751.22 Prestressed Concrete I Girders: Difference between revisions
m Per BR, updated links |
m Smithk moved page 751.22 P/S Concrete I Girders to 751.22 Prestressed Concrete I Girders: Per BR, renamed article to "Prestressed" instead of "P/S" |
(No difference)
|
Revision as of 07:40, 2 April 2021
Video |
Concrete Girder |
751.22.1 General
751.22.1.1 Material Properties
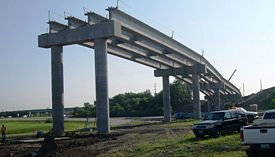
Concrete
Concrete strength utilized for prestressed girders may be conventional or high strength concrete (HSC) which shall be identified on the girder plans. HSC shall be concrete strengths in excess of 8.0 ksi and may only be used with the permission of the Structural Project Manager or Structural Liaison Engineer. Costs may increase due to production modifications necessary to obtain the required HSC strength.
Conventional concrete strength for P/S I-Girder shall be the following:
- For MoDOT Standard Girders:
- ,
- Optional higher concrete strength shall be:
- ,
- OR
- With the approval of the Structural Project Manager or Liaison:
- ,
- For NU Standard Girder:
- ,
- Modulus of Elasticity,
- Where,
- f'c in ksi
- K1 = correction factor for source of aggregate
- = 1.0 unless determined by physical testing
- K1 = correction factor for source of aggregate
Prestressing strand Type of strand: AASHTO M203 (ASTM A416) Grade 270 Uncoated, seven-wire, low-relaxation strand Ultimate tensile strength, Yield strength, Strand modulus of elasticity, For conventional concrete strengths: Strand diameter, Strand area, OR: Strand diameter, Strand area, Maximum allowed initial prestress force (immediately prior to transfer)
= fpbt = 0.75fpu kips LRFD table 5.9.2.2-1
Maximum allowed initial prestress force per strand
= Aps x fpbt kips
Maximum allowed initial force = 30.98 kips for 0.5 inch diameter strand
43.94 kips for 0.6 inch diameter strand
Total initial prestress force = (# of strands) x (required* initial prestress force per strand) * Typically the required prestress force per strand is the maximum allowed prestress force. Note: Report on the girder plans the required number of strands by design and the total initial prestress force using EPG 751.50 Standard Detailing Notes H2c1.3. Order of Material Use for Increasing Girder Capacity in Order of Increasing Costs 1. Increase concrete strength (readily producible by fabricator) 2. Increase strand size (readily available from fabricator but steel costs are high) 3. Modify MoDOT shape (most costly and inconvenient because of forming bed modifications required) (except NU shape) Mild reinforcing steel Minimum yield strength, Steel modulus of elasticity, Welded Wire Reinforcement Minimum yield strength, Steel modulus of elasticity,
751.22.1.2 Geometric Dimensions
The ratio of the depth of girder to span length will in general be not less than 1/18.
The cross sectional dimensions of the girder shall be one of the following:
- MoDOT Standard Girders:

BEAM TYPE 2 | BEAM TYPE 3 | BEAM TYPE 4 | BEAM TYPE 6 |
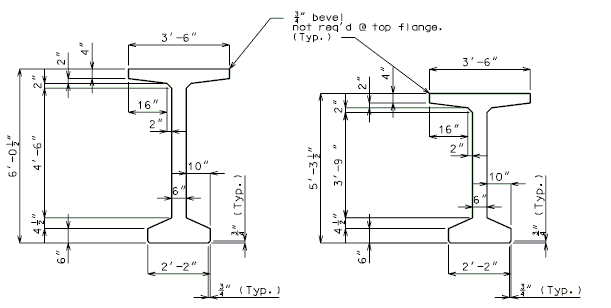
BEAM TYPE 7 | BEAM TYPE 8 |
If the web is required to be increased, then the top and bottom flanges are to be increased by the same amount. (1" increments 2" max.).
- NU Standard Girders:
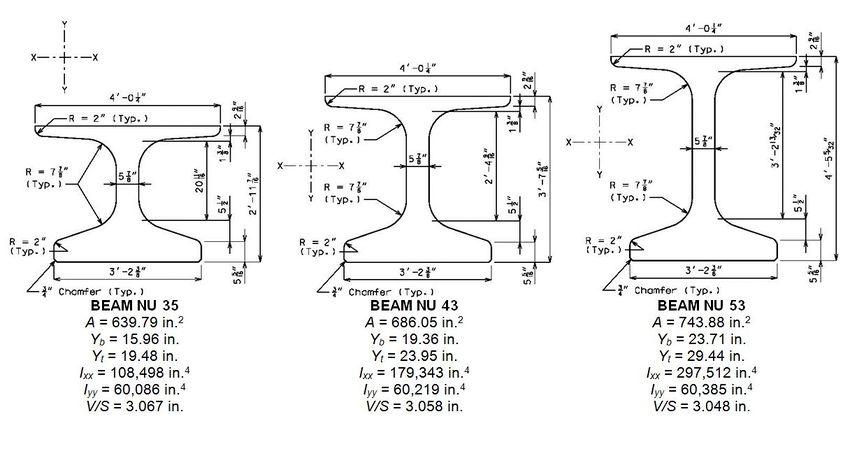
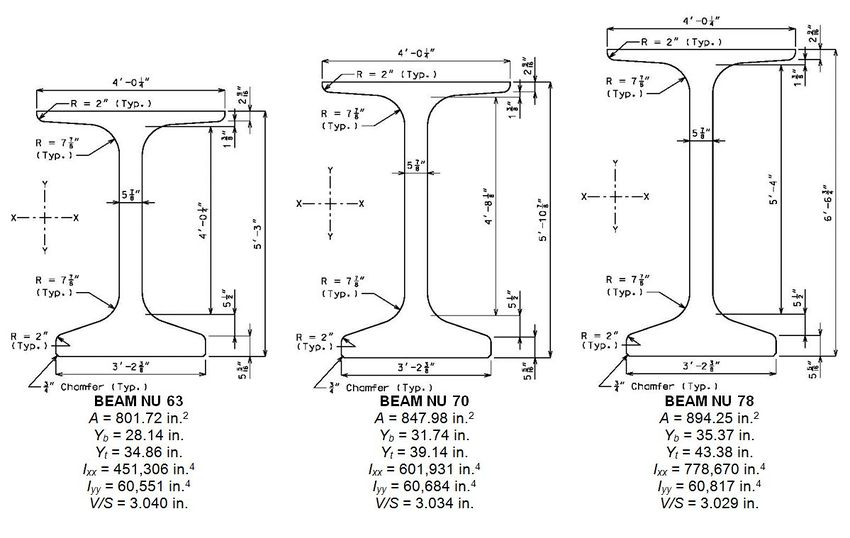
751.22.1.3 Typical Span Ranges
The following charts provide span ranges (limits) for P/S I-girders based on girder spacing and standard roadway widths.
Limitations of the Charts:
- A. Standard Concrete Charts Only
- Criteria used in determining maximum span lengths for lower conventional concrete strength:
- 1) Low-relaxation strand with 0.5” strand diameter
- 2) Concrete strengths, = 4.5 ksi and = 6.0 ksi
- 3) 3-span bridge consisting of 3 equal length girders made continuous and composite
- B. Optional Concrete Charts Only
- Criteria used in determining maximum span lengths for greater conventional concrete strength:
- 1) Low-relaxation strand with 0.6” strand diameter
- 2) Concrete strengths, = 5.0 ksi and = 7.0 ksi
- 3) 3-span bridge consisting of 3 equal length girders made continuous and composite
- C. Both Standard Concrete and Optional Concrete Charts
- Criteria used in determining span ranges for both Standard and Optional Concrete conventional strengths.
- 1) Minimum span lengths were determined by the positive moment capacity of the smallest strand arrangement per beam shape. Shorter span lengths are possible.
- 2) Based on 10 ft. design lanes. (Current design practice meets AASHTO LRFD and uses 12 ft. design lanes.)
- 3) Based on unrefined prestress loss equations. (Current design practice meets AASHTO LRFD and uses refined losses.)
Recommended Adjustments for Using the Charts:
Because the span limit charts were developed using older design criteria as noted above, increased span lengths are probable.
- 1) Span limits given in all charts should be increased 10 percent to account for current design practice. Ten percent can safely be used without a preliminary girder analysis.
- 2) Span limits given in all charts shall be increased when a preliminary girder analysis based on actual design conditions is performed which shall be noted on the Design Layout.
Span range charts are planned for future replacement. Use the recommended adjustments until implemented. |
Given Roadway Widths and Girder Spacing
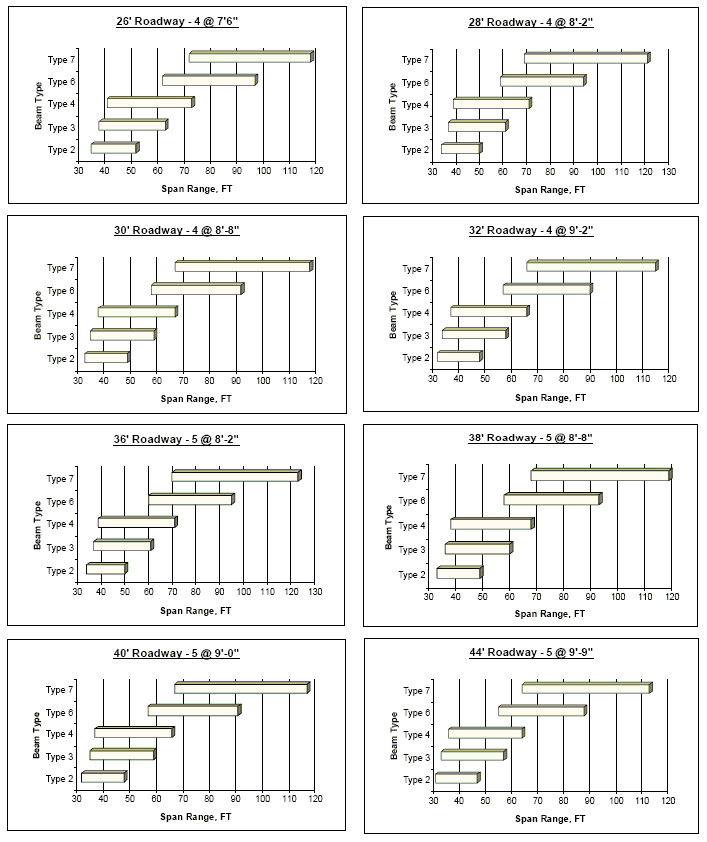
Given Roadway Widths and Girder Spacing
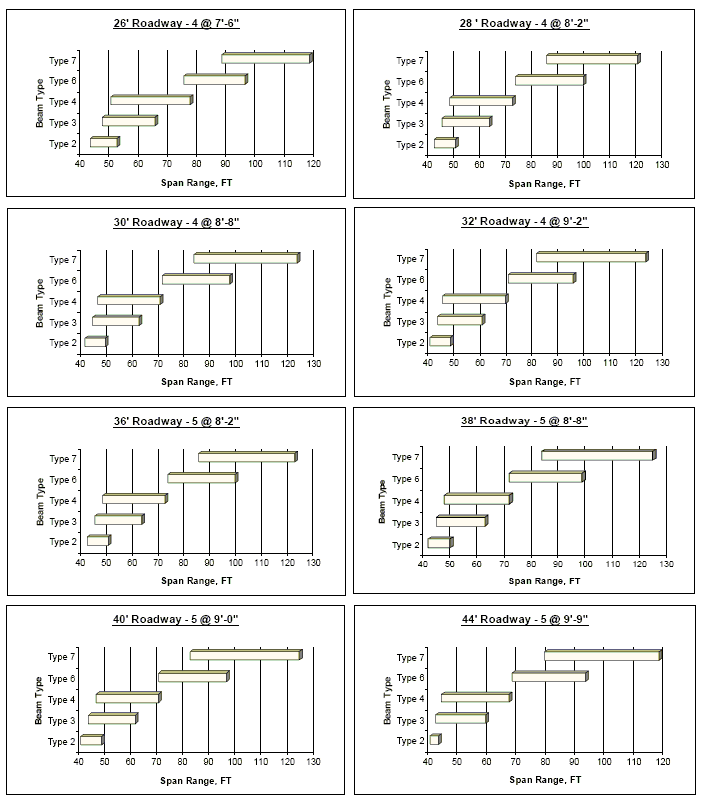
751.22.1.4 Span and Structure Lengths
751.22.1.4.1 Limits
Span Lengths
Designs using MoDOT standard Type 6 girders shall be limited to 105 feet maximum length to ensure stability during fabrication, shipping and erection.
No limits are set for other types of prestressed girders however the Structural Project Manager or Structural Liaison Engineer shall be consulted prior to the design of any unusually long prestressed girder.
Continuous Structure Lengths
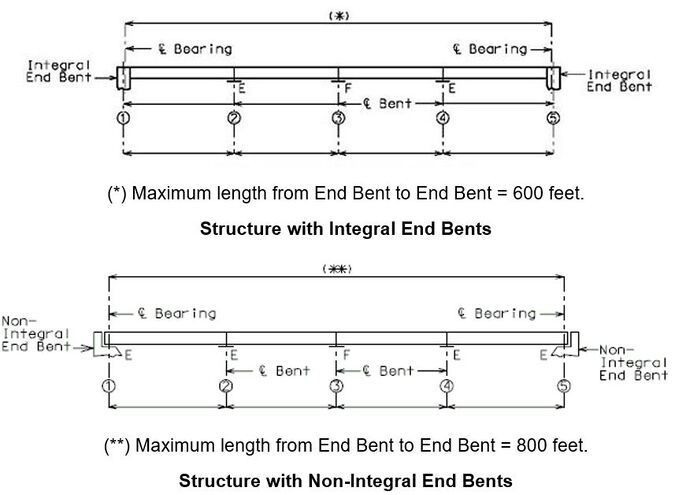
751.22.1.4.2 Girder Length and Geometric Layout
- Tangent Bridges
- Girder lengths of exterior spans (i.e., end spans) and interior spans shall be computed using the requirements shown below.
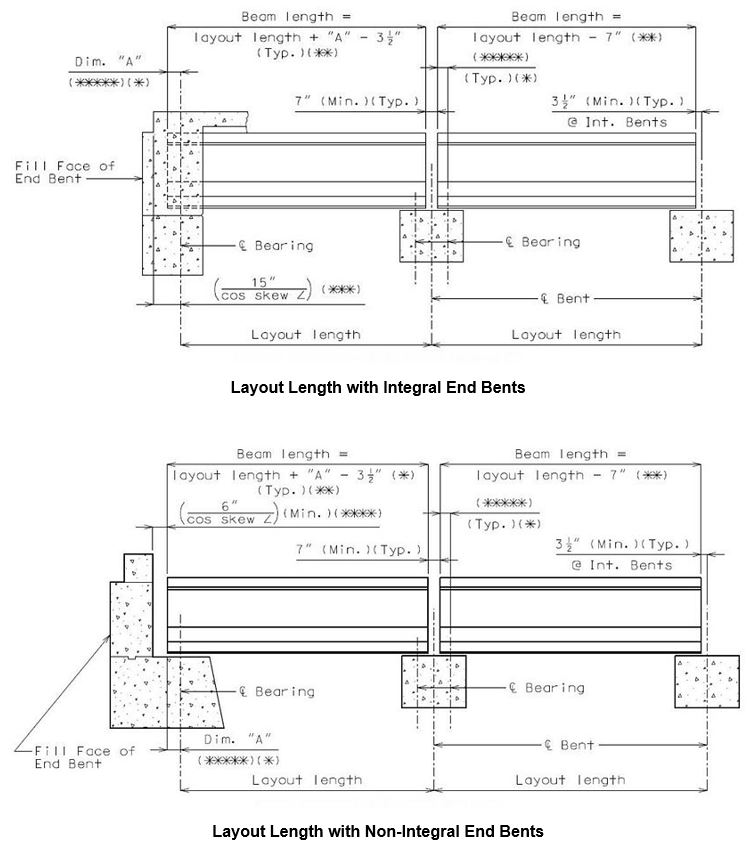
- The layout length for single span shall be measured from centerline of bearing to centerline of bearing. If the difference between layout length of the end span and interior span is within one foot, then layout length should be adjusted if possible so the girder lengths are equal for end span and interior span.
- (*) Minimum dimension from edge of bearing pad to end of girder equals one inch.
- (**) Design layout lengths are horizontal lengths. Girder lengths should be adjusted according to grade and shall be specified to the nearest 1/8 inch.
- (***) For large skews, end bent beam caps may need to be larger to provide edge distance.
- (****) Horizontal distance along certerline of girder.
- (*****) = 1” (minimum) + ½ bearing pad length which equals:
- 5” (minimum) for MoDOT standard girders and adjacent box beams,
- 3 ½” (minimum) for NU girders and spread box beams.
- (*****) = 1” (minimum) + ½ bearing pad length which equals:
- Curved Bridges
- Layout of any curved structure may be done using any coordinate geometry programs available. To layout the bridge, use the following steps:
- Start out by laying in the centerline (CL) of the survey curve.
- Locate the tie point of the bridge. This point will usually be on the CL of the survey curve but may be on a baseline which is offset a certain distance to the CL of the survey curve.
- A second tie point may be required if the skew is not measured to the CL of roadway at the bridge tie point. If this is the case, establish the tie point at the specified station and plot the skew line at the required angle.
- Next, on the centerline of structure or baseline curve, locate the station of the CL of bent for each intermediate bent and the fill face for the end bents. Once these points are located, plot lines through these stations parallel to skew line. Normally the layout file will specify that all bents are parallel to the skew line; however, there may be times when the bents are radial or have varying skews.
- When locating the stations in the preceding step, the distance between CL of intermediate bents are exactly the layout lengths specified on the file. However, the end spans need to follow the procedure for calculating length set forth in Tangent Bridges.
- When the CL of the intermediate bents and the fill face lines have been added, chords should be drawn connecting these points sequentially. For example, if you have a three-span bridge, chords should be drawn from the fill face of bent 1 to CL of bent 2, CL bent 2 to CL bent 3, and CL bent 3 to fill face bent 4.
- When all the chords are in, offset each girder in each span parallel to this chord. The perpendicular distance between girders will be the same for all spans, but the skew distance between girders along the bent will vary from bent to bent depending on the skew to the CL at that point. The designer needs to be aware of the fact that at an intermediate bent the distance between bearings on the approaching and leaving span sides will be different distances. These bearings will not line up across the bent and will actually diverge more the farther away they are from the CL of the survey.
- When establishing the CL of bearing points, the designer needs to allow for a minimum of seven (7) inches between ends of girders at the bents while keeping in mind that the girders will be offset and at different skews. If the offset is greater than half the girder bottom flange width, see Structural Project Manager. The distance from the end of girder to CL of bearing point should be half of the bearing length plus one inch minimum clearance. Once the distance for CL bent to CL of bearing is calculated, the designer should offset lines by that dimension on either side of the CL of bent. These lines will then be intersected with each of the girder lines to create the bearing points on each bent.
- Between the bearing points at the ends of the girders, quarter points or tenth points need to be established, depending on the girder span. These points will be used in calculating the haunch and bottom of slab elevations for the bridge deck.
- The bridge deck and barrier or railing can be laid in by offsetting the centerline of roadway to each side by the proper distance. Curves should be laid in to designate both the inside and outside edges of the barrier or railing. These will later be useful in laying in the wings and end bents.
- After the outside edge of slab curves are plotted, the curve offsets need to be found. The intersection points of the outside edge of slab and the centerline of each bent or fill face can be connected with chords. The distance between these chords and their partner curves need to be calculated at five-foot intervals beginning at the center point of each chord.
- Joints are placed in the barrier or railing at each bent. These joints are placed perpendicular to the centerline of the roadway through the intersection point of the centerline bent and the inside edge of barrier or railing.
- Wing layout length is given on the profile sheets in the layout file. An arc should be struck so as to intersect the inside edge of barrier or railing the specified length from a point at the intersection of the fill face and the inside edge of barrier or railing. This point will mark the end of the wing which is perpendicular to the centerline of the roadway.
- The vertical curve information needs to be added so a program can calculate the elevations at the desired stations. After this is done, the designer can request any of the following information which will be needed:
- Stations and elevations of all points
- Offset distances to the chords
- Lengths of girders
- Distances between bearings
- Angles between girders and each bent
- Lengths of bents
- Lengths of barrier or railing between joints
- Minimum vertical clearance.
751.22.1.4.3 Coping of Girder Ends
Non-Integral end bents with skews greater than 40 degrees shall always have girder ends coped. Skews less than 40 degrees shall have girder ends coped on case by case basis. It is preferable to not cope across the web.
Check clearance from fill face of integral end bents to bottom flanges of NU girders. Maintain 3-inch minimum clearance. Coping may be permitted with approval of the Structural Project Manager or Structural Liaison Engineer.
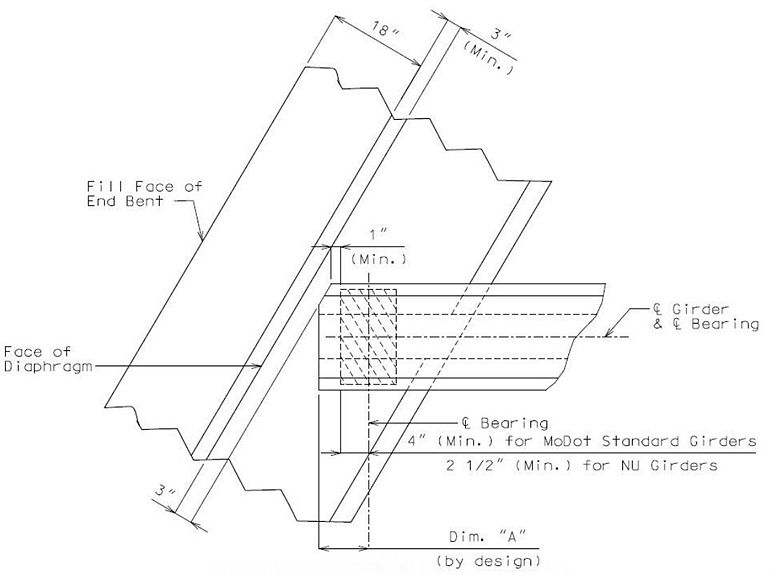
751.22.1.5 Constant and Varied Joint Filler Loads
Varied joint filler load
The prestressed I-girder should first be designed assuming that the contractor will vary the joint filler supporting the panels on the girder flange. This assumption will maintain the minimum slab/panel combination thickness of 8 1/2”, and will eliminate the possibility of increased load due to varying slab thickness.
