617.3 Material Inspection for Sec 617
This article establishes procedures for inspecting, accepting and reporting of protective coating for concrete bents and piers (urethane and epoxy), concrete and masonry protective systems, sacrificial graffiti protection system and temporary coating for concrete bents and piers (weathering steel). This article establishes procedures for inspecting and reporting concrete median barriers. Reinforcing steel, concrete curing material, mortar for grout and portland cement concrete shall be inspected in accordance with the corresponding sections of the Engineering Policy Guide. Refer to Sec 617 for MoDOT’s specifications. Fabrication of cast-in-place median barriers is inspected and reported by Construction and Materials.
617.3.1 Apparatus
- (a) Micrometer capable of measuring to 0.0001 in. and accurate to within at least 0.001 in.
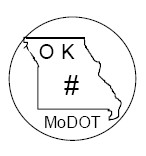
- (b) Rule with suitable graduations to accurately measure the material to be inspected.
- (c) Magnetic gauge, reading range 0-40 mils (0-1000 m).
- (d) OK - MoDOT stamp.
- (e) Weather resistant marking materials.
617.3.2 Procedure
Acceptance of precast concrete median barriers is to be based on the inspection of materials being incorporated into the sections, compressive tests on cured concrete cylinders and inspection of the finished section, including amount and placement of reinforcement.
617.3.2.1 Materials
The inspector shall ensure that only inspected and approved materials are used in the fabrication of concrete median barriers. The fabricator shall submit a proposed portland cement concrete mixture for approval. The District Construction and Materials Engineer shall ensure that the proposed mix meets the designated requirements.
617.3.2.2 Forms
The inspector shall ensure that forms and formwork comply with the applicable requirements of Sec 0617, Sec 0703, Standard Plan 617.10 and Standard Plan 617.20.
617.3.2.3 Placement of Reinforcement
The inspector shall ensure that the placing and tying of reinforcing bars conform to the applicable requirements of Sec 706, Standard Plan 617.10, Standard Plan 617.20 and that all reinforcing steel is properly placed and are clear and free. All reinforcing steel shall be checked to ensure that it is free from form oil or other material that might serve as a bond breaker.
617.3.2.4 Placing and Consolidating Concrete
The inspector shall ensure that the placing, consolidating, and finishing of concrete is in accordance with the applicable provisions of Sec 703.
617.3.2.5 Concrete Testing
During the placement of the portland cement concrete, tests shall be performed to ensure that the requirements of Sec 617 are met. Portland cement concrete shall be inspected and reported in accordance with EPG 501.1 Construction Inspection and EPG 501.2 Materials Inspection. Tests for determining consistency and air entrainment shall be performed. At least 2 sets of specimens for compressive strength for each pour shall be prepared in accordance with EPG 501.1 Construction Inspection and cured in the same manner as the units.
617.3.2.6 Curing
The inspector shall observe the curing operation to verify that the requirements of Sec 617 and Sec 1026 are being met. Type 1-D liquid membraneforming compound may be used in accordance with Sec 1055.2. The Type 1-D pigmented cure shall be applied at the same rate as for paving. Type 2, white pigmented curing compound, is not allowed.
617.3.2.7 Form Removal
Precast concrete members shall be cured a minimum of 12 hours after pouring before forms can be removed. The inspector at the fabricating plant is responsible for making and testing standard compressive specimens to determine when forms may be removed and curing discontinued in accordance with Sec 617. Compressive tests should be performed at the fabricating plant or an approved commercial testing laboratory. At the discretion of the District Construction and Materials Engineer, the specimens may be tested using district equipment. If questionable results are being obtained, the compressive specimens shall be submitted to the Laboratory for testing. At least one set of regular 28-day cylinders should be submitted to the Laboratory for each project to check the portland cement concrete mix design with a minimum of one set per month of operation of precast plant or as often deemed necessary. Form C-701 is to be used as an identification sheet with the distribution and title modified as required.
617.3.2.8 Marking
The inspector shall insure that each precast unit is identified with the manufacturer, location of manufacturer and year of manufacture clearly and permanently marked by indentation, plates or other suitable methods. The permanent markings should be identifiable after installation. New barriers are also required to be marked with the day and month of manufacture for yard tracking. The day and month markings may be by permanent marker that will wear off over time and will not be required when the barrier is re-used. These markings shall be located as shown on the plans. If the location of the markings is not shown on the plans, markings shall be located in such a manner that they will not be obvious or objectionable to the traveling public after the unit has been placed in its final position. The barriers shall not be accepted or shipped new from the yard if the year, month and day of manufacture are not identifiable. The barriers shall not be accepted or used on the project if the manufacturer, manufacturer location, and year of manufacture are not identifiable.
617.3.2.9 Inspection of Completed Units
The finished units are to be examined for conformance to dimensions, workmanship, and marking in accordance with Sec 617, Standard Plan 617.10 and Standard Plan 617.20. Accepted sections are to be stamped with an "OK - MoDOT" by the inspector. Minor patching will be permitted to obtain the specified texture so long as the defects to be patched do not harm the structural integrity of the unit.
617.3.2.10 Records
The plant inspector shall maintain a complete file of all data pertaining to the manufacturer of the concrete units, either at the manufacturing plant or in the district office. Complete and accurate records of each manufacturing operation should be kept in a field book. All pertinent data that in any way affects or influences the construction procedures or completed members shall also be recorded in the field book. Data shall be entered in the field book as soon as it is known. Field notes shall not be copied but shall be kept exactly as they are originally recorded.
617.3.3 Report
Materials shall be reported as shown in the applicable sections of this article. Appropriate remarks, as described in EPG 106.20 Reporting are to be included in the report to clarify conditions of acceptance or rejection.
When precast median barriers are delivered to a given project, the units shall be reported through SiteManager and shall contain one of the following statements as appropriate:
- "These median barriers have been surface sealed."
- "These median barriers have not been surface sealed."
Report copies normally forwarded to the Resident Engineer shall be furnished to the Inspector at the precast manufacturing plant. The reports shall be marked "General" and the name of the precast concrete manufacturer must be shown. The material is to be shown for use in "Precast Concrete Units." The plant inspector located at the concrete proportioning plant shall furnish a plant inspector's daily report through SiteManager for each day's pour identifying the units manufactured from that pour. The name of the manufacturer or set-up must be shown. The original copy of this report shall be forwarded to the State Construction and Materials Engineer. The duplicate copy shall be furnished to the District Construction and Materials Engineer supervising operations at the manufacturing plant. The plant inspector shall retain the triplicate copy of the plant records.
When precast concrete units are delivered to a given project, the units shall be reported through SiteManager with distribution, per Class A in EPG 106.20.8 Rejected Reports.