.3.2.1 Sample sizes
712.2.3.2.1.1 ASTM A307 Bolts
Samples for Laboratory testing are only required when requested by the State Construction and Materials Engineer, or when field inspection indicates questionable compliance. When samples are taken, they are to be taken as shown in the following table. When galvanized bolts, nuts and washers are submitted to the Laboratory, a minimum of 3 samples of each are required for Laboratory testing.
3 for lots of 0 to 800 pcs. | Each sample is to consist of one bolt, nut and washer. Submit for dimensions, weight (mass) of coating, mechanical properties. |
6 for lots of 801 to 8,000 pcs. | |
9 for lots of 8,001 to 22,000 pcs. | |
15 for lots of 22,001+ pcs. |
712.2.3.2.1.2 ASTM A325 Bolts
Samples for Laboratory testing shall be taken and submitted as follows: All lots containing 501 or more, high strength bolts shall be sampled and submitted to the Laboratory for testing. If no lot offered contains 501 or more bolts, sample 10 percent of the lots offered, or one lot, whichever is greater. A lot is defined as all bolts of the same size and length, with the same manufacturer's lot identification, offered for inspection at one time. Samples shall be taken as follows:
Number of Bolts in the Lot | Number of Bolts Taken for a Sample* |
---|---|
150 and less | 3 |
151 through 800 | 3 |
801 through 8,000 | 6 |
8,001 through 22,000 | 9 |
22,001 plus | 15 |
* A minimum of 3 samples will be required for galvanized materials. |
All lots containing 501 or more, high strength nuts shall be sampled and submitted to the Laboratory for testing. If no lot offered contains 501 or more nuts, sample 10 percent of the lots offered or one lot, whichever is greater. A lot is defined as all nuts of the same grade, size, style, thread series and class, and surface finish, with the same manufacturer's lot identification, offered for inspection at one time. Samples shall be taken as follows:
Number of Nuts in the Lot | Number of Nuts Taken for a Sample* |
---|---|
800 and under | 1 |
801 through 8,000 | 2 |
8,001 through 22,000 | 3 |
22,000 and over | 5 |
* A minimum of 3 samples will be required for galvanized materials. |
All lots containing 501 or more, high strength washers shall be sampled and submitted to the Laboratory for testing. If no lot offered contains 501 or more washers, sample 10 percent of the lots offered, or one lot, whichever is greater. A lot is defined as all washers of the same type, grade, size and surface finish, with the same manufacturer's lot identification, offered for inspection at one time. Samples shall be taken as follows:
Number of Washers in the Lot | Number of Washers Taken for a Sample* |
---|---|
800 and under | 1 |
801 through 8,000 | 2 |
8,001 through 22,000 | 3 |
22,000 and over | 5 |
* A minimum of 3 samples will be required for galvanized materials. |
712.2.3.2.2 Bolts for Highway Lighting, Traffic Signals or Highway Signing
Bolts, nuts, and washers for highway lighting, traffic signals, or highway signing shall meet the requirements given in EPG 712.2.3.1.2 High Strength Bolts. Samples for Central Laboratory testing are only required when requested by the State Construction and Materials Engineer or when field inspection indicates questionable compliance.
712.2.3.3 Slab Drains
Slab drains are to be accepted on the basis of field inspection of dimensions, weight (mass) of zinc coating, and a satisfactory fabricators certification. The dimensions, weight (mass) of zinc coating, and material specification requirements are shown on the bridge plans.