Constant joint filler load
With the girder designed and the camber and haunching dimensions calculated, the girder should be checked assuming the contractor will use a constant 1” joint filler. This will cause the slab thickness to vary due to camber of the girder, increasing load. This additional load shall be placed as a concentrated load at 1/8 point from each end of the girder.
An example of how this concentrated load could be calculated is shown as follows:
- Load
- Determine the concentrated load* to girders by distributing w transversely across the girders. If the minimum haunch is greater than 1” joint filler, the additional haunch shall be included in the slab thickness as a uniform load. If the use of these loads causes the girder design to change, it shall be the responsibility of the designer to determine if the camber and haunching should be recalculated.
This load shall be positioned at the 1/8 point from centerline of bearing pad.
The girder and bearing designs should be checked for the constant joint filler option and constant joint filler load. However, camber, haunching and beam seat elevations shown on the plans should be based on the variable joint filler option.
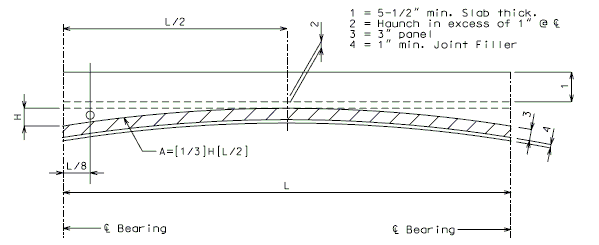
751.22.2 Design
751.22.2.1 Load Combinations
In general, each component shall satisfy the following equation:
Where:
= Total factored force effect | |
= Force effect | |
= Load modifier | |
= Load factor | |
= Resistance factor | |
= Nominal resistance | |
= Factored resistance |
- Limit States
The following limit states shall be considered for P/S Girder design:
- SERVICE I - for compressive stress
- SERVICE III - for tensile stress
- STRENGTH I
See LRFD Table 3.4.1-1 for Loads and Load Factors applied at each given limit state.
- Resistance factors,
STRENGTH limit states, see LRFD Article 6.5.4.2 & 5.5.4.2
For all other limit states, = 1.00
See EPG 751.2.3.1 Load Modifiers.
751.22.2.2 Prestressing Strands
Transfer Length of Prestressing Strands
The prestressing force may be assumed to vary linearly from zero at the point where bonding commences to a maximum at the transfer length. The transfer length may be taken as 60 times the strand diameter.
Development Length of Prestressing Strands
The development length for prestressing strands shall be taken as:
Where: = Nominal diameter of strand, (in.) = Average stress in prestressing strand at the time for which the nominal resistance of the girder is required, (ksi)
Stress limits for prestressing strands
Strand stress at service limit state shall not exceed the following:
At jacking:
- ksi
- (For typical girders and fabrication economy, )
At service limit state after all losses:
- ksi
Where:
= Stress in prestressing strand at jacking, (ksi) | |
= Effective stress of strand after all losses, (ksi) | |
= Yield strength of strand, (ksi) | |
= Ultimate tensile strength of strand, (ksi) |
Prestress Losses
Refined estimates of time-dependent losses are used, based on AASHTO LRFD Article 5.9.3.4, as opposed to approximate lump sum estimate of losses in AASHTO LRFD Article 5.9.3.3.
The prestress losses shall be calculated to investigate concrete stresses at two different stages.
- Temporary stresses immediately after transfer:
- Final stresses
SERVICE I and SERVICE III Limit states shall be investigated at each stage.
Harped Strands
Harped strands, although they add to the shear strength of the girder, are primarily used to keep the girder stresses (both top and bottom) within allowable limits while developing the full capacity of the girder at midspan.
Harped strands should be held down at points of 0.4 of the distance from each end of the girder. Distances along girder to hold-down devices and between hold-down devices should be reported on the plans to the nearest inch. Per Sec 1029, precaster may position hold-down devices +/- 6 in. longitudinally from position shown on the plans.
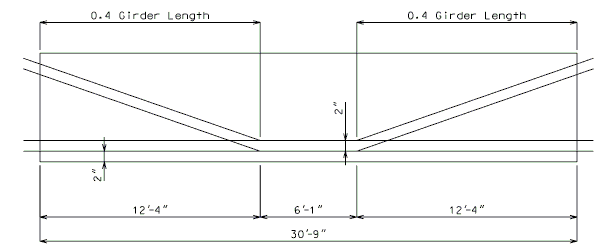
The jacking force applied to prestress strands produces an excessive vertical uplift in short spans on tall girders resulting in failure of harped strand hold-downs. The allowable limits for hold-downs are as follows:
- 5 kip/strand
- 10 kip/bolt
- 42 kip/hold-down
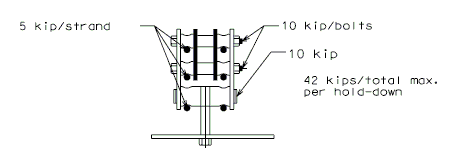
If necessary lower harped strand end location to meet criteria or use straight strands only. Investigate the possibility of using all straight strands when strength check of a hold-down device exceeds allowable.
Straight Strands.
Short spans (<40 ft.) are to use straight strands only for all girders greater than 2'-8" tall. Use at least two straight strands at the top of the girder when straight strands are used. Where straight strands only will not work a single hold-down point may be used. Note: A single point hold-down has twice the uplift force.
Strand Arrangement Optimizing
Using all straight strands for girder lengths less than 70 ft. should be investigated for MoDOT Standard Girder Types 6, 7, 8 and all NU Standard Girders in order to reduce risk of strand or hold-down breakage, increase safety by reducing risk of injury during fabrication and reduce cost.
Consider using the same section for all spans. This permits the use of shorter girders in the casting bed with longer girders, even if straight strands are needed, in the top flanges of the girders. They can be placed at either end of the bed and still optimize the usage of the bed.
Consider using the same number of draped strands for all spans and debond where needed. Strand patterns should be similar between long and short spans. For example, the designer should not use a single column of draped strands on the short spans and two columns of draped strands on the long spans. This will prevent optimization of the bed.
When using straight strands in the top flange of NU Girders and harped strands, lower (drop) the harped strand end locations and vertically align straight strands directly over harped strands to facilitate top flange blockout fabrication by removing interference created between straight strands placed to the outside of the harped strands and the flange blockout forms. If for any reason this is not possible, then place straight strands to the outside of the harped strands.
Debonding Strands
In all debonding operations the prestressing forces must be in such a manner as to prevent any sudden or shock loading.
Debonding a strand consists of wrapping the unnecessary strand(s) with a polyethylene plastic sleeve that prevents interaction of the strand with the concrete during casting and release which prevents any prestress force transfer.
751.22.2.3 Flexure
Flexure capacity of prestressed I-girders shall be determined as the following.
Flexural resistance at strength limit state
Where:
= | Flexural resistance | |
= | Nominal flexural resistance | |
= | Total factored moment from Strength I load combination | |
= | Flexural resistance factor as calculated in LRFD 5.5.4.2 |
Negative moment reinforcement design
P/S I-girder shall be designed as a reinforced concrete section at regions of negative flexures (i.e., negative moments).
At least one-third of the total tensile reinforcement provided for negative moment at the support shall have an embedment length beyond the point of inflection not less than the specified development length of the bars used.
Slab longitudinal reinforcement that contributes to making the precast beam continuous over an intermediate bent shall be anchored in regions of the slab that can be shown to be crack-free at strength limit states. This reinforcement anchorage shall be staggered. Regular longitudinal slab reinforcement may be utilized as part of the total longitudinal reinforcement required.
Effective Slab Thickness
An effective slab thickness shall be used for design by deducting from the actual slab thickness a 1” integral, sacrificial wearing surface.
Design A1 reinforcement in the top flange
The A1 reinforcement shall resist the tensile force in a cracked section computed on the basis of an uncracked section.
For MoDOT Standard Girders, A1 reinforcement shall consist of deformed bars (minimum #5 for Girder Type 2, 3 and 4 and minimum #6 for Girder Type 6, 7 and 8).
For NU Standard Girders, A1 reinforcement shall consist of the four 3/8-inch diameter reinforcement support strands with deformed bars added only as needed. The WWR in the top flange shall not be used for A1 reinforcement because there is insufficient clearance to splice the WWR.
Reinforcement shall be designed and spliced using f’ci in accordance with EPG 751.5.9.2.8 Development and Lap Splices.
Required steel area is equal to:
Where:
= , allowable tensile stress of mild steel, (ksi) | |
= Resultant of total tensile force computed on the basis of an uncracked section, (kips) |
Limits for reinforcement
The following criteria shall be considered only at composite stage.
Minimum amount of prestressed and non-prestressed tensile reinforcement shall be so that the factored flexural resistance, Mr, is at least equal to the lesser of:
- 1) Mcr LRFD Eq. 5.6.3.3-1
- 2) 1.33Mu
Where:
Mcr | = | Cracking moment, (kip-in.) |
Mu | = | Total factored moment from Strength I load combination, (kip-in.) |
751.22.2.4 Shear
Shear capacity of P/S I-girder should be checked along girder length and girder-slab interface.
Shear resistance at strength limit state
Where:
= | Shear resistance | |
= | Nominal shear resistance | |
= | Total factored shear from Strength I load combination | |
= | Shear resistance factor |
Nominal shear resistance
The nominal shear resistance, , shall be lesser of:
- , or
Where:
Where:
= | Nominal concrete shear resistance, (kips) | |
= | Nominal shear reinforcement resistance, (kips) | |
= | Component of prestressing force in the direction of shear force, (kips) | |
= | Thickness of web, (in.) | |
= | Effective shear depth taken as the distance measured perpendicular to the neutral axis, between the resultants of tensile and compressive forces due to flexure, (in.) | |
= | Spacing of shear reinforcement, (in.) | |
= | Factor indicating ability of diagonally cracked concrete to transmit tension | |
= | Angle of inclination of diagonal compressive stress, (degree) | |
= | 90.0, Angle of inclination of shear reinforcement to a longitudinal axis, (degree) | |
= | Area of shear reinforcement, (in.2) | |
= | Minimum yield strength of tension shear reinforcement, (ksi) |
Design sections near supports
Where a reaction force in the direction of the applied shear introduces compression into the end region of girder, the location of the critical section for shear is measured from the internal face of support a distance, dv. Otherwise, the design section shall be taken at the internal face of the support.
Where:
= effective shear depth taken as the distance, measured perpendicular to the neutral axis, between the resultants of the tensile and compressive forces due to flexure; it need not be taken to be less than the greater of 0.9de and 0.72h.
Girder regions requiring shear reinforcement
Girder shear reinforcement, usually consisting of stirrups, shall be provided where:
Where:
= | Factored shear force from Strength I load combination, (kips) | |
= | Nominal concrete shear resistance, (kips) | |
= | Component of prestressing force in the direction of shear force, (kips) | |
= = |
Shear resistance factor
0.9 for normal weight concrete |
Shear Reinforcement Limits
Minimum reinforcement
Area of shear reinforcement shall not be less than:
Where:
= | Area of shear reinforcement, (in.2) | |
= | Thickness of web, (in.) | |
= | Spacing of shear reinforcement, (in.) | |
= | Final concrete compressive strength, (ksi) |
Maximum spacing
Maximum spacing of shear reinforcement shall be determined as:
If , then
If , then
Where:
= | Effective shear depth taken as the distance measured perpendicular to the neutral axis, between the resultants of tensile and compressive forces due to flexure, (in.) | |
= | Shear stress on concrete, (ksi) | |
= | Maximum spacing of shear reinforcement, (in.) |
Shear stress on concrete shall be determined as:
Where:
= | Shear stress on concrete, (ksi) | |
= | Factored shear from Strength I load combination, (kips) | |
= = |
Shear resistance factor
0.9 for normal weight concrete | |
= | Thickness of web, (in.) | |
= | Component of prestressing force in the direction of shear force, (kips) | |
= | Effective shear depth taken as the distance measured perpendicular to the neutral axis, between the resultants of tensile and compressive forces due to flexure, (in.) | |
= | ||
= | Distance from extreme compression fiber to the centroid of tensile force in the tensile reinforcement, (in.) | |
= | Total height of girder including slab thickness, (in.) |
Girder-Slab Interface
The horizontal shear between the girder and slab shall be determined as specified in LRFD 5.7.4.4. The nominal horizontal shear resistance of the interface plane shall be taken as specified in LRFD 5.7.4.3. Minimum interface shear reinforcement shall be provided as specified in LRFD 5.7.4.2. The parameters used in determining the nominal horizontal shear resistance shall be taken as specified for a “cast-in-place concrete slab on clean concrete girder surfaces, free of laitance with surface roughened to an amplitude of 0.25 inch.”
The interface shear shall be resisted by extending and anchoring the vertical shear reinforcement into the slab. If the resistance provided by extending the vertical shear reinforcement is inadequate then additional U-bars may be provided as shown for a MoDOT Standard Girder Type 7 in EPG 751.22.3.6 Girder Reinforcement.
For NU Girders the edges of the top of girder flange are intentionally debonded (see figure below) and shall not be included when determining the nominal horizontal shear resistance. See EPG 751.50 Standard Detailing Notes H2c2.10 for specifics about the debonded width for NU Girders. Similarly, for all other prestressed girders, the joint filler width supporting precast panels shall be considered debonded and excluded when determining the interface resistance.
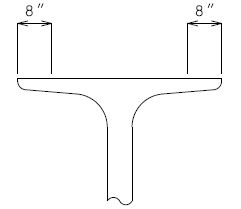
Pretensioned anchorage zones
The bursting resistance of anchorage zones provided by vertical reinforcement (i.e., B2 bars, WWF, G402 bars) in the ends of prestressed girders at the service limit state shall be taken as:
Where:
= | Stress in mild steel not exceeding 20 ksi | |
= | Total area of vertical reinforcement located within a minimum distance of h/4 from the end of the girder where h is overall depth of precast member as shown below. | |
= | Prestressing force immediately prior to transfer |
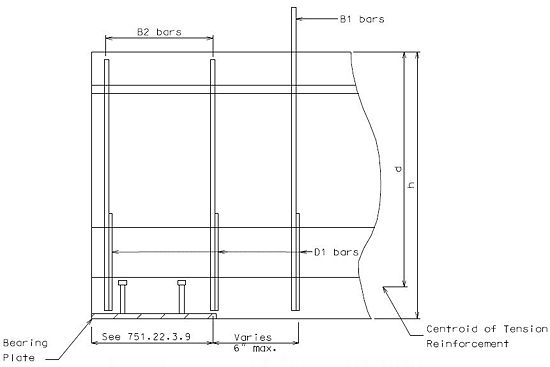
Confinement reinforcement
Reinforcement (i.e., D1 bars or G301 bars, not shown) shown in the figure above shall be placed to confine the prestressing strands in the bottom flange for a minimum distance of 1.5d from the end of beam.
The reinforcement shall not be less than #3 deformed bar, with spacing not exceeding 6.0 inches and shaped to enclose the strands.
MoDOT extends the use of D1 and G301 bars for the full length of girders.
751.22.2.5 Deformations
Criteria for deflection
For investigating maximum absolute deflection, all design lanes shall be loaded, and all supporting components should be assumed to deflect equally.
For composite design, the design cross-section should include the entire width of the roadway and the structurally continuous portions of railings, sidewalks, and median barriers. Note that barrier and railing are usually discontinuous over the bents. For skewed bridges, a right cross-section may be used.
Service I load combination shall be used. Dynamic load allowance shall be applied.
See EPG 751.2.4.2 Live Load Deflection Limits.
Calculation of deflection and camber
Deflection and camber calculations shall consider all internal loads (i.e., prestressing, concrete creep, and shrinkage) and external loads such as dead loads and live loads.
Camber is an upward displacement caused by moment due to prestressing forces. Deflection is a downward displacement due to external loads. Therefore, both camber and deflection shall be considered in making an appropriate adjustment for final profile grade on the bridge.
Initial camber at transfer at midspan
Total initial camber at transfer due to self-weight of girder and prestressing forces shall be determined as:
Where:
= Initial camber at transfer | |
= Deflection due to self-weight of girder | |
= Camber due to prestressing straight strands | |
= Camber due to prestressing harped strands |
Note: Positive and negative values indicate downward and upward displacements, respectively.
Camber at midspan after strand release (Estimated at 7 days)
Theoretical camber of girder after strand release due to self-weight of girder and prestressing forces shall be determined at 7 days as:
Where:
= Camber at 7 days after strand release with creep | |
= Time - dependent camber due to creep at 7 days |
Note: Camber is calculated 7 days after strand release to allow sufficient time for inspection. See EPG 1029 Fabricating Prestressed Concrete Members for Bridges.
Camber at midspan after erection (Estimated at 90 days)
Theoretical camber of girder after erection due to self-weight of girder and prestressing forces shall be determined at 90 days as:
Where:
= Camber at 90 days after strand release with creep | |
= Time - dependent camber due to creep at 90 days |
Final camber at midspan after slab is poured
Total deformation after slab is poured can be determined as the sum of theoretical camber of girder after erection (90 days) and deflections due to slab and concentrated loads (haunch, diaphragms, etc.) before composite action between slab and girder.
Where:
= | Final camber after slab is poured | |
= | Deflection due to weight of slab | |
= | Deflection due to concentrated loads (haunch, diaphragms, etc.) |
Final camber along span length
Deformations along the span length can be approximately determined as a product of final camber at midspan times correction factors.
= | 0.3140 at span fraction of 0.10 | |
= | 0.5930 at span fraction of 0.20 | |
= | 0.7125 at span fraction of 0.25 | |
= | 0.8130 at span fraction of 0.30 | |
= | 0.9520 at span fraction of 0.40 | |
= | 1.0000 at span fraction of 0.50 |
Calculation of camber (upward) using transformed properties
Camber at midspan due to strand forces is determined by the following:
For straight strands (groups determined by debonding lengths),
Where:
Where:
= Total prestressing force of straight strand group just prior to transfer, (kips) | |
= Distance between centerlines of bearing pads, (in.) | |
= Debond length of straight strand group from end of girder, (in.) | |
= Initial concrete modulus of elasticity based on , (ksi) | |
= Moment of inertia of transformed non-composite section computed based on , (in.4) | |
= Eccentricity between centroid of straight strand group (CSS) and center of gravity of transformed non-composite section (CGB) as shown in Figure below, (in.) | |
= Prestressing force in the strand just prior to transfer, (ksi) | |
= Summation of the time dependent losses (7 or 90 day). Losses include relaxation, creep and shrinkage, but exclude elastic shortening. |
Gross properties may be used to calculate losses and is consistent with AASHTO LRFD 5.9.3.4.
For two-point harped strands,
Where:
Where:
= Total prestressing force of harped strands just prior to transfer, (kips) | |
= Length between harped points, (in.) | |
= Eccentricity between centroid of harped strands (CHS) and center of gravity of transformed non-composite section (CGB) at midspan as shown in Figure below, (in.) | |
= Eccentricity between centroid of harped strands (CHS) and center of gravity of transformed non-composite section (CGB) at the end of girder as shown in Figure below, (in.) |
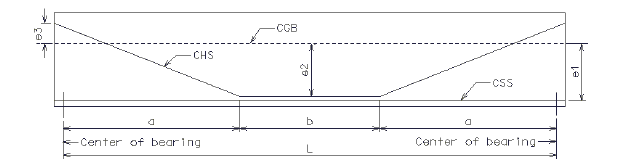
Calculations of deflections (downward)
Deflections at midspan due to dead loads are determined as the following: For self-weight of girder,
Where:
- = Uniform load due to self-weight of girder, (kip/in.)
For self-weight of slab,
Where:
- = Uniform load due to self-weight of slab, (kip/in.)
- = Final concrete modulus of elasticity based on f'c, (ksi)
- = Moment of inertia of transformed non-composite section based on Ec, (in.4)
Weight of additional slab haunch may be treated as uniform or concentrated load as appropriate. Diaphragm weight should be treated as concentrated load.
For one concentrated load at midspan,
For two equal concentrated loads,
Where:
= Concentrated load due to diaphragm and/or additional slab haunch, (kips) | |
= Distance from the centerline of bearing pad to the applied load, P, (in.) |
Creep coefficient | LRFD 5.4.2.3.2 |
Research has indicated that high strength concrete (HSC) undergoes less ultimate creep and shrinkage than conventional concrete.
Creep is a time-dependent phenomenon in which deformation increases under a constant stress. Creep coefficient is a ratio of creep strain over elastic strain, and it can be estimated as follows:
= | |
= | |
= | |
= | |
= |
Where:
= Creep coefficient. | |
= 70, Average annual ambient relative humidity | |
= Maturity of concrete, (days) Use 7 days for camber design after strand release Use 90 days for camber design after erection | |
= Age of concrete when a load is initially applied, (days) Use 0.75 days for camber design. | |
= Volume-to-surface area ratio, (in.) | |
= Initial girder concrete compressive strength, (ksi) |
751.22.3 Details
751.22.3.1 Reinforcement Criteria
Minimum Concrete Cover
- 2.0" (Min.) to centerline of strands
- 1.0" for stirrups
Minimum Bend Diameter for Stirrups
- #3 through #5 bars = 4.0 x Nominal Bar Diameter.
- Deformed wire larger than D6 = 4.0 x Nominal Wire Diameter
Minimum Spacing of Reinforcement Bars and Wires
For precast concrete, the clear distance between parallel bars in a layer shall not be lesser than:
- Nominal Bar Diameter or Nominal Wire Diameter
- 1.33 x Maximum Aggregate Size
- 1.0"
Minimum Spacing of Prestressing Strands
Spacing between each pretressing strand shall not be less than the larger of:
- A clear distance of 1.33 x Maximum Aggregate Size
- Center-to-center spacing of 2" for 0.6" strand diameter
- Center-to-center spacing of 1.75" for 0.5" strand diameter
751.22.3.2 MoDOT Standard Girders
751.22.3.2.1 Beam Type 2 Dimensions/Strand Arrangements

GIRDERS 2A THRU 2C
= 310.9 SQ. IN. |
GIRDER 2A
(11 STRANDS) |
GIRDER 2B
(12 STRANDS) |

= 310.9 SQ. IN. = 14.08 IN. |
GROUP I |
![]() GROUP II |
Numbers shown on girders relate to strand locations. |
ATTENTION: Location of harped strands shown in top flange are at end of girder and harped strands in bottom flange are at centerline.
If the web thickness is required to be increased, then the top and bottom flanges are to be increased by the same amount. (1" increments, 2" max.)
751.22.3.2.2 Beam Type 3 Dimensions/Strand Arrangements

GIRDERS 3A THRU 3B
= 381.9 SQ. IN. |
GIRDER 3A
(11 STRANDS) |
GIRDER 3B
(12 STRANDS) |
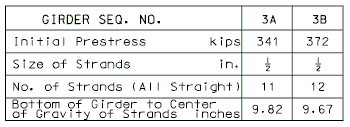
Note: Investigate the possibility of using all straight strands when strength check of a hold-down device exceeds allowable. Strand arrangements shown for Girders 3A thru 3B have straight strands only. Strand arrangements other than those shown may be investigated by the designer. |

= 381.9 SQ. IN. = 17.08 IN. |
GROUP I |
![]() GROUP II |
Numbers shown on girders relate to strand locations. |
ATTENTION: Location of harped strands shown in top flange are at end of girder and harped strands in bottom flange are at centerline.
If the web thickness is required to be increased, then the top and bottom flanges are to be increased by the same amount. (1" increments, 2" max.)
751.22.3.2.3 Beam Type 4 Dimensions/Strand Arrangements

GIRDERS 4A THRU 4C
= 428.9 SQ. IN. |
GIRDER 4A
(10 STRANDS) |
GIRDER 4B
(11 STRANDS) |
![]() GIRDERS 4C |
![]()
|

= 428.9 SQ. IN. = 19.54 IN. |
GROUP I |
![]() GROUP II |
Numbers shown on girders relate to strand locations. |
ATTENTION: Location of harped strands shown in top flange are at end of girder and harped strands in bottom flange are at centerline.
If the web thickness is required to be increased, then the top and bottom flanges are to be increased by the same amount. (1" increments, 2" max.)
751.22.3.2.4 Beam Type 6 Dimensions/Strand Arrangements
![]() |
|
![]() GROUP I |
Numbers shown on girders relate to strand locations. |
ATTENTION: Location of harped strands shown in top flange are at end of girder and harped strands in bottom flange are at centerline.
If the web thickness is required to be increased, then the top and bottom flanges are to be increased by the same amount. (1" increments, 2" max.)
751.22.3.2.5 Beam Type 7 Dimensions/Strand Arrangements
![]() |
|
![]() GROUP I |
Numbers shown on girders relate to strand locations. |
ATTENTION: Location of harped strands shown in top flange are at end of girder and harped strands in bottom flange are at centerline.
751.22.3.3 NU Standard Girders
751.22.3.3.1 Strand Arrangements
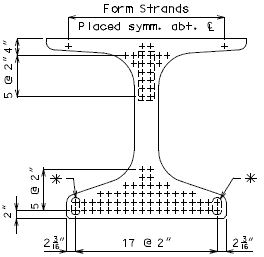
- Note: Strand arrangements shall start at the bottom row and then move up for the most efficient design.
751.22.3.3.2 Top Flange Blockout
![]() |
![]() |
![]() |
![]() | ||||
Choose one of the above four details for the top flange blockout detail and follow the provided detailing guidance.
Blockout shall be dimensioned along the girder to 1 1/2 inches inside the face of the diaphragm and adjusted for any girder tilt.
The left advanced details shown may be used for right advanced bridges. The mirror note may be removed if left advanced.
Revise bent references as required and specify the bent number if blockout varies by bent.
The skew angle value need not be shown for tangent bridges. Consult SPM or Liaison on replacing "skew angle" with actual value for curved bridges.
Revised titles for non-integral end bents (exterior girder at end bent will be same detail as at intermediate bent).
Skew | X Eq. Spa. |
X #4-G6 |
Bar Lengths |
---|---|---|---|
>14° to 21° | 3 | 2 | G3 bar = G5 bar = For skews >7° to 14°: G6 bar = For skews >14° to 60°: report length of G6 bars as “Varies” |
>21° to 27° | 4 | 3 | |
>27° to 32° | 5 | 4 | |
>32° to 37° | 6 | 5 | |
>37° to 42° | 7 | 6 | |
>42° to 46° | 8 | 7 | |
>46° to 49° | 9 | 8 | |
>49° to 52° | 10 | 9 | |
>52° to 55° | 11 | 10 | |
>55° to 57° | 12 | 11 | |
>57° to 60° | 13 | 12 |
751.22.3.4 Beam Section Properties Tables - Conventional Concrete Strength
The properties of prestressed I-girders in the following tables are valid for = 4.5 ksi and = 6 ksi. The modular ratio , , is 8 for the initial moment of inertia, , and 7 for the final moment of inertia, .
Note: Moments of inertia, and are computed based on transformed non-composite section and are used in camber calculations.
Definitions used in tables are:
Section Area | = | Gross area of girder, (in.2) |
Section | = | Distance from bottom of girder to center of gravity of non-transformed non-composite section, (in.) |
= | Moment of inertia of non-transformed non-composite section, (in.4) | |
Depth | = | Height of girder, (in.) |
Strand size | = | Strand diameter, (in.) |
e1* | = | Eccentricity between centroid of straight strands (CSS) and center of gravity of non-transformed non-composite section (CGB) as shown in figure below, (in.) |
e2* | = | Eccentricity between centroid of harped strands (CHS) and center of gravity of non-transformed non-composite section (CGB) at midspan as shown in figure below, (in.) |
e3* | = | Eccentricity between centroid of harped strands (CHS) and center of gravity of non-transformed non-composite section (CGB) at the end of girder as shown in figure below, (in.) |
A more accurate value can be used based on transformed non-composite section. The final camber calculation will not be significantly different using values between transformed and non-transformed sections.
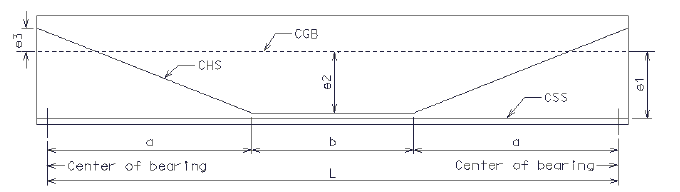
Steps for detailing strand patterns from Prestressed Beam Tables
- For strand locations at mid-span of girder: Look up the "Total Number of Strands" value for the corresponding strand pattern number. The strands will then be located at that number and all numbers below that number. Ex. For 14 total strands, the strands will be placed at all locations numbered ≤14.
- For harped strand locations at end of girder: Look up the "Number of Harped Strands" value for the corresponding strand pattern number. The strands will then be located at that number and all numbers below that number. Ex. For 6 harped strands, the strands will be placed at all locations numbered ≤6.
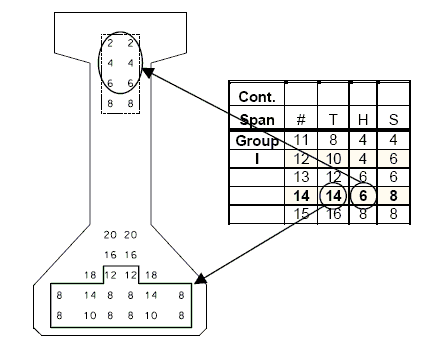
- GROUP I
Section Properties
Beam Type 2 -- 6" Web
Section Area = | 310.9 | in2 |
| ||||||||||||||||
Section = | 14.08 | in | |||||||||||||||||
= | 33,974 | in4 | |||||||||||||||||
Depth= | 32 | in | |||||||||||||||||
Strand Size= | ½ | in | |||||||||||||||||
= | 4.5 | ksi | |||||||||||||||||
= | 6 | ksi |
Iinitial | Ifinal | ||||||||||
# | T | H | S | e1 | e2 | e3 | A1 Bars 2-#5 |
A1 Bars 2-#6 |
A1 Bars 2-#5 |
A1 Bars, 2-#6 | |
Group | 1 | 8 | 4 | 4 | 11.08 | 11.08 | 13.92 | 36,147 | 36,627 | 35,837 | 36,248 |
---|---|---|---|---|---|---|---|---|---|---|---|
I | 2 | 10 | 4 | 6 | 11.41 | 11.08 | 13.92 | 36,453 | 36,938 | 36,100 | 36,515 |
3 | 12 | 6 | 6 | 11.41 | 10.08 | 12.92 | 36,587 | 37,075 | 36,215 | 36,632 | |
4 | 14 | 6 | 8 | 11.08 | 10.08 | 12.92 | 36,794 | 37,286 | 36,394 | 36,814 | |
5 | 16 | 8 | 8 | 11.08 | 9.08 | 11.92 | 36,866 | 37,360 | 36,456 | 36,878 | |
6 | 18 | 8 | 10 | 10.48 | 9.08 | 11.92 | 36,994 | 37,491 | 36,568 | 36,992 | |
Group | 7 | 8 | 2 | 6 | 11.41 | 10.08 | 14.92 | 36,147 | 36,627 | 35,837 | 36,248 |
II | 8 | 10 | 2 | 8 | 11.58 | 10.08 | 14.92 | 36,453 | 36,938 | 36,100 | 36,515 |
9 | 12 | 4 | 8 | 11.08 | 11.08 | 13.92 | 36,663 | 37,151 | 36,280 | 36,698 | |
10 | 14 | 4 | 10 | 11.28 | 9.08 | 13.92 | 36,794 | 37,286 | 36,394 | 36,814 | |
11 | 16 | 6 | 10 | 11.28 | 8.08 | 12.92 | 36,866 | 37,360 | 36,456 | 36,878 | |
12 | 18 | 6 | 12 | 10.75 | 8.08 | 12.92 | 36,994 | 37,491 | 36,568 | 36,992 | |
13 | 20 | 6 | 14 | 10.65 | 6.08 | 12.92 | 37,024 | 37,522 | 36,594 | 37,019 |
Section Properties
Beam Type 2 -- 7" Web
Section Area = | 342.9 | in2 |
| ||||||||||||||||
Section = | 14.26 | in | |||||||||||||||||
= | 36,812 | in4 | |||||||||||||||||
Depth= | 32 | in | |||||||||||||||||
Strand Size= | ½ | in | |||||||||||||||||
= | 4.5 | ksi | |||||||||||||||||
= | 6 | ksi |
Iinitial | Ifinal | ||||||||||
# | T | H | S | e1 | e2 | e3 | A1 Bars 2-#5 |
A1 Bars 2-#6 |
A1 Bars 2-#5 |
A1 Bars 2-#6 | |
Group | 1 | 8 | 4 | 4 | 11.26 | 11.26 | 13.74 | 38,994 | 39,464 | 38,683 | 39,085 |
---|---|---|---|---|---|---|---|---|---|---|---|
I | 2 | 10 | 4 | 6 | 11.59 | 11.26 | 13.74 | 39,310 | 39,784 | 38,954 | 39,360 |
3 | 12 | 6 | 6 | 11.59 | 10.26 | 12.74 | 39,450 | 39,927 | 39,075 | 39,482 | |
4 | 14 | 6 | 8 | 11.26 | 10.26 | 12.74 | 39,666 | 40,146 | 39,261 | 39,671 | |
5 | 16 | 8 | 8 | 11.26 | 9.26 | 11.74 | 39,742 | 40,225 | 39,327 | 39,739 | |
6 | 18 | 8 | 10 | 10.66 | 9.26 | 11.74 | 39,877 | 40,363 | 39,444 | 39,858 | |
Group | 7 | 8 | 2 | 6 | 11.59 | 10.26 | 14.74 | 38,994 | 39,464 | 38,683 | 39,085 |
II | 8 | 10 | 2 | 8 | 11.76 | 10.26 | 14.74 | 39,310 | 39,784 | 38,954 | 39,360 |
9 | 12 | 4 | 8 | 11.26 | 11.26 | 13.74 | 39,528 | 40,005 | 39,142 | 39,550 | |
10 | 14 | 4 | 10 | 11.46 | 9.26 | 13.74 | 39,666 | 40,146 | 39,261 | 39,671 | |
11 | 16 | 6 | 10 | 11.46 | 8.26 | 12.74 | 39,742 | 40,225 | 39,327 | 39,739 | |
12 | 18 | 6 | 12 | 10.93 | 8.26 | 12.74 | 39,877 | 40,363 | 39,444 | 39,858 | |
13 | 20 | 6 | 14 | 10.83 | 6.26 | 12.74 | 39,910 | 39,473 | 39,473 | 39,888 |
Section Properties
Beam Type 2 -- 8" Web
Section Area = | 374.9 | in2 |
| ||||||||||||||||
Section = | 14.41 | in | |||||||||||||||||
= | 39,632 | in4 | |||||||||||||||||
Depth= | 32 | in | |||||||||||||||||
Strand Size= | ½ | in | |||||||||||||||||
= | 4.5 | ksi | |||||||||||||||||
= | 6 | ksi |
Iinitial | Ifinal | ||||||||||
# | T | H | S | e1 | e2 | e3 | A1 Bars 2-#5 |
A1 Bars 2-#6 |
A1 Bars 2-#5 |
A1 Bars 2-#6 | |
Group | 1 | 8 | 4 | 4 | 11.41 | 11.41 | 13.59 | 41,823 | 42,283 | 41,510 | 41,905 |
---|---|---|---|---|---|---|---|---|---|---|---|
I | 2 | 10 | 4 | 6 | 11.74 | 11.41 | 13.59 | 42,147 | 42,611 | 41,789 | 42,186 |
3 | 12 | 6 | 6 | 11.74 | 10.41 | 12.59 | 42,292 | 42,760 | 41,914 | 42,313 | |
4 | 14 | 6 | 8 | 11.41 | 10.41 | 12.59 | 42,515 | 42,985 | 42,106 | 42,508 | |
5 | 16 | 8 | 8 | 11.41 | 9.41 | 11.59 | 42,596 | 43,068 | 42,176 | 42,579 | |
6 | 18 | 8 | 10 | 10.81 | 9.41 | 11.59 | 42,737 | 43,212 | 42,298 | 42,703 | |
Group | 7 | 8 | 2 | 6 | 11.74 | 10.41 | 14.59 | 41,823 | 42,283 | 41,510 | 41,905 |
II | 8 | 10 | 2 | 8 | 11.91 | 10.41 | 14.59 | 42,147 | 42,611 | 41,789 | 42,186 |
9 | 12 | 4 | 8 | 11.41 | 11.41 | 13.59 | 42,371 | 42,839 | 41,982 | 42,382 | |
10 | 14 | 4 | 10 | 11.61 | 9.41 | 13.59 | 42,515 | 42,985 | 42,106 | 42,508 | |
11 | 16 | 6 | 10 | 11.61 | 8.41 | 12.59 | 42,596 | 43,068 | 42,176 | 42,579 | |
12 | 18 | 6 | 12 | 11.08 | 8.41 | 12.59 | 42,737 | 43,212 | 42,298 | 42,703 | |
13 | 20 | 6 | 14 | 10.98 | 6.41 | 12.59 | 42,772 | 43,249 | 42,329 | 42,736 |
Section Properties
Beam Type 3 -- 6" Web
Section Area = | 381.9 | in2 |
| ||||||||||||||||
Section = | 17.08 | in | |||||||||||||||||
= | 61,841 | in4 | |||||||||||||||||
Depth= | 39 | in | |||||||||||||||||
Strand Size= | ½ | in | |||||||||||||||||
= | 4.5 | ksi | |||||||||||||||||
= | 6 | ksi |
Cont. | Iinitial | Ifinal | |||||||||
---|---|---|---|---|---|---|---|---|---|---|---|
Span | # | T | H | S | e1 | e2 | e3 | A1 Bars 2-#5 |
A1 Bars 2-#6 |
A1 Bars 2-#5 |
A1 Bars 2-#6 |
Group | 1 | 8 | 4 | 4 | 13.08 | 14.08 | 17.92 | 65,179 | 65,930 | 64,702 | 65,346 |
I | 2 | 10 | 4 | 6 | 13.75 | 14.08 | 17.92 | 65,659 | 66,415 | 65,114 | 65,762 |
3 | 12 | 4 | 8 | 13.58 | 14.08 | 17.92 | 66,014 | 66,776 | 65,421 | 66,072 | |
4 | 14 | 6 | 8 | 13.58 | 13.08 | 16.92 | 66,265 | 67,032 | 65,637 | 66,292 | |
5 | 16 | 6 | 10 | 13.48 | 13.08 | 16.92 | 66,614 | 67,386 | 65,938 | 66,597 | |
6 | 18 | 8 | 10 | 13.48 | 12.08 | 15.92 | 66,776 | 67,552 | 66,079 | 66,740 | |
7 | 20 | 8 | 12 | 13.08 | 12.08 | 15.92 | 67,020 | 67,799 | 66,290 | 66,954 | |
8 | 22 | 8 | 14 | 12.51 | 12.08 | 15.92 | 67,178 | 67,961 | 66,427 | 67,095 | |
9 | 24 | 10 | 14 | 12.51 | 11.08 | 14.92 | 67,270 | 68,056 | 66,508 | 67,177 | |
Group | 10 | 8 | 2 | 6 | 13.75 | 13.08 | 18.92 | 65,179 | 65,930 | 64,702 | 65,346 |
II | 11 | 10 | 2 | 8 | 14.08 | 13.08 | 18.92 | 65,659 | 66,415 | 65,114 | 65,762 |
12 | 12 | 2 | 10 | 13.88 | 13.08 | 18.92 | 66,014 | 66,776 | 65,421 | 66,072 | |
13 | 14 | 4 | 10 | 13.48 | 14.08 | 17.92 | 66,366 | 67,134 | 65,724 | 66,379 | |
14 | 16 | 4 | 12 | 13.75 | 12.08 | 17.92 | 66,614 | 67,386 | 65,938 | 66,597 | |
15 | 18 | 6 | 12 | 13.75 | 11.08 | 16.92 | 66,776 | 67,552 | 66,079 | 66,740 | |
16 | 20 | 6 | 14 | 13.37 | 11.08 | 16.92 | 67,020 | 67,799 | 66,290 | 66,954 | |
17 | 22 | 6 | 16 | 12.83 | 11.08 | 16.92 | 67,178 | 67,961 | 66,427 | 67,095 | |
18 | 24 | 8 | 16 | 12.83 | 10.08 | 15.92 | 67,270 | 68,056 | 66,508 | 67,177 |
Section Properties
Beam Type 3 -- 7" Web
Section Area = | 420.9 | in2 |
| ||||||||||||||||
Section = | 17.31 | in | |||||||||||||||||
= | 66,991 | in4 | |||||||||||||||||
Depth= | 39 | in | |||||||||||||||||
Strand Size= | ½ | in | |||||||||||||||||
= | 4.5 | ksi | |||||||||||||||||
= | 6 | ksi |
Cont. | Iinitial | Ifinal | |||||||||
---|---|---|---|---|---|---|---|---|---|---|---|
Span | # | T | H | S | e1 | e2 | e3 | A1 Bars 2-#5 |
A1 Bars 2-#6 |
A1 Bars 2-#5 |
A1 Bars 2-#6 |
Group | 1 | 8 | 4 | 4 | 13.31 | 14.31 | 17.69 | 70,343 | 71,077 | 69,865 | 70,493 |
I | 2 | 10 | 4 | 6 | 13.98 | 14.31 | 17.69 | 70,838 | 71,577 | 70,289 | 70,922 |
3 | 12 | 4 | 8 | 13.81 | 14.31 | 17.69 | 71,207 | 71,951 | 70,607 | 71,243 | |
4 | 14 | 6 | 8 | 13.81 | 13.31 | 16.69 | 71,469 | 72,218 | 70,833 | 71,473 | |
5 | 16 | 6 | 10 | 13.71 | 13.31 | 16.69 | 71,832 | 72,585 | 71,146 | 71,789 | |
6 | 18 | 8 | 10 | 13.71 | 12.31 | 15.69 | 72,004 | 72,760 | 71,295 | 71,940 | |
7 | 20 | 8 | 12 | 13.31 | 12.31 | 15.69 | 72,259 | 73,019 | 71,516 | 72,164 | |
8 | 22 | 8 | 14 | 12.74 | 12.31 | 15.69 | 72,427 | 73,190 | 71,662 | 72,312 | |
9 | 24 | 10 | 14 | 12.74 | 11.31 | 14.69 | 72,526 | 73,292 | 71,749 | 72,401 | |
Group | 10 | 8 | 2 | 6 | 13.98 | 13.31 | 18.69 | 70,343 | 71,077 | 69,865 | 70,493 |
II | 11 | 10 | 2 | 8 | 14.31 | 13.31 | 18.69 | 70,838 | 71,577 | 70,289 | 70,922 |
12 | 12 | 2 | 10 | 14.11 | 13.31 | 18.69 | 71,207 | 71,951 | 70,607 | 71,243 | |
13 | 14 | 4 | 10 | 13.71 | 14.31 | 17.69 | 71,572 | 72,322 | 70,922 | 71,562 | |
14 | 16 | 4 | 12 | 13.98 | 12.31 | 17.69 | 71,832 | 72,585 | 71,146 | 71,789 | |
15 | 18 | 6 | 12 | 13.98 | 11.31 | 16.69 | 72,004 | 72,760 | 71,295 | 71,940 | |
16 | 20 | 6 | 14 | 13.60 | 11.31 | 16.69 | 72,259 | 73,019 | 71,516 | 72,164 | |
17 | 22 | 6 | 16 | 13.06 | 11.31 | 16.69 | 72,427 | 73,190 | 71,662 | 72,312 | |
18 | 24 | 8 | 16 | 13.06 | 10.31 | 15.69 | 72,526 | 73,292 | 71,749 | 72,401 |
Section Properties
Beam Type 3 -- 8" Web
Section Area = | 459.9 | in2 |
| ||||||||||||||||
Section = | 17.49 | in | |||||||||||||||||