Field determination of weight (mass) of coating is to be made on each lot of material furnished. The magnetic gauge is to be operated and calibrated in accordance with ASTM E376. At least three members of each size and type offered for inspection are to be selected for testing. A single-spot test is to be comprised of at least five readings of the magnetic gauge taken in a small area and those five readings averaged to obtain a single-spot test result. Three such areas should be tested on each of the members being tested. Test each member in the same manner. Average all single-spot test results from all members to obtain an average coating weight (mass) to be reported. The minimum single-spot test result would be the minimum average obtained on any one member. Material may be accepted or rejected for galvanized coating on the basis of magnetic gauge. If a test result fails to comply with the specifications, that lot should be resampled at double the original sampling rate. If any of the resampled members fail to comply with the specification, that lot is to be rejected. The contractor or supplier is to be given the option of sampling for Laboratory testing, if the magnetic gauge test results are within minus 15 percent of the specified coating weight (mass).
A fabricators certification shall be submitted to the engineer in triplicate stating that "The steel used in the fabrication of the slab drains was manufactured to conform to ASTM A709" or "A500, A501" as the case may be.
712.2.3.4 Miscellaneous Structural Steel
Other structural steel items not requiring shop drawings also require inspection. Inspection includes a fabricator's certification identifying the source and grade of steel, as well as verification of dimensions and inspection of any coating applied. The report is to include the grade of steel, coating applied, and results of inspection.
712.3 Lab Testing
712.3.1 Scope
This establishes procedures for Laboratory testing and reporting samples of structural steel, bolts, nuts, and washers and for welding qualifications.
712.3.2 Procedure
712.3.2.1 Chemical Tests - Bolts, Nuts, and Washers
Weight (mass) of coating shall be determined in accordance with AASHTO M232. Chemical analysis of the base metal shall be determined, when requested, according to [[Category:1020 Corrugated Metallic-Coated Steel Culvert Pipe, Pipe-Arches and End Sections#1020.8 Laboratory Testing Guidelines for Sec 1020|Laboratory Testing Guidelines for Sec 1020. Original test data and calculations shall be recorded in Laboratory workbooks.
712.3.2.2 Physical Tests - Bolts and Nuts
Original test results and calculations shall be reported through SiteManager.
Low carbon steel bolts and nuts shall be tested according to ASTM A307. Tests are to be as follows:
- (a) Bolts shall be tested for dimensions, hardness, and tensile strength.
- (b) Nuts shall be tested for dimensions, hardness, and proof load.
Due to the shape and length of some bolts and the shape of some nuts, it may not be possible or required to determine the tensile strength of the bolts or the proof load of the nuts.
High strength bolts, nuts, and washers shall be tested according to ASTM A325. Tests are to be as follows:
- (a) Bolts shall be tested for dimensions, markings, hardness, proof load, and tensile strength.
- (b) Nuts shall be tested for dimensions, markings, hardness, and proof load.
- (c) Washers shall be tested for hardness.
Due to the shape and length of some bolts and the size of some nuts, it may not be possible or required to determine the proof load and tensile strength of the bolts or the proof load of the nuts.
712.3.3 Sample Record
The sample record shall be completed in SiteManager, as described in Sample Record General Information , and shall indicate acceptance, qualified acceptance, or rejection. Appropriate remarks, as described in EPG 106.20 Reporting, are to be included in the report to clarify conditions of acceptance or rejection.
Test results for bolts, nuts and washers shall be reported through SiteManager.
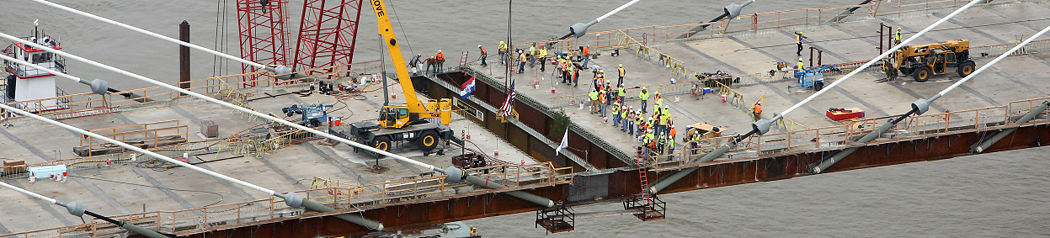