= | 72,106 | in4 | |||||||||||||||||
Depth= | 39 | in | |||||||||||||||||
Strand Size= | ½ | in | |||||||||||||||||
= | 4.5 | ksi | |||||||||||||||||
= | 6 | ksi |
Cont. | Iinitial | Ifinal | |||||||||
---|---|---|---|---|---|---|---|---|---|---|---|
Span | # | T | H | S | e1 | e2 | e3 | A1 Bars 2-#5 |
A1 Bars 2-#6 |
A1 Bars 2-#5 |
A1 Bars 2-#6 |
Group | 1 | 8 | 4 | 4 | 13.49 | 14.49 | 17.51 | 75,470 | 76,191 | 74,990 | 75,607 |
I | 2 | 10 | 4 | 6 | 14.16 | 14.49 | 17.51 | 75,977 | 76,703 | 75,425 | 76,046 |
3 | 12 | 4 | 8 | 13.99 | 14.49 | 17.51 | 76,357 | 77,087 | 75,752 | 76,376 | |
4 | 14 | 6 | 8 | 13.99 | 13.49 | 16.51 | 76,628 | 77,363 | 75,986 | 76,613 | |
5 | 16 | 6 | 10 | 13.89 | 13.49 | 16.51 | 77,002 | 77,740 | 76,308 | 76,939 | |
6 | 18 | 8 | 10 | 13.89 | 12.49 | 15.51 | 77,182 | 77,923 | 76,464 | 77,096 | |
7 | 20 | 8 | 12 | 13.49 | 12.49 | 15.51 | 77,446 | 78,191 | 76,692 | 77,328 | |
8 | 22 | 8 | 14 | 12.92 | 12.49 | 15.51 | 77,622 | 78,370 | 76,845 | 77,483 | |
9 | 24 | 10 | 14 | 12.92 | 11.49 | 14.51 | 77,728 | 78,479 | 76,938 | 77,577 | |
Group | 10 | 8 | 2 | 6 | 14.16 | 13.49 | 18.51 | 75,470 | 76,191 | 74,990 | 75,607 |
II | 11 | 10 | 2 | 8 | 14.49 | 13.49 | 18.51 | 75,977 | 76,703 | 75,425 | 76,046 |
12 | 12 | 2 | 10 | 14.29 | 13.49 | 18.51 | 76,357 | 77,087 | 75,752 | 76,376 | |
13 | 14 | 4 | 10 | 13.89 | 14.49 | 17.51 | 76,733 | 77,468 | 76,076 | 76,704 | |
14 | 16 | 4 | 12 | 14.16 | 12.49 | 17.51 | 77,002 | 77,740 | 76,308 | 76,939 | |
15 | 18 | 6 | 12 | 14.16 | 11.49 | 16.51 | 77,182 | 77,923 | 76,464 | 77,096 | |
16 | 20 | 6 | 14 | 13.78 | 11.49 | 16.51 | 77,446 | 78,191 | 76,692 | 77,328 | |
17 | 22 | 6 | 16 | 13.24 | 11.49 | 16.51 | 77,622 | 78,370 | 76,845 | 77,483 | |
18 | 24 | 8 | 16 | 13.24 | 10.49 | 15.51 | 77,728 | 78,479 | 76,938 | 77,577 |
Section Properties
Beam Type 4 -- 6" Web
Section Area = | 428.9 | in2 |
| ||||||||||||||||
Section = | 19.54 | in | |||||||||||||||||
= | 92,450 | in4 | |||||||||||||||||
Depth= | 45 | in | |||||||||||||||||
Strand Size= | ½ | in | |||||||||||||||||
= | 4.5 | ksi | |||||||||||||||||
= | 6 | ksi |
Cont. | Iinitial | Ifinal | |||||||||
---|---|---|---|---|---|---|---|---|---|---|---|
Span | # | T | H | S | e1 | e2 | e3 | A1 Bars 2-#5 |
A1 Bars 2-#6 |
A1 Bars 2-#5 |
A1 Bars 2-#6 |
Group | 1 | 8 | 4 | 4 | 15.54 | 16.54 | 21.46 | 97,077 | 98,118 | 96,416 | 97,308 |
I | 2 | 10 | 4 | 6 | 16.21 | 16.54 | 21.46 | 97,727 | 98,775 | 96,974 | 97,872 |
3 | 12 | 4 | 8 | 16.04 | 16.54 | 21.46 | 98,231 | 99,286 | 97,408 | 98,310 | |
4 | 14 | 6 | 8 | 16.04 | 15.54 | 20.46 | 98,608 | 99,669 | 97,733 | 98,640 | |
5 | 16 | 6 | 10 | 15.94 | 15.54 | 20.46 | 99,103 | 100,170 | 98,160 | 99,071 | |
6 | 18 | 8 | 10 | 15.94 | 14.54 | 19.46 | 99,368 | 100,441 | 98,390 | 99,305 | |
7 | 20 | 8 | 12 | 15.54 | 14.54 | 19.46 | 99,735 | 100,813 | 98,707 | 99,626 | |
8 | 22 | 8 | 14 | 14.97 | 14.54 | 19.46 | 99,995 | 101,078 | 98,933 | 99,856 | |
9 | 24 | 8 | 16 | 15.29 | 12.54 | 19.46 | 100,168 | 101,254 | 99,083 | 100,009 | |
10 | 26 | 10 | 16 | 15.29 | 11.54 | 18.46 | 100,271 | 101,360 | 99,174 | 100,102 | |
11 | 28 | 10 | 18 | 15.32 | 9.54 | 18.46 | 100,323 | 101,414 | 99,220 | 100,149 | |
Group | 12 | 8 | 2 | 6 | 16.21 | 15.54 | 22.46 | 97,077 | 98,118 | 96,416 | 97,308 |
II | 13 | 10 | 2 | 8 | 16.54 | 15.54 | 22.46 | 97,727 | 98,775 | 96,974 | 97,872 |
14 | 12 | 4 | 8 | 16.04 | 16.54 | 21.46 | 98,231 | 99,286 | 97,408 | 98,310 | |
15 | 14 | 4 | 10 | 15.94 | 16.54 | 21.46 | 98,730 | 99,792 | 97,838 | 98,745 | |
16 | 16 | 4 | 12 | 16.21 | 14.54 | 21.46 | 99,103 | 100,170 | 98,160 | 99,071 | |
17 | 16 | 6 | 10 | 15.94 | 15.54 | 20.46 | 99,103 | 100,170 | 98,160 | 99,071 | |
18 | 18 | 6 | 12 | 16.21 | 13.54 | 20.46 | 99,368 | 100,441 | 98,390 | 99,305 | |
19 | 20 | 6 | 14 | 15.83 | 13.54 | 20.46 | 99,735 | 100,813 | 98,707 | 99,626 | |
20 | 22 | 6 | 16 | 15.29 | 13.54 | 20.46 | 99,995 | 101,078 | 98,933 | 99,856 | |
21 | 24 | 6 | 18 | 15.32 | 11.54 | 20.46 | 100,168 | 101,254 | 99,083 | 100,009 | |
22 | 26 | 6 | 20 | 15.14 | 9.54 | 20.46 | 100,271 | 101,360 | 99,174 | 100,102 | |
23 | 26 | 8 | 18 | 15.32 | 10.54 | 19.46 | 100,271 | 101,360 | 99,174 | 100,102 | |
24 | 28 | 6 | 22 | 14.81 | 7.54 | 20.46 | 100,323 | 101,414 | 99,220 | 100,149 | |
25 | 28 | 8 | 20 | 15.14 | 8.54 | 19.46 | 100,323 | 101,414 | 99,220 | 100,149 | |
26 | 30 | 8 | 22 | 14.81 | 6.54 | 19.46 | 100,341 | 101,433 | 99,236 | 100,166 | |
27 | 32 | 8 | 24 | 14.37 | 4.54 | 19.46 | 100,342 | 101,435 | 99,238 | 100,168 |
Section Properties
Beam Type 4 -- 7" Web
Section Area = | 473.9 | in2 |
| ||||||||||||||||
Section = | 19.82 | in | |||||||||||||||||
= | 100,400 | in4 | |||||||||||||||||
Depth= | 45 | in | |||||||||||||||||
Strand Size= | ½ | in | |||||||||||||||||
= | 4.5 | ksi | |||||||||||||||||
= | 6 | ksi |
Cont. | Iinitial | Ifinal | |||||||||
---|---|---|---|---|---|---|---|---|---|---|---|
Span | # | T | H | S | e1 | e2 | e3 | A1 Bars 2-#5 |
A1 Bars 2-#6 |
A1 Bars 2-#5 |
A1 Bars 2-#6 |
Group | 1 | 8 | 4 | 4 | 15.82 | 16.82 | 21.18 | 105,048 | 106,065 | 104,384 | 105,256 |
I | 2 | 10 | 4 | 6 | 16.49 | 16.82 | 21.18 | 105,719 | 106,743 | 104,960 | 105,837 |
3 | 12 | 4 | 8 | 16.32 | 16.82 | 21.18 | 106,242 | 107,272 | 105,410 | 106,291 | |
4 | 14 | 6 | 8 | 16.32 | 15.82 | 20.18 | 106,636 | 107,671 | 105,750 | 106,635 | |
5 | 16 | 6 | 10 | 16.22 | 15.82 | 20.18 | 107,151 | 108,192 | 106,193 | 107,083 | |
6 | 18 | 8 | 10 | 16.22 | 14.82 | 19.18 | 107,431 | 108,476 | 106,436 | 107,328 | |
7 | 20 | 8 | 12 | 15.82 | 14.82 | 19.18 | 107,815 | 108,866 | 106,768 | 107,664 | |
8 | 22 | 8 | 14 | 15.25 | 14.82 | 19.18 | 108,090 | 109,145 | 107,007 | 107,906 | |
9 | 24 | 8 | 16 | 15.57 | 12.82 | 19.18 | 108,275 | 109,334 | 107,168 | 108,070 | |
10 | 26 | 10 | 16 | 15.57 | 11.82 | 18.18 | 108,388 | 109,449 | 107,266 | 108,171 | |
11 | 28 | 10 | 18 | 15.60 | 9.82 | 18.18 | 108,446 | 109,510 | 107,318 | 108,224 | |
Group | 12 | 8 | 2 | 6 | 16.49 | 15.82 | 22.18 | 105,048 | 106,065 | 104,384 | 105,256 |
II | 13 | 10 | 2 | 8 | 16.82 | 15.82 | 22.18 | 105,719 | 106,743 | 104,960 | 105,837 |
14 | 12 | 4 | 8 | 16.32 | 16.82 | 21.18 | 106,242 | 107,272 | 105,410 | 106,291 | |
15 | 14 | 4 | 10 | 16.22 | 16.82 | 21.18 | 106,760 | 107,796 | 105,857 | 106,742 | |
16 | 16 | 4 | 12 | 16.49 | 14.82 | 21.18 | 107,151 | 108,192 | 106,193 | 107,083 | |
17 | 16 | 6 | 10 | 16.22 | 15.82 | 20.18 | 107,151 | 108,192 | 106,193 | 107,083 | |
18 | 18 | 6 | 12 | 16.49 | 13.82 | 20.18 | 107,431 | 108,476 | 106,436 | 107,328 | |
19 | 20 | 6 | 14 | 16.11 | 13.82 | 20.18 | 107,815 | 108,866 | 106,768 | 107,664 | |
20 | 22 | 6 | 16 | 15.57 | 13.82 | 20.18 | 108,090 | 109,145 | 107,007 | 107,906 | |
21 | 24 | 6 | 18 | 15.60 | 11.82 | 20.18 | 108,275 | 109,334 | 107,168 | 108,070 | |
22 | 26 | 6 | 20 | 15.42 | 9.82 | 20.18 | 108,388 | 109,449 | 107,266 | 108,171 | |
23 | 26 | 8 | 18 | 15.60 | 10.82 | 19.18 | 108,388 | 109,449 | 107,266 | 108,171 | |
24 | 28 | 6 | 22 | 15.09 | 7.82 | 20.18 | 108,446 | 109,510 | 107,318 | 108,224 | |
25 | 28 | 8 | 20 | 15.42 | 8.82 | 19.18 | 108,446 | 109,510 | 107,318 | 108,224 | |
26 | 30 | 8 | 22 | 15.09 | 6.82 | 19.18 | 108,469 | 109,533 | 107,338 | 108,245 | |
27 | 32 | 8 | 24 | 14.65 | 4.82 | 19.18 | 108,472 | 109,537 | 107,341 | 108,248 |
Section Properties
Beam Type 4 -- 8" Web
Section Area = | 518.9 | in2 |
| ||||||||||||||||
Section = | 20.06 | in | |||||||||||||||||
= | 108,288 | in4 | |||||||||||||||||
Depth= | 45 | in | |||||||||||||||||
Strand Size= | ½ | in | |||||||||||||||||
= | 4.5 | ksi | |||||||||||||||||
= | 6 | ksi |
Cont. | Iinitial | Ifinal | |||||||||
---|---|---|---|---|---|---|---|---|---|---|---|
Span | # | T | H | S | e1 | e2 | e3 | A1 Bars 2-#5 |
A1 Bars 2-#6 |
A1 Bars 2-#5 |
A1 Bars 2-#6 |
Group | 1 | 8 | 4 | 4 | 16.06 | 17.06 | 20.94 | 112,955 | 113,952 | 112,289 | 113,143 |
I | 2 | 10 | 4 | 6 | 16.73 | 17.06 | 20.94 | 113,645 | 114,648 | 112,881 | 113,739 |
3 | 12 | 4 | 8 | 16.56 | 17.06 | 20.94 | 114,185 | 115,193 | 113,345 | 114,208 | |
4 | 14 | 6 | 8 | 16.56 | 16.06 | 19.94 | 114,594 | 115,607 | 113,698 | 114,563 | |
5 | 16 | 6 | 10 | 16.46 | 16.06 | 19.94 | 115,126 | 116,144 | 114,156 | 115,026 | |
6 | 18 | 8 | 10 | 16.46 | 15.06 | 18.94 | 115,419 | 116,442 | 114,409 | 115,282 | |
7 | 20 | 8 | 12 | 16.06 | 15.06 | 18.94 | 115,818 | 116,846 | 114,755 | 115,631 | |
8 | 22 | 8 | 14 | 15.49 | 15.06 | 18.94 | 116,107 | 117,138 | 115,004 | 115,884 | |
9 | 24 | 8 | 16 | 15.81 | 13.06 | 18.94 | 116,303 | 117,337 | 115,175 | 116,057 | |
10 | 26 | 10 | 16 | 15.81 | 12.06 | 17.94 | 116,424 | 117,461 | 115,281 | 116,165 | |
11 | 28 | 10 | 18 | 15.84 | 10.06 | 17.94 | 116,489 | 117,528 | 115,338 | 116,223 | |
Group | 12 | 8 | 2 | 6 | 16.73 | 16.06 | 21.94 | 112,955 | 113,952 | 112,289 | 113,143 |
II | 13 | 10 | 2 | 8 | 17.06 | 16.06 | 21.94 | 113,645 | 114,648 | 112,881 | 113,739 |
14 | 12 | 4 | 8 | 16.56 | 17.06 | 20.94 | 114,185 | 115,193 | 113,345 | 114,208 | |
15 | 14 | 4 | 10 | 16.46 | 17.06 | 20.94 | 114,720 | 115,734 | 113,806 | 114,673 | |
16 | 16 | 4 | 12 | 16.73 | 15.06 | 20.94 | 115,126 | 116,144 | 114,156 | 115,026 | |
17 | 16 | 6 | 10 | 16.46 | 16.06 | 19.94 | 115,126 | 116,144 | 114,156 | 115,026 | |
18 | 18 | 6 | 12 | 16.73 | 14.06 | 19.94 | 115,419 | 116,442 | 114,409 | 115,282 | |
19 | 20 | 6 | 14 | 16.35 | 14.06 | 19.94 | 115,818 | 116,846 | 114,755 | 115,631 | |
20 | 22 | 6 | 16 | 15.81 | 14.06 | 19.94 | 116,107 | 117,138 | 115,004 | 115,884 | |
21 | 24 | 6 | 18 | 15.84 | 12.06 | 19.94 | 116,303 | 117,337 | 115,175 | 116,057 | |
22 | 26 | 6 | 20 | 15.66 | 10.06 | 19.94 | 116,424 | 117,461 | 115,281 | 116,165 | |
23 | 26 | 8 | 18 | 15.84 | 11.06 | 18.94 | 116,424 | 117,461 | 115,281 | 116,165 | |
24 | 28 | 6 | 22 | 15.33 | 8.06 | 19.94 | 116,489 | 117,528 | 115,338 | 116,223 | |
25 | 28 | 8 | 20 | 15.66 | 9.06 | 18.94 | 116,489 | 117,528 | 115,338 | 116,223 | |
26 | 30 | 8 | 22 | 15.33 | 7.06 | 18.94 | 116,515 | 117,555 | 115,361 | 116,247 | |
27 | 32 | 8 | 24 | 14.89 | 5.06 | 18.94 | 116,520 | 117,560 | 115,366 | 116,252 |
Section Properties
Beam Type 6 -- 6.5" Web
Section Area = | 643.6 | in2 |
| ||||||||||||||||
Section = | 25.92 | in | |||||||||||||||||
= | 235,735 | in4 | |||||||||||||||||
Depth= | 54 | in | |||||||||||||||||
Strand Size= | ½ | in | |||||||||||||||||
= | 4.5 | ksi | |||||||||||||||||
= | 6 | ksi |
Iinitial | Ifinal | ||||||||
# | T | H | S | e1 | e2 | e3 | A1 Bars 2-#6 |
A1 Bars 2-#6 | |
Group | 1 | 14 | 4 | 10 | 23.52 | 22.92 | 23.08 | 248,115 | 246,353 |
---|---|---|---|---|---|---|---|---|---|
I | 2 | 16 | 4 | 12 | 23.25 | 22.92 | 23.08 | 249,115 | 247,213 |
3 | 18 | 6 | 12 | 23.25 | 21.92 | 22.08 | 249,933 | 247,918 | |
4 | 20 | 6 | 14 | 23.06 | 21.92 | 22.08 | 250,920 | 248,769 | |
5 | 22 | 6 | 16 | 22.92 | 21.92 | 22.08 | 251,901 | 249,616 | |
6 | 24 | 8 | 16 | 22.92 | 20.92 | 21.08 | 252,545 | 250,173 | |
7 | 26 | 8 | 18 | 22.59 | 20.92 | 21.08 | 253,342 | 250,862 | |
8 | 28 | 8 | 20 | 22.32 | 20.92 | 21.08 | 254,133 | 251,547 | |
9 | 30 | 10 | 20 | 22.32 | 19.92 | 20.08 | 254,626 | 251,975 | |
10 | 32 | 10 | 22 | 22.10 | 19.92 | 20.08 | 255,408 | 252,653 | |
11 | 34 | 10 | 24 | 21.75 | 19.92 | 20.08 | 256,032 | 253,195 | |
12 | 36 | 10 | 26 | 21.46 | 19.92 | 20.08 | 256,651 | 253,734 | |
13 | 38 | 12 | 26 | 21.46 | 18.92 | 19.08 | 257,011 | 254,048 |
Section Properties
Beam Type 6 -- 7.5" Web
Section Area = | 697.6 | in2 |
| ||||||||||||||||
Section = | 26.00 | in | |||||||||||||||||
= | 248,915 | in4 | |||||||||||||||||
Depth= | 54 | in | |||||||||||||||||
Strand Size= | ½ | in | |||||||||||||||||
= | 4.5 | ksi | |||||||||||||||||
= | 6 | ksi |
Iinitial | Ifinal | ||||||||
# | T | H | S | e1 | e2 | e3 | A1 Bars 2-#6 |
A1 Bars 2-#6 | |
Group | 1 | 14 | 4 | 10 | 23.60 | 23.00 | 23.00 | 262,852 | 260,864 |
---|---|---|---|---|---|---|---|---|---|
I | 2 | 16 | 4 | 12 | 23.33 | 23.00 | 23.00 | 263,868 | 261,737 |
3 | 18 | 6 | 12 | 23.33 | 22.00 | 22.00 | 264,701 | 262,454 | |
4 | 20 | 6 | 14 | 23.14 | 22.00 | 22.00 | 265,707 | 263,319 | |
5 | 22 | 6 | 16 | 23.00 | 22.00 | 22.00 | 266,706 | 264,180 | |
6 | 24 | 8 | 16 | 23.00 | 21.00 | 21.00 | 267,365 | 264,749 | |
7 | 26 | 8 | 18 | 22.67 | 21.00 | 21.00 | 268,178 | 265,452 | |
8 | 28 | 8 | 20 | 22.40 | 21.00 | 21.00 | 268,987 | 266,150 | |
9 | 30 | 10 | 20 | 22.40 | 20.00 | 20.00 | 269,493 | 266,589 | |
10 | 32 | 10 | 22 | 22.18 | 20.00 | 20.00 | 270,294 | 267,282 | |
11 | 34 | 10 | 24 | 21.83 | 20.00 | 20.00 | 270,933 | 267,836 | |
12 | 36 | 10 | 26 | 21.54 | 20.00 | 20.00 | 271,569 | 268,387 | |
13 | 38 | 12 | 26 | 21.54 | 19.00 | 19.00 | 271,941 | 268,712 |
Section Properties
Beam Type 6 -- 8.5" Web
Section Area = | 751.6 | in2 |
| ||||||||||||||||
Section = | 26.07 | in | |||||||||||||||||
= | 262,087 | in4 | |||||||||||||||||
Depth= | 54 | in | |||||||||||||||||
Strand Size= | ½ | in | |||||||||||||||||
= | 4.5 | ksi | |||||||||||||||||
= | 6 | ksi |
Iinitial | Ifinal | ||||||||
# | T | H | S | e1 | e2 | e3 | A1 Bars 2-#6 |
A1 Bars 2-#6 | |
Group | 1 | 14 | 4 | 10 | 23.67 | 23.07 | 22.93 | 276,043 | 274,052 |
---|---|---|---|---|---|---|---|---|---|
I | 2 | 16 | 4 | 12 | 23.40 | 23.07 | 22.93 | 277,068 | 274,932 |
3 | 18 | 6 | 12 | 23.40 | 22.07 | 21.93 | 277,908 | 275,656 | |
4 | 20 | 6 | 14 | 23.21 | 22.07 | 21.93 | 278,922 | 276,528 | |
5 | 22 | 6 | 16 | 23.07 | 22.07 | 21.93 | 279,930 | 277,396 | |
6 | 24 | 8 | 16 | 23.07 | 21.07 | 20.93 | 280,596 | 277,971 | |
7 | 26 | 8 | 18 | 22.74 | 21.07 | 20.93 | 281,418 | 278,680 | |
8 | 28 | 8 | 20 | 22.47 | 21.07 | 20.93 | 282,236 | 279,386 | |
9 | 30 | 10 | 20 | 22.47 | 20.07 | 19.93 | 282,750 | 279,831 | |
10 | 32 | 10 | 22 | 22.25 | 20.07 | 19.93 | 283,559 | 280,531 | |
11 | 34 | 10 | 24 | 21.90 | 20.07 | 19.93 | 284,207 | 281,093 | |
12 | 36 | 10 | 26 | 21.61 | 20.07 | 19.93 | 284,851 | 281,651 | |
13 | 38 | 12 | 26 | 21.61 | 19.07 | 18.93 | 285,230 | 281,981 |
Section Properties
Beam Type 7 -- 6" Web
Bulb-Tee Girder
Section Area = | 787.4 | in2 |
| ||||||||||||||||
Section = | 37.58 | in | |||||||||||||||||
= | 571,047 | in4 | |||||||||||||||||
Depth= | 72.5 | in | |||||||||||||||||
Strand Size= | ½ | in | |||||||||||||||||
= | 4.5 | ksi | |||||||||||||||||
= | 6 | ksi |
Cont. | Iinitial | Ifinal | |||||||
---|---|---|---|---|---|---|---|---|---|
Span | # | T | H | S | e1 | e2 | e3 | A1 Bars 4-#6 |
A1 Bars 4-#6 |
Group | 1 | 14 | 4 | 10 | 35.58 | 34.58 | 29.92 | 603,636 | 598,983 |
I | 2 | 16 | 4 | 12 | 35.25 | 34.58 | 29.92 | 606,025 | 601,033 |
3 | 18 | 6 | 12 | 35.25 | 33.58 | 28.92 | 608,125 | 602,838 | |
4 | 20 | 6 | 14 | 35.01 | 33.58 | 28.92 | 610,490 | 604,871 | |
5 | 22 | 6 | 16 | 34.83 | 33.58 | 28.92 | 612,843 | 606,895 | |
6 | 24 | 8 | 16 | 34.83 | 32.58 | 27.92 | 614,652 | 608,453 | |
7 | 26 | 8 | 18 | 34.69 | 32.58 | 27.92 | 616,981 | 610,459 | |
8 | 28 | 8 | 20 | 34.58 | 32.58 | 27.92 | 619,299 | 612,457 | |
9 | 30 | 10 | 20 | 34.58 | 31.58 | 26.92 | 620,839 | 613,788 | |
10 | 32 | 10 | 22 | 34.31 | 31.58 | 26.92 | 622,864 | 615,536 | |
11 | 34 | 10 | 24 | 34.08 | 31.58 | 26.92 | 624,878 | 617,276 | |
12 | 36 | 10 | 26 | 33.89 | 31.58 | 26.92 | 626,881 | 619,009 | |
13 | 38 | 10 | 28 | 33.58 | 31.58 | 26.92 | 628,622 | 620,517 | |
14 | 40 | 12 | 28 | 33.58 | 30.58 | 25.92 | 629,902 | 621,627 |
751.22.3.5 Beam Section Properties Tables - Higher Concrete Strength
The properties of prestressed I-girders in the following tables are valid for = 5 ksi and = 7 ksi. The modular ratio , , is 7 for the initial moment of inertia, , and 6 for the final moment of inertia, .
Note: Moments of inertia, and are computed based on transformed non-composite section and are used in camber calculations. A1 Bar locations are assumed at 3" from the top of girder.
Definitions used in tables are:
Section Area | = | Gross area of girder, (in.2) |
Section | = | Distance from bottom of girder to center of gravity of non-transformed non-composite section, (in.) |
= | Moment of inertia of non-transformed non-composite section, (in.4) | |
Depth | = | Height of girder, (in.) |
Strand size | = | Strand diameter, (in.) |
e1* | = | Eccentricity between centroid of straight strands (CSS) and center of gravity of non-transformed non-composite section (CGB) as shown in figure below, (in.) |
e2* | = | Eccentricity between centroid of harped strands (CHS) and center of gravity of non-transformed non-composite section (CGB) at midspan as shown in figure below, (in.) |
e3* | = | Eccentricity between centroid of harped strands (CHS) and center of gravity of non-transformed non-composite section (CGB) at the end of girder as shown in figure below, (in.) |
A more accurate value can be used based on transformed non-composite section. The final camber calculation will not be significantly different using values between transformed and non-transformed sections.
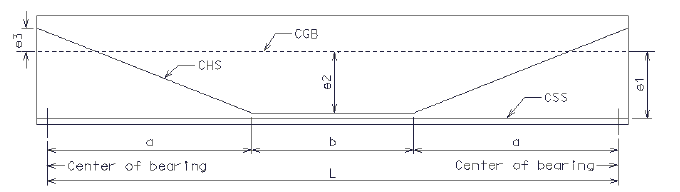
Steps for detailing strand patterns from Prestressed Beam Tables
- For strand locations at mid-span of girder: Look up the "Total Number of Strands" value for the corresponding strand pattern number. The strands will then be located at that number and all numbers below that number. Ex. For 14 total strands, the strands will be placed at all locations numbered ≤14.
- For harped strand locations at end of girder: Look up the "Number of Harped Strands" value for the corresponding strand pattern number. The strands will then be located at that number and all numbers below that number. Ex. For 6 harped strands, the strands will be placed at all locations numbered ≤6.
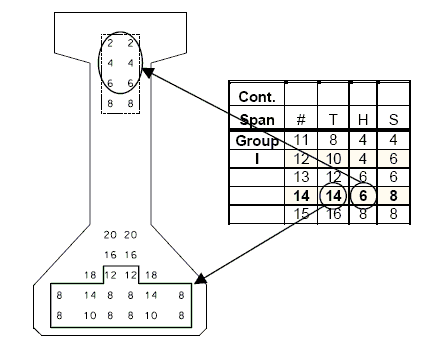
- GROUP I
Section Properties
Beam Type 2 -- 6" Web
Section Area = | 310.9 | in2 |
| ||||||||||||||||
Section = | 14.08 | in | |||||||||||||||||
= | 33,974 | in4 | |||||||||||||||||
Depth= | 32 | in | |||||||||||||||||
Strand Size= | 0.6 | in | |||||||||||||||||
= | 5 | ksi | |||||||||||||||||
= | 7 | ksi |
Iinitial | Ifinal | ||||||||||
# | T | H | S | e1 | e2 | e3 | A1 Bars 2-#5 |
A1 Bars 2-#6 |
A1 Bars 2-#5 |
A1 Bars, 2-#6 | |
Group | 1 | 8 | 4 | 4 | 11.08 | 11.08 | 13.92 | 36,407 | 36,838 | 36,062 | 36,429 |
---|---|---|---|---|---|---|---|---|---|---|---|
I | 2 | 10 | 4 | 6 | 11.41 | 11.08 | 13.92 | 36,828 | 37,265 | 36,424 | 36,797 |
3 | 12 | 6 | 6 | 11.41 | 10.08 | 12.92 | 36,983 | 37,424 | 36,559 | 36,935 | |
4 | 14 | 6 | 8 | 11.08 | 10.08 | 12.92 | 37,265 | 37,711 | 36,804 | 37,183 | |
5 | 16 | 8 | 8 | 11.08 | 9.08 | 11.92 | 37,304 | 37,753 | 36,839 | 37,221 | |
6 | 18 | 8 | 10 | 10.48 | 9.08 | 11.92 | 37,465 | 37,917 | 36,980 | 37,364 | |
Group | 7 | 8 | 2 | 6 | 11.41 | 10.08 | 14.92 | 36,407 | 36,837 | 36,061 | 36,429 |
II | 8 | 10 | 2 | 8 | 11.58 | 10.08 | 14.92 | 36,829 | 37,265 | 36,425 | 36,797 |
9 | 12 | 4 | 8 | 11.08 | 11.08 | 13.92 | 37,112 | 37,553 | 36,670 | 37,046 | |
10 | 14 | 4 | 10 | 11.28 | 9.08 | 13.92 | 37,265 | 37,711 | 36,804 | 37,183 | |
11 | 16 | 6 | 10 | 11.28 | 8.08 | 12.92 | 37,304 | 37,753 | 36,839 | 37,221 | |
12 | 18 | 6 | 12 | 10.75 | 8.08 | 12.92 | 37,466 | 37,918 | 36,981 | 37,365 | |
13 | 20 | 6 | 14 | 10.65 | 6.08 | 12.92 | 37,409 | 37,864 | 36,934 | 37,320 |
Section Properties
Beam Type 2 -- 7" Web
Section Area = | 342.9 | in2 |
| ||||||||||||||||
Section = | 14.26 | in | |||||||||||||||||
= | 36,812 | in4 | |||||||||||||||||
Depth= | 32 | in | |||||||||||||||||
Strand Size= | 0.6 | in | |||||||||||||||||
= | 5 | ksi | |||||||||||||||||
= | 7 | ksi |
Iinitial | Ifinal | ||||||||||
# | T | H | S | e1 | e2 | e3 | A1 Bars 2-#5 |
A1 Bars 2-#6 |
A1 Bars 2-#5 |
A1 Bars 2-#6 | |
Group | 1 | 8 | 4 | 4 | 11.26 | 11.26 | 13.74 | 39,272 | 39,691 | 38,922 | 39,281 |
---|---|---|---|---|---|---|---|---|---|---|---|
I | 2 | 10 | 4 | 6 | 11.59 | 11.26 | 13.74 | 39,706 | 40,132 | 39,297 | 39,660 |
3 | 12 | 6 | 6 | 11.59 | 10.26 | 12.74 | 39,871 | 40,300 | 39,440 | 39,806 | |
4 | 14 | 6 | 8 | 11.26 | 10.26 | 12.74 | 40,165 | 40,599 | 39,695 | 40,064 | |
5 | 16 | 8 | 8 | 11.26 | 9.26 | 11.74 | 40,211 | 40,648 | 39,736 | 40,108 | |
6 | 18 | 8 | 10 | 10.66 | 9.26 | 11.74 | 40,382 | 40,822 | 39,885 | 40,259 | |
Group | 7 | 8 | 2 | 6 | 11.59 | 10.26 | 14.74 | 39,271 | 39,691 | 38,921 | 39,280 |
II | 8 | 10 | 2 | 8 | 11.76 | 10.26 | 14.74 | 39,707 | 40,133 | 39,297 | 39,660 |
9 | 12 | 4 | 8 | 11.26 | 11.26 | 13.74 | 40,002 | 40,432 | 39,553 | 39,919 | |
10 | 14 | 4 | 10 | 11.46 | 9.26 | 13.74 | 40,165 | 40,599 | 39,695 | 40,064 | |
11 | 16 | 6 | 10 | 11.46 | 8.26 | 12.74 | 40,211 | 40,648 | 39,736 | 40,108 | |
12 | 18 | 6 | 12 | 10.93 | 8.26 | 12.74 | 40,383 | 40,823 | 39,886 | 40,260 | |
13 | 20 | 6 | 14 | 10.83 | 6.26 | 12.74 | 40,331 | 40,773 | 39,843 | 40,219 |
Section Properties
Beam Type 2 -- 8" Web
Section Area = | 374.9 | in2 |
| ||||||||||||||||
Section = | 14.41 | in | |||||||||||||||||
= | 39,632 | in4 | |||||||||||||||||
Depth= | 32 | in | |||||||||||||||||
Strand Size= | 0.6 | in | |||||||||||||||||
= | 5 | ksi | |||||||||||||||||
= | 7 | ksi |
Iinitial | Ifinal | ||||||||||
# | T | H | S | e1 | e2 | e3 | A1 Bars 2-#5 |
A1 Bars 2-#6 |
A1 Bars 2-#5 |
A1 Bars 2-#6 | |
Group | 1 | 8 | 4 | 4 | 11.41 | 11.41 | 13.59 | 42,114 | 42,525 | 41,761 | 42,113 |
---|---|---|---|---|---|---|---|---|---|---|---|
I | 2 | 10 | 4 | 6 | 11.74 | 11.41 | 13.59 | 42,561 | 42,977 | 42,146 | 42,502 |
3 | 12 | 6 | 6 | 11.74 | 10.41 | 12.59 | 42,734 | 43,154 | 42,296 | 42,654 | |
4 | 14 | 6 | 8 | 11.41 | 10.41 | 12.59 | 43,039 | 43,463 | 42,560 | 42,921 | |
5 | 16 | 8 | 8 | 11.41 | 9.41 | 11.59 | 43,091 | 43,518 | 42,607 | 42,970 | |
6 | 18 | 8 | 10 | 10.81 | 9.41 | 11.59 | 43,270 | 43,700 | 42,764 | 43,129 | |
Group | 7 | 8 | 2 | 6 | 11.74 | 10.41 | 14.59 | 42,114 | 42,525 | 41,761 | 42,112 |
II | 8 | 10 | 2 | 8 | 11.91 | 10.41 | 14.59 | 42,562 | 42,978 | 42,147 | 42,502 |
9 | 12 | 4 | 8 | 11.41 | 11.41 | 13.59 | 42,867 | 43,288 | 42,411 | 42,769 | |
10 | 14 | 4 | 10 | 11.61 | 9.41 | 13.59 | 43,039 | 43,463 | 42,560 | 42,921 | |
11 | 16 | 6 | 10 | 11.61 | 8.41 | 12.59 | 43,091 | 43,518 | 42,607 | 42,970 | |
12 | 18 | 6 | 12 | 11.08 | 8.41 | 12.59 | 43,271 | 43,701 | 42,765 | 43,130 | |
13 | 20 | 6 | 14 | 10.98 | 6.41 | 12.59 | 43,224 | 43,655 | 42,725 | 43,092 |
Section Properties
Beam Type 3 -- 6" Web
Section Area = | 381.9 | in2 |
| ||||||||||||||||
Section = | 17.08 | in | |||||||||||||||||
= | 61,841 | in4 | |||||||||||||||||
Depth= | 39 | in | |||||||||||||||||
Strand Size= | 0.6 | in | |||||||||||||||||
= | 5 | ksi | |||||||||||||||||
= | 7 | ksi |
Cont. | Iinitial | Ifinal | |||||||||
---|---|---|---|---|---|---|---|---|---|---|---|
Span | # | T | H | S | e1 | e2 | e3 | A1 Bars 2-#5 |
A1 Bars 2-#6 |
A1 Bars 2-#5 |
A1 Bars 2-#6 |
Group | 1 | 8 | 4 | 4 | 13.08 | 14.08 | 17.92 | 65,603 | 66,291 | 65,068 | 65,656 |
I | 2 | 10 | 4 | 6 | 13.75 | 14.08 | 17.92 | 66,265 | 66,962 | 65,638 | 66,233 |
3 | 12 | 4 | 8 | 13.58 | 14.08 | 17.92 | 66,753 | 67,457 | 66,060 | 66,660 | |
4 | 14 | 6 | 8 | 13.58 | 13.08 | 16.92 | 67,077 | 67,787 | 66,341 | 66,945 | |
5 | 16 | 6 | 10 | 13.48 | 13.08 | 16.92 | 67,555 | 68,271 | 66,755 | 67,364 | |
6 | 18 | 8 | 10 | 13.48 | 12.08 | 15.92 | 67,723 | 68,444 | 66,903 | 67,516 | |
7 | 20 | 8 | 12 | 13.08 | 12.08 | 15.92 | 68,042 | 68,769 | 67,182 | 67,799 | |
8 | 22 | 8 | 14 | 12.51 | 12.08 | 15.92 | 68,218 | 68,949 | 67,336 | 67,957 | |
9 | 24 | 10 | 14 | 12.51 | 11.08 | 14.92 | 68,260 | 68,994 | 67,376 | 67,998 | |
Group | 10 | 8 | 2 | 6 | 13.75 | 13.08 | 18.92 | 65,604 | 66,292 | 65,068 | 65,657 |
II | 11 | 10 | 2 | 8 | 14.08 | 13.08 | 18.92 | 66,264 | 66,961 | 65,637 | 66,232 |
12 | 12 | 2 | 10 | 13.88 | 13.08 | 18.92 | 66,753 | 67,457 | 66,060 | 66,660 | |
13 | 14 | 4 | 10 | 13.48 | 14.08 | 17.92 | 67,236 | 67,946 | 66,477 | 67,082 | |
14 | 16 | 4 | 12 | 13.75 | 12.08 | 17.92 | 67,556 | 68,272 | 66,756 | 67,366 | |
15 | 18 | 6 | 12 | 13.75 | 11.08 | 16.92 | 67,725 | 68,445 | 66,904 | 67,517 | |
16 | 20 | 6 | 14 | 13.37 | 11.08 | 16.92 | 68,045 | 68,771 | 67,184 | 67,800 | |
17 | 22 | 6 | 16 | 12.83 | 11.08 | 16.92 | 68,217 | 68,948 | 67,336 | 67,956 | |
18 | 24 | 8 | 16 | 12.83 | 10.08 | 15.92 | 68,259 | 68,993 | 67,375 | 67,998 |
Section Properties
Beam Type 3 -- 7" Web
Section Area = | 420.9 | in2 |
| ||||||||||||||||
Section = | 17.31 | in | |||||||||||||||||
= | 66,991 | in4 | |||||||||||||||||
Depth= | 39 | in | |||||||||||||||||
Strand Size= | 0.6 | in | |||||||||||||||||
= | 5 | ksi | |||||||||||||||||
= | 7 | ksi |
Cont. | Iinitial | Ifinal | |||||||||
---|---|---|---|---|---|---|---|---|---|---|---|
Span | # | T | H | S | e1 | e2 | e3 | A1 Bars 2-#5 |
A1 Bars 2-#6 |
A1 Bars 2-#5 |
A1 Bars 2-#6 |
Group | 1 | 8 | 4 | 4 | 13.31 | 14.31 | 17.69 | 70,792 | 71,464 | 70,251 | 70,826 |
I | 2 | 10 | 4 | 6 | 13.98 | 14.31 | 17.69 | 71,477 | 72,156 | 70,841 | 71,420 |
3 | 12 | 4 | 8 | 13.81 | 14.31 | 17.69 | 71,985 | 72,670 | 71,279 | 71,864 | |
4 | 14 | 6 | 8 | 13.81 | 13.31 | 16.69 | 72,326 | 73,016 | 71,575 | 72,163 | |
5 | 16 | 6 | 10 | 13.71 | 13.31 | 16.69 | 72,823 | 73,520 | 72,006 | 72,599 | |
6 | 18 | 8 | 10 | 13.71 | 12.31 | 15.69 | 73,006 | 73,707 | 72,166 | 72,762 | |
7 | 20 | 8 | 12 | 13.31 | 12.31 | 15.69 | 73,342 | 74,049 | 72,459 | 73,060 | |
8 | 22 | 8 | 14 | 12.74 | 12.31 | 15.69 | 73,532 | 74,242 | 72,626 | 73,229 | |
9 | 24 | 10 | 14 | 12.74 | 11.31 | 14.69 | 73,584 | 74,298 | 72,675 | 73,280 | |
Group | 10 | 8 | 2 | 6 | 13.98 | 13.31 | 18.69 | 70,793 | 71,465 | 70,252 | 70,826 |
II | 11 | 10 | 2 | 8 | 14.31 | 13.31 | 18.69 | 71,476 | 72,155 | 70,840 | 71,420 |
12 | 12 | 2 | 10 | 14.11 | 13.31 | 18.69 | 71,985 | 72,670 | 71,279 | 71,864 | |
13 | 14 | 4 | 10 | 13.71 | 14.31 | 17.69 | 72,487 | 73,178 | 71,714 | 72,303 | |
14 | 16 | 4 | 12 | 13.98 | 12.31 | 17.69 | 72,825 | 73,522 | 72,007 | 72,600 | |
15 | 18 | 6 | 12 | 13.98 | 11.31 | 16.69 | 73,007 | 73,708 | 72,167 | 72,764 | |
16 | 20 | 6 | 14 | 13.60 | 11.31 | 16.69 | 73,344 | 74,051 | 72,461 | 73,061 | |
17 | 22 | 6 | 16 | 13.06 | 11.31 | 16.69 | 73,531 | 74,242 | 72,625 | 73,229 | |
18 | 24 | 8 | 16 | 13.06 | 10.31 | 15.69 | 73,584 | 74,298 | 72,674 | 73,280 |
Section Properties
Beam Type 3 -- 8" Web
Section Area = | 459.9 | in2 |
| ||||||||||||||||
Section = | 17.49 | in | |||||||||||||||||
= | 72,106 | in4 | |||||||||||||||||
Depth= | 39 | in | |||||||||||||||||
Strand Size= | 0.60 | in | |||||||||||||||||
= | 5 | ksi | |||||||||||||||||
= | 7 | ksi |
Cont. | Iinitial | Ifinal | |||||||||
---|---|---|---|---|---|---|---|---|---|---|---|
Span | # | T | H | S | e1 | e2 | e3 | A1 Bars 2-#5 |
A1 Bars 2-#6 |
A1 Bars 2-#5 |
A1 Bars 2-#6 |
Group | 1 | 8 | 4 | 4 | 13.49 | 14.49 | 17.51 | 75,940 | 76,598 | 75,394 | 75,957 |
I | 2 | 10 | 4 | 6 | 14.16 | 14.49 | 17.51 | 76,642 | 77,307 | 75,999 | 76,567 |
3 | 12 | 4 | 8 | 13.99 | 14.49 | 17.51 | 77,166 | 77,837 | 76,451 | 77,023 | |
4 | 14 | 6 | 8 | 13.99 | 13.49 | 16.51 | 77,520 | 78,196 | 76,758 | 77,334 | |
5 | 16 | 6 | 10 | 13.89 | 13.49 | 16.51 | 78,034 | 78,716 | 77,203 | 77,783 | |
6 | 18 | 8 | 10 | 13.89 | 12.49 | 15.51 | 78,229 | 78,914 | 77,373 | 77,956 | |
7 | 20 | 8 | 12 | 13.49 | 12.49 | 15.51 | 78,580 | 79,270 | 77,678 | 78,265 | |
8 | 22 | 8 | 14 | 12.92 | 12.49 | 15.51 | 78,781 | 79,475 | 77,855 | 78,445 | |
9 | 24 | 10 | 14 | 12.92 | 11.49 | 14.51 | 78,843 | 79,540 | 77,911 | 78,504 | |
Group | 10 | 8 | 2 | 6 | 14.16 | 13.49 | 18.51 | 75,941 | 76,599 | 75,395 | 75,958 |
II | 11 | 10 | 2 | 8 | 14.49 | 13.49 | 18.51 | 76,641 | 77,306 | 75,998 | 76,566 |
12 | 12 | 2 | 10 | 14.29 | 13.49 | 18.51 | 77,166 | 77,837 | 76,451 | 77,023 | |
13 | 14 | 4 | 10 | 13.89 | 14.49 | 17.51 | 77,684 | 78,361 | 76,899 | 77,476 | |
14 | 16 | 4 | 12 | 14.16 | 12.49 | 17.51 | 78,036 | 78,718 | 77,204 | 77,785 | |
15 | 18 | 6 | 12 | 14.16 | 11.49 | 16.51 | 78,230 | 78,916 | 77,374 | 77,957 | |
16 | 20 | 6 | 14 | 13.78 | 11.49 | 16.51 | 78,582 | 79,273 | 77,680 | 78,267 | |
17 | 22 | 6 | 16 | 13.24 | 11.49 | 16.51 | 78,780 | 79,475 | 77,854 | 78,444 | |
18 | 24 | 8 | 16 | 13.24 | 10.49 | 15.51 | 78,842 | 79,540 | 77,911 | 78,503 |
Section Properties
Beam Type 4 -- 6" Web
Section Area = | 428.9 | in2 |
| ||||||||||||||||
Section = | 19.54 | in | |||||||||||||||||
= | 92,450 | in4 | |||||||||||||||||
Depth= | 45 | in | |||||||||||||||||
Strand Size= | 0.6 | in | |||||||||||||||||
= | 5 | ksi | |||||||||||||||||
= | 7 | ksi |
Cont. | Iinitial | Ifinal | |||||||||
---|---|---|---|---|---|---|---|---|---|---|---|
Span | # | T | H | S | e1 | e2 | e3 | A1 Bars 2-#5 |
A1 Bars 2-#6 |
A1 Bars 2-#5 |
A1 Bars 2-#6 |
Group | 1 | 8 | 4 | 4 | 15.54 | 16.54 | 21.46 | 97,723 | 98,691 | 96,972 | 97,800 |
I | 2 | 10 | 4 | 6 | 16.21 | 16.54 | 21.46 | 98,623 | 99,602 | 97,748 | 98,583 |
3 | 12 | 4 | 8 | 16.04 | 16.54 | 21.46 | 99,318 | 100,305 | 98,347 | 99,189 | |
4 | 14 | 6 | 8 | 16.04 | 15.54 | 20.46 | 99,818 | 100,812 | 98,780 | 99,627 | |
5 | 16 | 6 | 10 | 15.94 | 15.54 | 20.46 | 100,497 | 101,501 | 99,369 | 100,223 | |
6 | 18 | 8 | 10 | 15.94 | 14.54 | 19.46 | 100,808 | 101,818 | 99,640 | 100,499 | |
7 | 20 | 8 | 12 | 15.54 | 14.54 | 19.46 | 101,297 | 102,314 | 100,066 | 100,930 | |
8 | 22 | 8 | 14 | 14.97 | 14.54 | 19.46 | 101,611 | 102,634 | 100,341 | 101,210 | |
9 | 24 | 8 | 16 | 15.29 | 12.54 | 19.46 | 101,761 | 102,789 | 100,475 | 101,347 | |
10 | 26 | 10 | 16 | 15.29 | 11.54 | 18.46 | 101,762 | 102,794 | 100,480 | 101,356 | |
11 | 28 | 10 | 18 | 15.32 | 9.54 | 18.46 | 101,633 | 102,667 | 100,372 | 101,250 | |
Group | 12 | 8 | 2 | 6 | 16.21 | 15.54 | 22.46 | 97,724 | 98,692 | 96,973 | 97,801 |
II | 13 | 10 | 2 | 8 | 16.54 | 15.54 | 22.46 | 98,622 | 99,601 | 97,747 | 98,582 |
14 | 12 | 4 | 8 | 16.04 | 16.54 | 21.46 | 99,318 | 100,305 | 98,347 | 99,189 | |
15 | 14 | 4 | 10 | 15.94 | 16.54 | 21.46 | 100,005 | 101,001 | 98,941 | 99,790 | |
16 | 16 | 4 | 12 | 16.21 | 14.54 | 21.46 | 100,499 | 101,503 | 99,370 | 100,224 | |
17 | 16 | 6 | 10 | 15.94 | 15.54 | 20.46 | 100,497 | 101,501 | 99,369 | 100,223 | |
18 | 18 | 6 | 12 | 16.21 | 13.54 | 20.46 | 100,810 | 101,819 | 99,641 | 100,500 | |
19 | 20 | 6 | 14 | 15.83 | 13.54 | 20.46 | 101,300 | 102,317 | 100,068 | 100,932 | |
20 | 22 | 6 | 16 | 15.29 | 13.54 | 20.46 | 101,610 | 102,633 | 100,340 | 101,209 | |
21 | 24 | 6 | 18 | 15.32 | 11.54 | 20.46 | 101,762 | 102,790 | 100,476 | 101,349 | |
22 | 26 | 6 | 20 | 15.14 | 9.54 | 20.46 | 101,762 | 102,794 | 100,480 | 101,356 | |
23 | 26 | 8 | 18 | 15.32 | 10.54 | 19.46 | 101,764 | 102,796 | 100,482 | 101,357 | |
24 | 28 | 6 | 22 | 14.81 | 7.54 | 20.46 | 101,629 | 102,663 | 100,369 | 101,246 | |
25 | 28 | 8 | 20 | 15.14 | 8.54 | 19.46 | 101,631 | 102,666 | 100,371 | 101,248 | |
26 | 30 | 8 | 22 | 14.81 | 6.54 | 19.46 | 101,381 | 102,417 | 100,158 | 101,037 | |
27 | 32 | 8 | 24 | 14.37 | 4.54 | 19.46 | 101,033 | 102,069 | 99,860 | 100,739 |
Section Properties
Beam Type 4 -- 7" Web
Section Area = | 473.9 | in2 |
| ||||||||||||||||
Section = | 19.82 | in | |||||||||||||||||
= | 100,400 | in4 | |||||||||||||||||
Depth= | 45 | in | |||||||||||||||||
Strand Size= | 0.6 | in | |||||||||||||||||
= | 5 | ksi | |||||||||||||||||
= | 7 | ksi |
Cont. | Iinitial | Ifinal | |||||||||
---|---|---|---|---|---|---|---|---|---|---|---|
Span | # | T | H | S | e1 | e2 | e3 | A1 Bars 2-#5 |
A1 Bars 2-#6 |
A1 Bars 2-#5 |
A1 Bars 2-#6 |
Group | 1 | 8 | 4 | 4 | 15.82 | 16.82 | 21.18 | 105,729 | 106,673 | 104,971 | 105,778 |
I | 2 | 10 | 4 | 6 | 16.49 | 16.82 | 21.18 | 106,661 | 107,614 | 105,773 | 106,587 |
3 | 12 | 4 | 8 | 16.32 | 16.82 | 21.18 | 107,384 | 108,345 | 106,396 | 107,216 | |
4 | 14 | 6 | 8 | 16.32 | 15.82 | 20.18 | 107,908 | 108,876 | 106,850 | 107,675 | |
5 | 16 | 6 | 10 | 16.22 | 15.82 | 20.18 | 108,617 | 109,593 | 107,464 | 108,295 | |
6 | 18 | 8 | 10 | 16.22 | 14.82 | 19.18 | 108,950 | 109,931 | 107,753 | 108,589 | |
7 | 20 | 8 | 12 | 15.82 | 14.82 | 19.18 | 109,464 | 110,453 | 108,201 | 109,041 | |
8 | 22 | 8 | 14 | 15.25 | 14.82 | 19.18 | 109,801 | 110,795 | 108,495 | 109,340 | |
9 | 24 | 8 | 16 | 15.57 | 12.82 | 19.18 | 109,968 | 110,967 | 108,644 | 109,492 | |
10 | 26 | 10 | 16 | 15.57 | 11.82 | 18.18 | 109,984 | 110,986 | 108,661 | 109,512 | |
11 | 28 | 10 | 18 | 15.60 | 9.82 | 18.18 | 109,864 | 110,869 | 108,562 | 109,415 | |
Group | 12 | 8 | 2 | 6 | 16.49 | 15.82 | 22.18 | 105,730 | 106,674 | 104,971 | 105,779 |
II | 13 | 10 | 2 | 8 | 16.82 | 15.82 | 22.18 | 106,660 | 107,613 | 105,772 | 106,586 |
14 | 12 | 4 | 8 | 16.32 | 16.82 | 21.18 | 107,384 | 108,345 | 106,396 | 107,216 | |
15 | 14 | 4 | 10 | 16.22 | 16.82 | 21.18 | 108,100 | 109,069 | 107,015 | 107,841 | |
16 | 16 | 4 | 12 | 16.49 | 14.82 | 21.18 | 108,619 | 109,595 | 107,465 | 108,296 | |
17 | 16 | 6 | 10 | 16.22 | 15.82 | 20.18 | 108,617 | 109,593 | 107,464 | 108,295 | |
18 | 18 | 6 | 12 | 16.49 | 13.82 | 20.18 | 108,951 | 109,933 | 107,755 | 108,590 | |
19 | 20 | 6 | 14 | 16.11 | 13.82 | 20.18 | 109,467 | 110,456 | 108,203 | 109,044 | |
20 | 22 | 6 | 16 | 15.57 | 13.82 | 20.18 | 109,800 | 110,794 | 108,484 | 109,339 | |
21 | 24 | 6 | 18 | 15.60 | 11.82 | 20.18 | 109,970 | 110,969 | 108,645 | 109,494 | |
22 | 26 | 6 | 20 | 15.42 | 9.82 | 20.18 | 109,984 | 110,986 | 108,661 | 109,512 | |
23 | 26 | 8 | 18 | 15.60 | 10.82 | 19.18 | 109,985 | 110,988 | 108,663 | 109,514 | |
24 | 28 | 6 | 22 | 15.09 | 7.82 | 20.18 | 109,860 | 110,865 | 108,559 | 109,411 | |
25 | 28 | 8 | 20 | 15.42 | 8.82 | 19.18 | 109,862 | 110,867 | 108,561 | 109,413 | |
26 | 30 | 8 | 22 | 15.09 | 6.82 | 19.18 | 109,618 | 110,624 | 108,353 | 109,207 | |
27 | 32 | 8 | 24 | 14.65 | 4.82 | 19.18 | 109,271 | 110,278 | 108,056 | 108,910 |
Section Properties
Beam Type 4 -- 8" Web
Section Area = | 518.9 | in2 |
| ||||||||||||||||
Section = | 20.06 | in | |||||||||||||||||
= | 108,288 | in4 | |||||||||||||||||
Depth= | 45 | in | |||||||||||||||||
Strand Size= | 0.6 | in | |||||||||||||||||
= | 5 | ksi | |||||||||||||||||
= | 7 | ksi |
Cont. | Iinitial | Ifinal | |||||||||
---|---|---|---|---|---|---|---|---|---|---|---|
Span | # | T | H | S | e1 | e2 | e3 | A1 Bars 2-#5 |
A1 Bars 2-#6 |
A1 Bars 2-#5 |
A1 Bars 2-#6 |
Group | 1 | 8 | 4 | 4 | 16.06 | 17.06 | 20.94 | 113,668 | 114,591 | 112,902 | 113,692 |
I | 2 | 10 | 4 | 6 | 16.73 | 17.06 | 20.94 | 114,627 | 115,559 | 113,727 | 114,523 |
3 | 12 | 4 | 8 | 16.56 | 17.06 | 20.94 | 115,375 | 116,314 | 114,372 | 115,174 | |
4 | 14 | 6 | 8 | 16.56 | 16.06 | 19.94 | 115,921 | 116,866 | 114,844 | 115,651 | |
5 | 16 | 6 | 10 | 16.46 | 16.06 | 19.94 | 116,655 | 117,608 | 115,480 | 116,291 | |
6 | 18 | 8 | 10 | 16.46 | 15.06 | 18.94 | 117,007 | 117,965 | 115,786 | 116,601 | |
7 | 20 | 8 | 12 | 16.06 | 15.06 | 18.94 | 117,544 | 118,509 | 116,252 | 117,073 | |
8 | 22 | 8 | 14 | 15.49 | 15.06 | 18.94 | 117,900 | 118,870 | 116,563 | 117,387 | |
9 | 24 | 8 | 16 | 15.81 | 13.06 | 18.94 | 118,084 | 119,058 | 119,725 | 117,553 | |
10 | 26 | 10 | 16 | 15.81 | 12.06 | 17.94 | 118,112 | 119,089 | 116,754 | 117,584 | |
11 | 28 | 10 | 18 | 15.84 | 10.06 | 17.94 | 118,001 | 118,981 | 116,662 | 117,494 | |
Group | 12 | 8 | 2 | 6 | 16.73 | 16.06 | 21.94 | 113,669 | 114,592 | 112,903 | 113,693 |
II | 13 | 10 | 2 | 8 | 17.06 | 16.06 | 21.94 | 114,626 | 115,558 | 113,726 | 114,522 |
14 | 12 | 4 | 8 | 16.56 | 17.06 | 20.94 | 115,375 | 116,314 | 114,372 | 115,174 | |
15 | 14 | 4 | 10 | 16.46 | 17.06 | 20.94 | 116,116 | 117,062 | 115,012 | 115,819 | |
16 | 16 | 4 | 12 | 16.73 | 15.06 | 20.94 | 116,657 | 117,610 | 115,481 | 116,293 | |
17 | 16 | 6 | 10 | 16.46 | 16.06 | 19.94 | 116,655 | 117,608 | 115,480 | 116,291 | |
18 | 18 | 6 | 12 | 16.73 | 14.06 | 19.94 | 117,009 | 117,967 | 115,787 | 116,603 | |
19 | 20 | 6 | 14 | 16.35 | 14.06 | 19.94 | 117,547 | 118,512 | 116,255 | 117,075 | |
20 | 22 | 6 | 16 | 15.81 | 14.06 | 19.94 | 117,899 | 118,869 | 116,562 | 117,387 | |
21 | 24 | 6 | 18 | 15.84 | 12.06 | 19.94 | 118,085 | 119,059 | 116,727 | 117,554 | |
22 | 26 | 6 | 20 | 15.66 | 10.06 | 19.94 | 118,112 | 119,089 | 116,754 | 117,584 | |
23 | 26 | 8 | 18 | 15.84 | 11.06 | 18.94 | 118,113 | 119,091 | 116,755 | 117,585 | |
24 | 28 | 6 | 22 | 15.33 | 8.06 | 19.94 | 117,997 | 118,977 | 116,659 | 117,490 | |
25 | 28 | 8 | 20 | 15.66 | 9.06 | 18.94 | 117,999 | 118,979 | 116,661 | 117,493 | |
26 | 30 | 8 | 22 | 15.33 | 7.06 | 18.94 | 117,760 | 118,742 | 116,458 | 117,291 | |
27 | 32 | 8 | 24 | 14.89 | 5.06 | 18.94 | 117,415 | 118,397 | 116,163 | 116,996 |
Section Properties
Beam Type 6 -- 6.5" Web
Section Area = | 643.6 | in2 |
| ||||||||||||||||
Section = | 25.92 | in | |||||||||||||||||
= | 235,735 | in4 | |||||||||||||||||
Depth= | 54 | in | |||||||||||||||||
Strand Size= | 0.6 | in | |||||||||||||||||
= | 5 | ksi | |||||||||||||||||
= | 7 | ksi |
Iinitial | Ifinal | ||||||||
# | T | H | S | e1 | e2 | e3 | A1 Bars 2-#6 |
A1 Bars 2-#6 | |
Group | 1 | 14 | 4 | 10 | 23.52 | 22.92 | 23.08 | 251,047 | 248,880 |
---|---|---|---|---|---|---|---|---|---|
I | 2 | 16 | 4 | 12 | 23.25 | 22.92 | 23.08 | 252,425 | 250,070 |
3 | 18 | 6 | 12 | 23.25 | 21.92 | 22.08 | 253,525 | 251,022 | |
4 | 20 | 6 | 14 | 23.06 | 21.92 | 22.08 | 254,886 | 252,199 | |
5 | 22 | 6 | 16 | 22.92 | 21.92 | 22.08 | 256,238 | 253,370 | |
6 | 24 | 8 | 16 | 22.92 | 20.92 | 21.08 | 257,053 | 254,081 | |
7 | 26 | 8 | 18 | 22.59 | 20.92 | 21.08 | 258,130 | 255,017 | |
8 | 28 | 8 | 20 | 22.32 | 20.92 | 21.08 | 259,191 | 255,940 | |
9 | 30 | 10 | 20 | 22.32 | 19.92 | 20.08 | 259,751 | 256,433 | |
10 | 32 | 10 | 22 | 22.10 | 19.92 | 20.08 | 260,803 | 257,350 | |
11 | 34 | 10 | 24 | 21.75 | 19.92 | 20.08 | 261,604 | 258,052 | |
12 | 36 | 10 | 26 | 21.46 | 19.92 | 20.08 | 262,412 | 258,760 | |
13 | 38 | 12 | 26 | 21.46 | 18.92 | 19.08 | 262,739 | 259,053 |
Section Properties
Beam Type 6 -- 7.5" Web
Section Area = | 697.6 | in2 |
| ||||||||||||||||
Section = | 26.00 | in | |||||||||||||||||
= | 248,915 | in4 | |||||||||||||||||
Depth= | 54 | in | |||||||||||||||||
Strand Size= | 0.6 | in | |||||||||||||||||
= | 5 | ksi | |||||||||||||||||
= | 7 | ksi |
Iinitial | Ifinal | ||||||||
# | T | H | S | e1 | e2 | e3 | A1 Bars 2-#6 |
A1 Bars 2-#6 | |
Group | 1 | 14 | 4 | 10 | 23.60 | 23.00 | 23.00 | 264,293 | 262,115 |
---|---|---|---|---|---|---|---|---|---|
I | 2 | 16 | 4 | 12 | 23.33 | 23.00 | 23.00 | 265,686 | 263,318 |
3 | 18 | 6 | 12 | 23.33 | 22.00 | 22.00 | 266,801 | 264,281 | |
4 | 20 | 6 | 14 | 23.14 | 22.00 | 22.00 | 268,178 | 265,473 | |
5 | 22 | 6 | 16 | 23.00 | 22.00 | 22.00 | 269,548 | 266,658 | |
6 | 24 | 8 | 16 | 23.00 | 21.00 | 21.00 | 270,378 | 267,381 | |
7 | 26 | 8 | 18 | 22.67 | 21.00 | 21.00 | 271,472 | 268,330 | |
8 | 28 | 8 | 20 | 22.40 | 21.00 | 21.00 | 272,551 | 269,269 | |
9 | 30 | 10 | 20 | 22.40 | 20.00 | 20.00 | 273,125 | 269,772 | |
10 | 32 | 10 | 22 | 22.18 | 20.00 | 20.00 | 274,195 | 270,705 | |
11 | 34 | 10 | 24 | 21.83 | 20.00 | 20.00 | 275,014 | 271,420 | |
12 | 36 | 10 | 26 | 21.54 | 20.00 | 20.00 | 275,839 | 272,143 | |
13 | 38 | 12 | 26 | 21.54 | 19.00 | 19.00 | 276,180 | 272,447 |
Section Properties
Beam Type 6 -- 8.5" Web
Section Area = | 751.6 | in2 |
| ||||||||||||||||
Section = | 26.07 | in | |||||||||||||||||
= | 262,087 | in4 | |||||||||||||||||
Depth= | 54 | in | |||||||||||||||||
Strand Size= | 0.6 | in | |||||||||||||||||
= | 5 | ksi | |||||||||||||||||
= | 7 | ksi |
Iinitial | Ifinal | ||||||||
# | T | H | S | e1 | e2 | e3 | A1 Bars 2-#6 |
A1 Bars 2-#6 | |
Group | 1 | 14 | 4 | 10 | 23.67 | 23.07 | 22.93 | 277,522 | 275,336 |
---|---|---|---|---|---|---|---|---|---|
I | 2 | 16 | 4 | 12 | 23.40 | 23.07 | 22.93 | 278,930 | 276,549 |
3 | 18 | 6 | 12 | 23.40 | 22.07 | 21.93 | 280,057 | 277,523 | |
4 | 20 | 6 | 14 | 23.21 | 22.07 | 21.93 | 281,449 | 278,727 | |
5 | 22 | 6 | 16 | 23.07 | 22.07 | 21.93 | 282,834 | 279,925 | |
6 | 24 | 8 | 16 | 23.07 | 21.07 | 20.93 | 283,678 | 280,658 | |
7 | 26 | 8 | 18 | 22.74 | 21.07 | 20.93 | 284,786 | 281,620 | |
8 | 28 | 8 | 20 | 22.47 | 21.07 | 20.93 | 285,881 | 282,571 | |
9 | 30 | 10 | 20 | 22.47 | 20.07 | 19.93 | 286,468 | 283,085 | |
10 | 32 | 10 | 22 | 22.25 | 20.07 | 19.93 | 287,554 | 284,030 | |
11 | 34 | 10 | 24 | 21.90 | 20.07 | 19.93 | 288,388 | 284,758 | |
12 | 36 | 10 | 26 | 21.61 | 20.07 | 19.93 | 289,228 | 285,493 | |
13 | 38 | 12 | 26 | 21.61 | 19.07 | 18.93 | 289,581 | 285,807 |
Section Properties
Beam Type 7 -- 6" Web
Bulb-Tee Girder
Section Area = | 787.4 | in2 |
| ||||||||||||||||
Section = | 37.58 | in | |||||||||||||||||
= | 571,047 | in4 | |||||||||||||||||
Depth= | 72.5 | in | |||||||||||||||||
Strand Size= | 0.6 | in | |||||||||||||||||
= | 5 | ksi | |||||||||||||||||
= | 7 | ksi |
Cont. | Iinitial | Ifinal | |||||||
---|---|---|---|---|---|---|---|---|---|
Span | # | T | H | S | e1 | e2 | e3 | A1 Bars 4-#6 |
A1 Bars 4-#6 |
Group | 1 | 14 | 4 | 10 | 35.58 | 34.58 | 29.92 | 609,994 | 604,448 |
I | 2 | 16 | 4 | 12 | 35.25 | 34.58 | 29.92 | 613,316 | 607,307 |
3 | 18 | 6 | 12 | 35.25 | 33.58 | 28.92 | 616,196 | 609,790 | |
4 | 20 | 6 | 14 | 35.01 | 33.58 | 28.92 | 619,469 | 612,612 | |
5 | 22 | 6 | 16 | 34.83 | 33.58 | 28.92 | 622,719 | 615,417 | |
6 | 24 | 8 | 16 | 34.83 | 32.58 | 27.92 | 625,140 | 617,512 | |
7 | 26 | 8 | 18 | 34.69 | 32.58 | 27.92 | 628,347 | 620,286 | |
8 | 28 | 8 | 20 | 34.58 | 32.58 | 27.92 | 631,536 | 623,046 | |
9 | 30 | 10 | 20 | 34.58 | 31.58 | 26.92 | 633,518 | 624,769 | |
10 | 32 | 10 | 22 | 34.31 | 31.58 | 26.92 | 636,280 | 627,166 | |
11 | 34 | 10 | 24 | 34.08 | 31.58 | 26.92 | 639,012 | 629,539 | |
12 | 36 | 10 | 26 | 33.89 | 31.58 | 26.92 | 641,737 | 631,909 | |
13 | 38 | 10 | 28 | 33.58 | 31.58 | 26.92 | 644,052 | 633,926 | |
14 | 40 | 12 | 28 | 33.58 | 30.58 | 25.92 | 645,607 | 635,289 |
751.22.3.6 Girder Reinforcement
751.22.3.6.1 Reinforcing Steel Details
See Bridge Standard Drawings for details not shown below.
TABLE OF DIMENSIONS BY GIRDER TYPE | |||||||||||||
TYPE 2 | TYPE 3 | TYPE 4 | TYPE 6 | TYPE 7 | |||||||||
WEB | 6" | 7" | 8" | 6" | 7" | 8" | 6" | 7" | 8" | 6½" | 7½" | 8½" | 6" |
"A" | 5½" | 5½" | 5½" | 5½" | 5½" | 5½" | 5½" | 5½" | 5½" | 8¾" | 8¾" | 8¾" | 10" |
"B" | 4" | 4" | 4" | 4" | 4" | 4" | 4" | 4" | 4" | 4" | 4" | 4" | 4" |
"C" | 6" | 6" | 6" | 6" | 6" | 6" | 6" | 6" | 6" | 7" | 7" | 7" | 4½" |
"D" | 3¼" | 3¼" | 3¼" | 5⅛" | 5⅛" | 5⅛" | 6¼" | 6¼" | 6¼" | 4⅛" | 4⅛" | 4⅛" | 4⅛" |
"E" | 13" | 14" | 15" | 13" | 14" | 15" | 13" | 14" | 15" | 18" | 19" | 20" | 20" |
"F" | 2" | 2" | 2" | 2" | 2" | 2" | 2" | 2" | 2" | 3" | 3" | 3" | 7¾" |
"G" | 11" | 12" | 13" | 11" | 12" | 13" | 11" | 12" | 13" | 22" | 23" | 24" | 2'-10" |
"H" | 2'-6" | 2'-6" | 2'-6" | 3'-1" | 3'-1" | 3'-1" | 3'-7" | 3'-7" | 3'-7" | 4'-4" | 4'-4" | 4'-4" | 5'-10½" |
"I" | 3'-0½" | 3'-0½" | 3'-0½" | 3'-7½" | 3'-7½" | 3'-7½" | 4'-1½" | 4'-1½" | 4'-1½" | 4'-10½" | 4'-10½" | 4'-10½" | 6'-5" |
TOTAL BAR LENGTH BY GIRDER TYPE | |||||||||||||
TYPE 2 | TYPE 3 | TYPE 4 | TYPE 6 | TYPE 7 | |||||||||
WEB | 6" | 7" | 8" | 6" | 7" | 8" | 6" | 7" | 8" | 6½" | 7½" | 8½" | 6" |
#4-B1 | 4'-1" | 4'-1" | 4'-1" | 4'-8" | 4'-8" | 4'-8" | 5'-2" | 5'-2" | 5'-2" | 5'-11" | 5'-11" | 5'-11" | 7'-8" |
#5-B1 | 4'-1" | 4'-1" | 4'-1" | 4'-8" | 4'-8" | 4'-8" | 5'-2" | 5'-2" | 5'-2" | 5'-11" | 5'-11" | 5'-11" | 7'-7" |
#6-B1 | 3'-11" | 3'-11" | 3'-11" | 4'-6" | 4'-6" | 4'-6" | 5'-0" | 5'-0" | 5'-0" | 5'-9" | 5'-9" | 5'-9" | 7'-6" |
#6-B2 | 3'-5" | 3'-5" | 3'-5" | 4'-0" | 4'-0" | 4'-0" | 4'-6" | 4'-6" | 4'-6" | 5'-3" | 5'-3" | 5'-3" | 6'-11" |
#4-C1 | 13" | 14" | 15" | 13" | 14" | 15" | 13" | 14" | 15" | 2'-2" | 2'-3" | 2'-4" | 3'-5" |
#4-D1 | 2'-3" | 2'-4" | 2'-5" | 2'-5" | 2'-6" | 2'-7" | 2'-6" | 2'-7" | 2'-8" | 3'-0" | 3'-1" | 3'-2" | 3'-1" |
Note: For girders that have excessive haunch or girder steps, create new B1 and C1 bars and adjust heights in one-inch increments or provide #4 hairpin bars in accordance with EPG 751.10.1.14 Girder and Beam Haunch Reinforcement to ensure at least 2 inches of embedment into slab.
![]() |
![]() |
![]() |
C1 BAR
(Girders Type 2-6) |
C1 BAR
(Girder Type 7) | |
B1 and B2 Bar | ![]() | |
![]() |
![]() | |
D1 BAR | ||
SECTION THRU GIRDER
(Typical for MoDOT standard girder Type 2-6) |
SECTION THRU GIRDER
(MoDOT standard girder Type 7) |
Welded Wire Reinforcing Steel Details for NU Standard Girders
See Bridge Standard Drawings for details. For girders that have excessive haunch or girder steps, create new WWR and adjust heights in one inch increments or provide #4 hairpin bars in accordance with EPG 751.10.1.14 Girder and Beam Haunch Reinforcement to ensure at least 2 inches of embedment into slab. Length of WWR sections should be based on shear and confinement requirements before adjusting height to avoid multiple short sections.
Alternate Bar Reinforcing Steel Details for NU Standard Girders
Alternate bar reinforcing steel details shall be provided for all NU girders for all spans.
See Bridge Standard Drawings for details. For girders that have excessive haunch or girder steps, create new B1 bars and adjust heights in one inch increments or provide #4 hairpin bars in accordance with EPG 751.10.1.14 Girder and Beam Haunch Reinforcement to ensure at least 2 inches of embedment into slab.
751.22.3.6.2 Shear Reinforcement
The following criteria are preferred by girder manufacturers and reinforcement suppliers. If the design requires a deviation from the preferred criteria then feasibility should be verified with a manufacturer.
MoDOT Standard Girders and NU Standard Girders with Alternate Bar Reinforcing Steel
- B1 bars shall be either #4 or #5 epoxy-coated bars with #4 bars preferred to allow permissible alternate bar shape. Using #6 B1 bars does not provide one inch clearance when center strands are spaced one inch off centerline of girder between hold down devices because of bend radius of the #6 bars.
- The same shear reinforcement bar size shall be used in a girder. Using the same shear reinforcement bar size for all of the spans is preferred but not required for girders of different spans lengths.
- 6” is the preferred minimum spacing.
- 5” spacing may be used for first set if required.
- 21” is the maximum spacing for #4 bars.
- 24” is the maximum spacing for #5 bars.
- 3” increment spacing shall be used (i.e. 6”, 9”, 12”, 15”, 18”, 21” and 24”) except when less than 6” spacing is required for the first set. In this case, 6” or 9” shall be used for the next set of B1 bars.
- Four or less spacing changes are preferred for spans up to 100 feet.
- Six spacing changes may be used for spans greater than 100 feet.
- Using the same spacing scenario (i.e. sets of B1 bars at 6”, 12” and 18” spacing) for all of spans is preferred but not required for girders of different span lengths.
NU Standard Girders with Welded Wire Reinforcing Steel
- WWR shall be uncoated and shall use either D18, D20, D22 or D31 vertical wire sizes.
- The same shear reinforcement wire size shall be used in a girder. Using the same shear reinforcement wire size for all of the spans is preferred but not required for girders of different spans lengths.
- 4” is the preferred minimum spacing.
- 2” or 3” spacing (maximum eight spaces) may be used for WWR1 if required.
- 20” is the maximum spacing for the D18, D20 and D22 wire sizes.
- 24” is the maximum spacing for the D31 wire size.
- 4” increment spacing shall be used (i.e. 4”, 8”, 12”, 16”, 20” and 24”) except when the required spacing of WWR1 is less than 4”. In this case, 4” or 8” shall be used for WWR2.
- Three or less spacing changes (WWR pieces) are preferred for spans less than 100 feet.
- An additional spacing change (WWR piece) may be used when the spacing of WWR1 is less than 4” or in spans greater than 100 feet.
- Using the same spacing scenario (i.e. S1=4”, S2=12” and S3=20”) for all of the spans is preferred but not required for girders of different span lengths.
751.22.3.6.3 Anchorage Zone Reinforcement
The following details meet the criteria for anchorage zone reinforcement for pretensioned girders in EPG 751.22.2.4 for all MoDOT and NU standard girder shapes.
MoDOT Standard Girder End Section Reinforcement
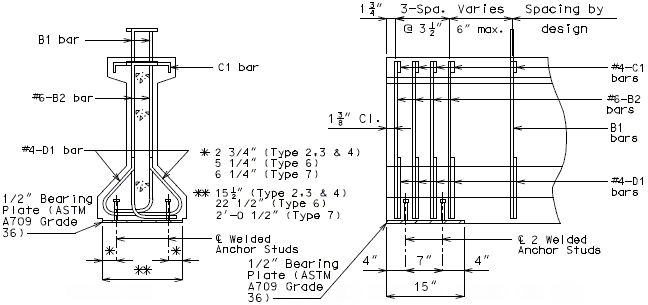
NU Standard Girder End Section Reinforcement
Typical end section reinforcement shall be all welded wire reinforcement (WWR) or all deformed bars. If additional reinforcement is required with WWR, the following options shall be considered.
Minimum spacing of reinforcing bars shall be in accordance with LRFD 5.10.3.1.2.
Consideration shall be given to spacing reinforcing bars 1” clear from welded studs on bearing plates (not shown).
Bearing Plate Anchor Studs
The standard ½" bearing plate will be anchored with four ½" x 4" studs for MoDOT shapes and eight ½” x 5” studs for NU shapes.
If required, increase the number of ½" studs and space between open B2 bars.
The minimum ¼" fillet weld between the ½" bearing plate and 1½" sole plate is adequate for all cases.
LFD Seismic Design
Studs shall be designed to meet the criteria of 2002 AASHTO 17th Edition Division I-A in Seismic Performance Category C or D.
Stud capacity is determined as follows for:
- Stud Cap. = (n)(As)(0.4Fy)(1.5)
- Where:
- N = number of studs
- As = area of stud
- Fy = yield strength of stud (50 ksi)
- 0.4Fy = Allowable Shear in Pins AASHTO Table 10.32.1A
- 1.5 = seismic overload factor
- Where:
If required, increase the number of 1/2” studs to six and space between open B2 bars or WWF. If this is still not adequate, 5/8” studs may be used. The following table may be used as a guide for upper limits of dead load reactions:
No. of Studs | Stud Dia. | Max Allowable D.L Reaction (kips) | |
---|---|---|---|
A = 0.30 | A = 0.36 | ||
4 | 1/2” | 78 | 65 |
6 | 1/2” | 117 | 98 |
4 | 5/8” | 122 | 102 |
6 | 5/8” | 184 | 153 |
8 | 1/2” | 156 | 130 |
10 | 1/2” | 195 | 163 |
8 | 5/8” | 244 | 204 |
10 | 5/8” | 306 | 255 |
751.22.3.7 Bent-up Strands
Bent-up strands for positive moment connection
Tables below show the number of bent-up strands for closed and open diaphragms (with a continuous superstructure), respectively. Provide a minimum number of bent-up strands as shown in tables at the bottom of girder ends. These bent-up strands shall be adequate to resist a positive moment over the bents.
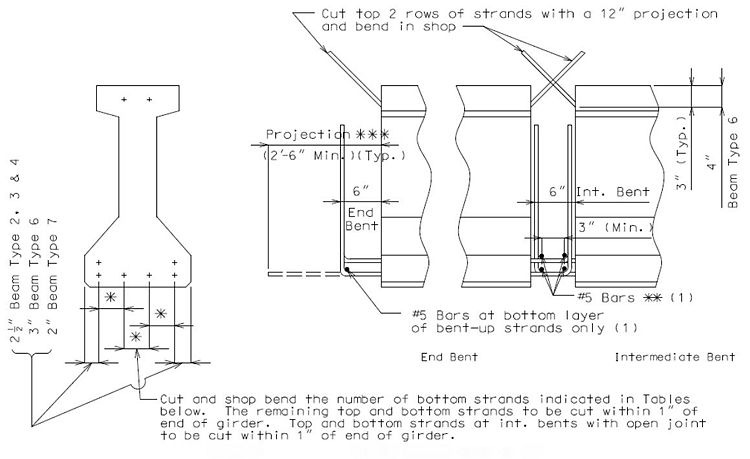
Varies
#5 bars typical at each layer of bent-up strands.
Use 3’-0” projection for NU Girders.
(1) #5-strand tie bars normal to girder.
WEB THICKNESS (INCHES) |
NUMBER OF BOTTOM STRANDS FOR POSITIVE MOMENT CONNECTION (C) | ||||
BEAM TYPE 2 | BEAM TYPE 3 | BEAM TYPE 4 | BEAM TYPE 6 | BEAM TYPE 7 (BULB-TEE) | |
6 | 6 | 6 | 8 | --- | 12 |
6-1/2 | --- | --- | --- | 10 | --- |
7(A) | 6 | 8 | 8 | --- | --- |
7-1/2(B) | --- | --- | --- | 12 | --- |
8(A) | 6 | 8 | 10 | --- | --- |
8-1/2(B) | --- | --- | --- | 12 | --- |
- (A) Modified Beam Type 2, 3 or 4.
- (B) Modified Beam Type 6.
- (C) If available. Otherwise, bend all bottom strands.
NUMBER OF BOTTOM STRANDS FOR POSITIVE MOMENT CONNECTION (C) | ||||
NU 35, 43 and 53 | 10 | |||
NU 63, 70 and 78 | 12 |
751.22.3.8 Camber, Haunching and Girder Steps
Camber
Compute theoretical camber of girder at 90 days and show on the plan as a “Theoretical camber of girder after erection (Estimated at 90 days)". Compute theoretical camber of girder at 7 days and show on the plan as a “Theoretical camber of girder after strand release (Estimated at 7 days)". Camber shall be reported to the nearest 1/8 inch.
Sample detail:
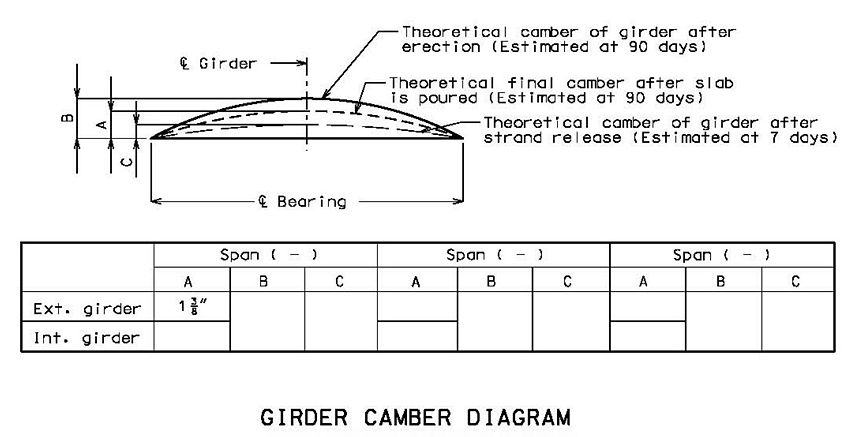
Show conversion factors for girder camber with camber diagram as per EPG 751.50 H2c6.1.
Note: The example shows Dimension A as greater than Dimension C. When Dimension A is less than Dimension C, modify detail to show this correctly keeping definitions of Dimensions A and C the same. MS Cells are given for each case.
Haunching
Haunching for a P/S I-girder bridge is the distance between the top of the girder and the bottom of the slab.
Haunching shall be computed at quarter (1/4) points for bridges with spans less than 75 feet, and at tenth (1/10) points for span 75 feet and longer. Haunching shall be reported to the nearest 1/8 inch. A typical theoretical slab haunching diagram as shown below shall be provided on all P/S I-girder bridges.
For full depth cast-in-place decks, a minimum haunch of 1 in. at the centerline of girder and 1/2 in. at the edge of the girder flange shall be provided to allow for construction tolerances and normal concrete variations. For NU and MoDOT Bulb-Tee standard girders, the minimum haunch may need to be increased. See the Structural Project Manager or Structural Liaison Engineer for full depth cast-in-place decks.
For the same reasons the following minimum haunch shall be provided for precast prestressed panel deck slabs:
- 1 1/8” for MoDOT standard girders Type 2, 3 and 4
- 1 1/4” for MoDOT standard girder Type 6
- 1 1/2” for MoDOT standard girders Type 7 and 8 (bulb-tee) and NU standard girders
A minimum of 1 in. shall be made available below the precast prestressed panels to allow for adequate flow of concrete below the panel. This is accomplished by specifying the placement of 1 in. minimum joint filler thickness under all panels.
The following maximum haunch at the centerline of the girder is allowed when prestressed panels are used:
- 2 1/2" for MoDOT standard girders Type 2, 3 and 4
- 4 1/2” for MoDOT standard girders Type 6, 7 and 8 and NU standard girders
A maximum haunch of 3 1/2 in. is allowed for all girders when only the cast-in-place option is used.
The maximum joint filler thickness to be used for supporting panels shall be 2 inches for MoDOT standard girders Type 2, 3 and 4 or 4 inches for MoDOT standard girders Type 6, 7 and 8 and NU standard girders; the remaining haunch thickness will be addressed by varying the slab thickness.
Sample detail:
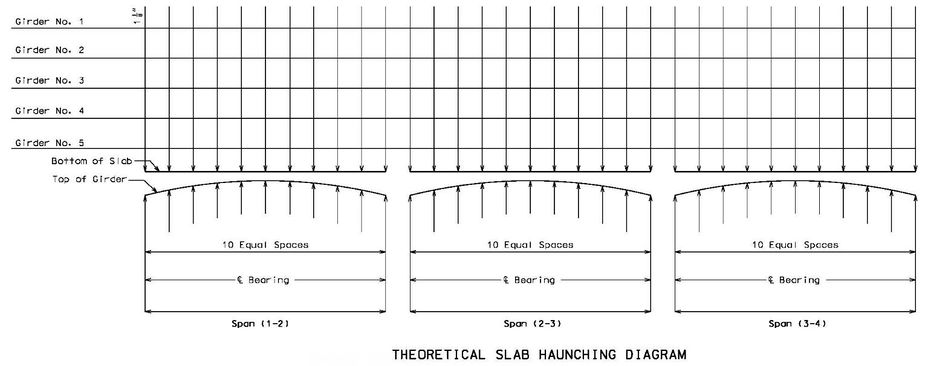
Girder Haunch Reinforcement
Hairpin reinforcement may be required in accordance with EPG 751.10.1.14 Girder and Beam Haunch Reinforcement.
Girder Steps
Steps shall be provided on prestressed girders with precast prestressed panels as shown below to keep the haunch from exceeding 2 inches for MoDOT standard girders Type 2, 3 and 4 or exceeding 4 inches for MoDOT standard girders Type 6, 7 and 8 and NU standard girders. The minimum step height shall be 1/2 inch with 1/2 inch increments with no limit of the number of steps.
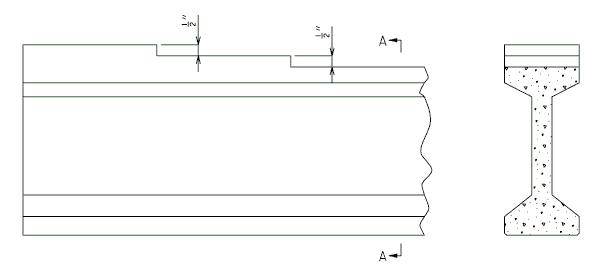
PART ELEVATION OF GIRDER | SECTION A-A |
Top of Girder
Tops of girders, for bridges with a superelevation of more than 2 percent, shall be sloped across the top flange to match the superelevation as shown below. The minimum thickness of the top flange shall be the standard flange thickness and the overall height at the minimum point shall be the standard girder height.
NU and MoDOT Bulb-Tee standard girders with top flanges exceeding a 4 percent cross-slope may experience sweep after form removal because of the unsymmetrical section and a resulting imbalanced prestressed load. It is recommended that the flange thickness be increased to only half of that required (but less than or equal to 4 percent cross-slope) and the height difference mitigated using thicker joint filler on the high side. If thicker joint filler cannot be fully used to compensate for the height difference, the extra load of a thicker slab must be accounted for in the design of the girders.
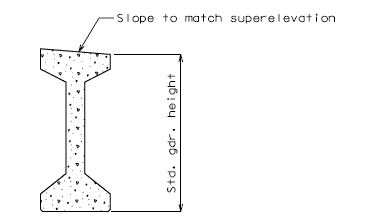
751.22.3.9 Open Intermediate Bent Diaphragms
Open diaphragms allow clearance for jacks required for future bearing rehabilitation.
751.22.3.9.1 Dimensions
for Expansion Intermediate Bent with Continuous Slab
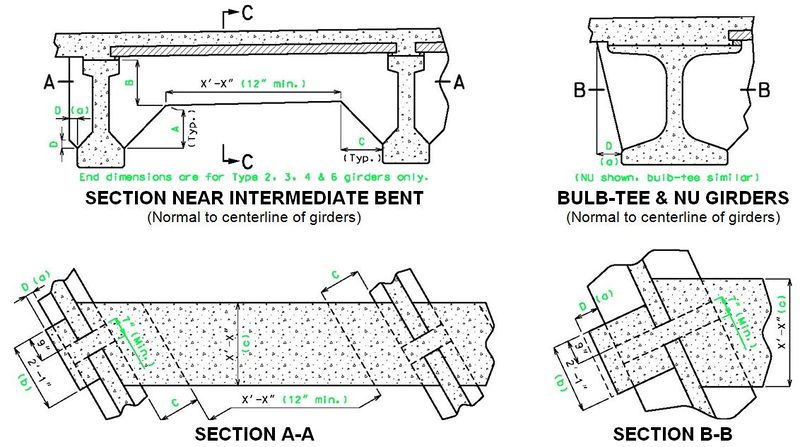
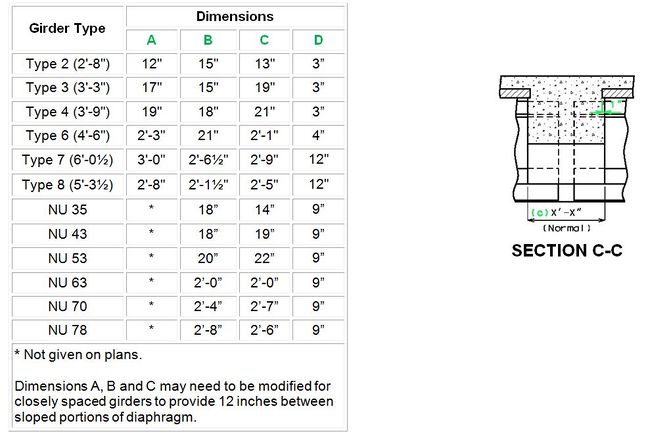
- Detailing Guidance:
- Green items are guidance only and shall not be shown on plans.
- (ɑ) Minimum distance. Will need to be increased on one side of the bent for curved alignments. Will need to add "(Min.)" to dimension in the elevation detail or replace dimension with "Varies".
- (b) Dimension based on a tangent alignment and minimum 7 inches between the ends of girders. Will vary for curved alignments.
- (c) Diaphragm shall be 2'-6" wide unless skew requires wider diaphragm to accommodate coil ties.
751.22.3.9.2 Coil Tie Rod
for Expansion Intermediate Bent with Continuous Slab
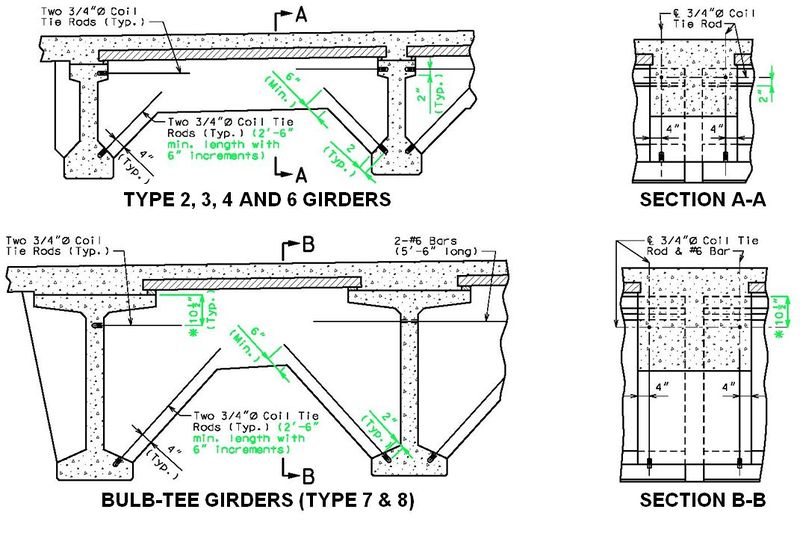
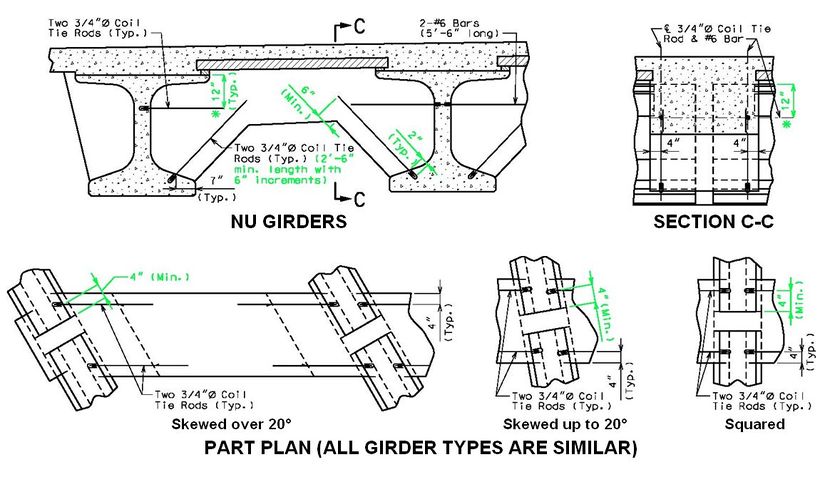
- Detailing Guidance:
- Green items are guidance only and shall not be shown on plans.
- * Adjust dimension for modified flange thickness.
751.22.3.9.3 Reinforcement Details for Type 2, 3, 4 and 6 Girders
Using Expansion Intermediate Bent with Continuous Slab
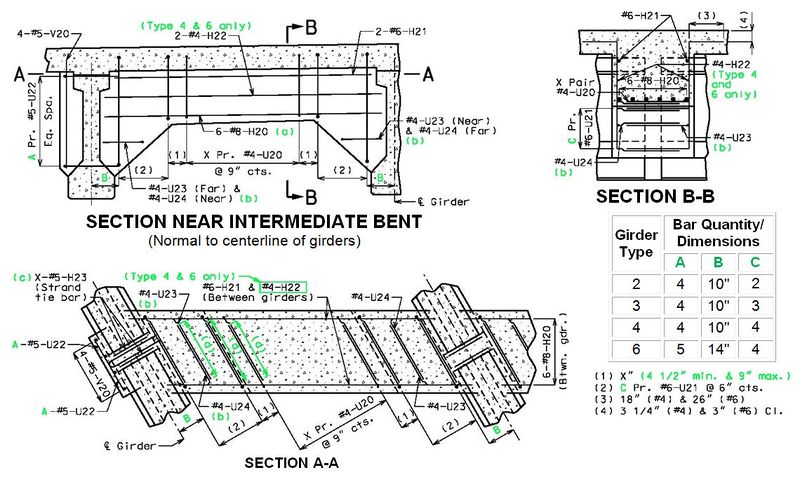
- Detailing Guidance:
- Green items are guidance only and shall not be shown on plans.
- Bar marks shown are for these details only; vary as needed.
- (ɑ) Hook ends if length of bars are less than 88” (Ld = 44”).
- (b) Replace with pair of the same bars for squared bents.
- (c) X equals layers of bent up strands.
- (d) 23" minimum for #4 bars and full available width for #6 bars.
751.22.3.9.4 Reinforcement Details for Bulb-Tee Girders (Type 7 and 8)
Using Expansion Intermediate Bent with Continuous Slab
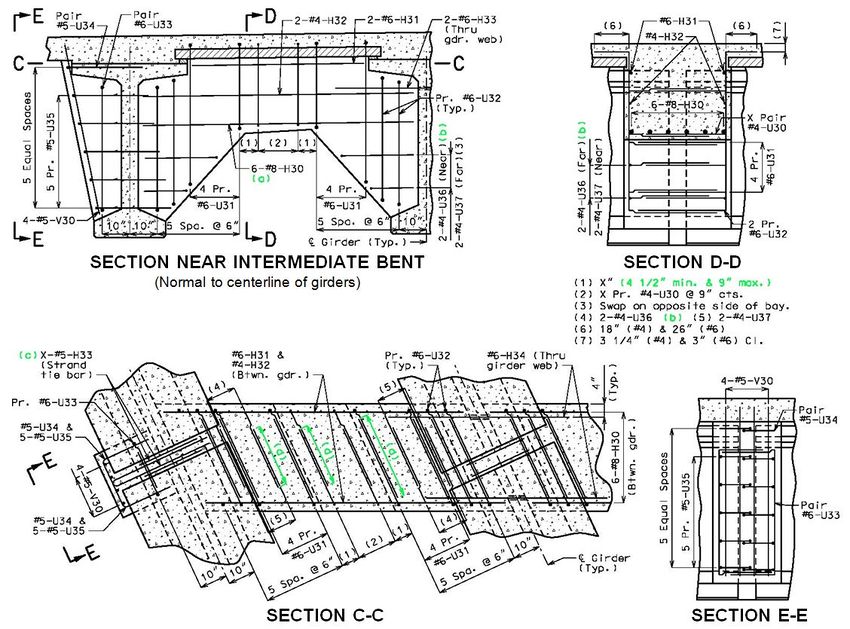
- Detailing Guidance:
- Green items are guidance only and shall not be shown on plans.
- Bar marks shown are for these details only; vary as needed.
- (ɑ) Hook ends if length of bars are less than 88” (Ld = 44”).
- (b) Replace with pairs of the same bars for squared bents.
- (c) X equals layers of bent up strands.
- (d) 23" minimum for #4 bars and full available width for #6 bars.
751.22.3.9.5 Reinforcement Details for NU Girders
Using Expansion Intermediate Bent with Continuous Slab
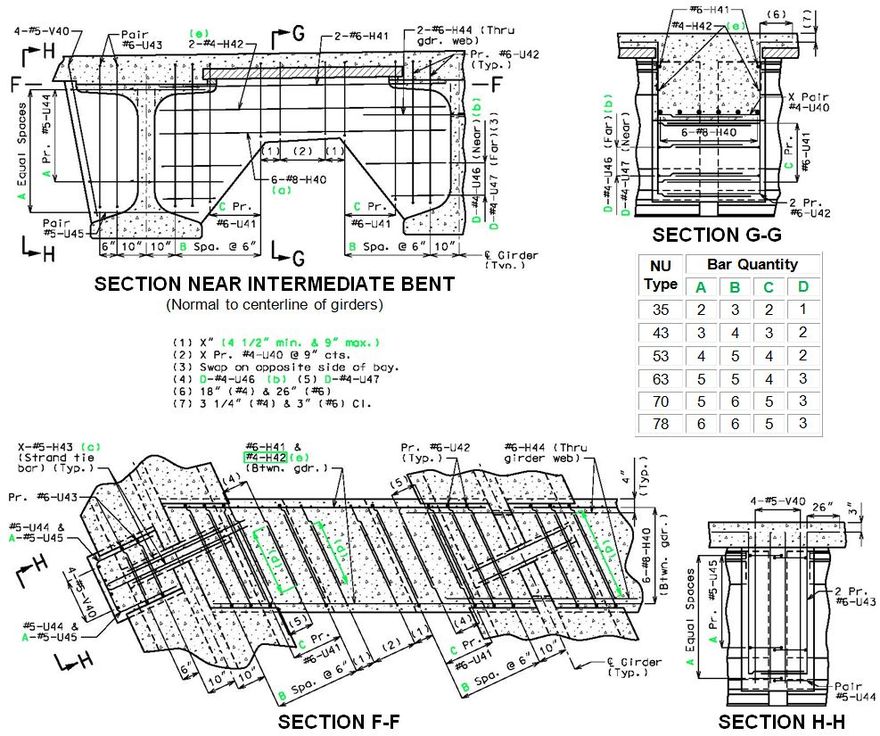
- Detailing Guidance:
- Green items are guidance only and shall not be shown on plans.
- Bar marks shown are for these details only; vary as needed.
- (ɑ) Hook ends if length of bars are less than 88” (Ld = 44”).
- (b) Replace with pairs of the same bars for squared bents.
- (c) X equals layers of bent up strands.
- (d) 23" minimum for #4 bars and full available width for #6 bars.
- (e) NU 78 requires another row of bars.
751.22.3.10 Closed Intermediate Bent Diaphragms
751.22.3.10.1 Dimensions
for Fixed or Expansion Intermediate Bents with Continuous Slab
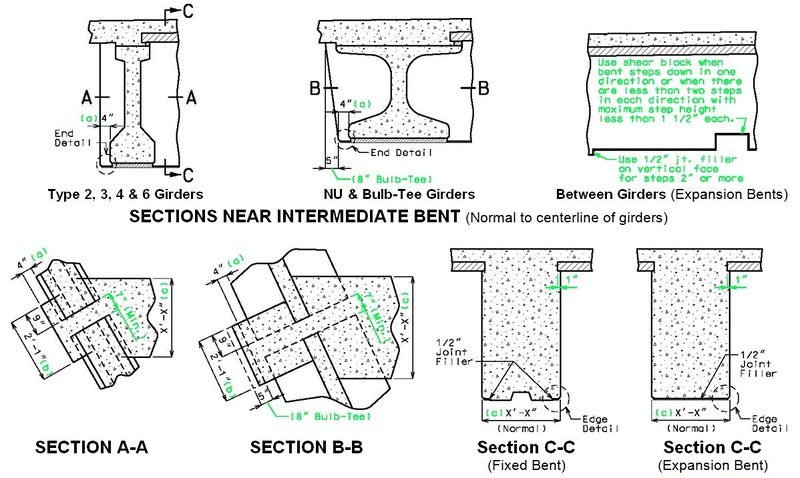
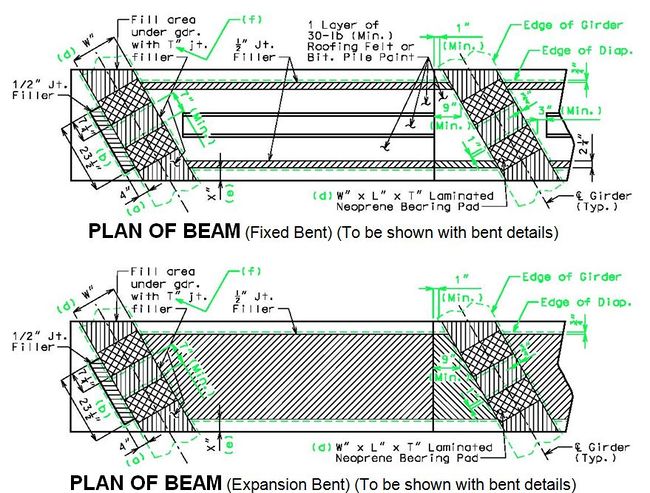
- Detailing Guidance:
- Green items are guidance only and shall not be shown on plans.
- For End Detail and Edge Detail see the end of this section.
- (ɑ) Minimum distance. Will need to be increased on one side of the bent for curved alignments. Will need to add "(Min.)" to dimension in the elevation detail or replace dimension with "Varies".
- (b) Dimension based on a tangent alignment and minimum 7 inches between the ends of girders. Will vary for curved alignments.
- (c) Diaphragm shall be 2'-6" wide unless skew requires wider diaphragm to accommodate coil ties.
- (d) "W" is width of bearing and is equal to width of bottom flange minus 1 1/2". Bearing length and thickness is by design. Bearings may vary on each side of bent.
- (e) 3 3/4" minimum. Make diaphragm flush with beams less than three feet wide.
- (f) Remove thickness for tapered bearings or when bearings vary on each side of bent.
751.22.3.10.2 Coil Tie Rod
for Fixed or Expansion Intermediate Bents with Continuous Slab
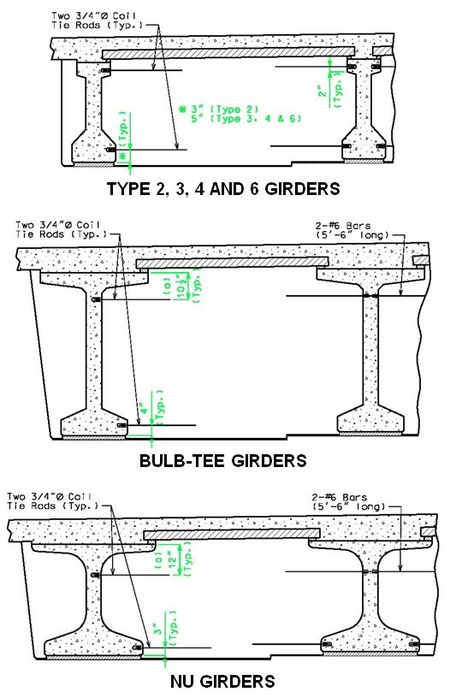

- Detailing Guidance:
- Green items are guidance only and shall not be shown on plans.
- (ɑ) Adjust dimension for modified flange thickness.
751.22.3.10.3 Reinforcement Details for Type 2, 3, 4 and 6 Girders
Using Fixed or Expansion Intermediate Bents with Continuous Slab
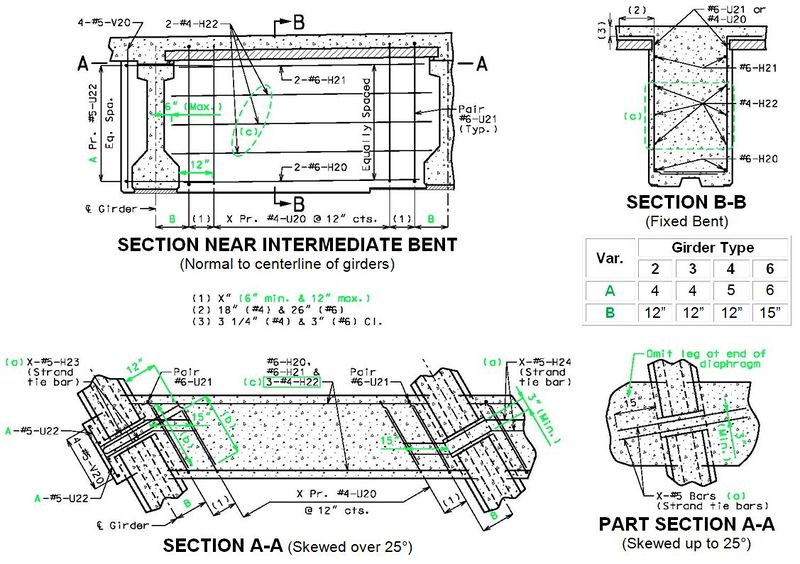
- Detailing Guidance:
- Green items are guidance only and shall not be shown on plans.
- Bar marks shown are for these details only; vary as needed.
- Bars will need to clear any required shear blocks for expansion bents.
- (ɑ) X equals layers of bent up strands.
- (b) 23" minimum for #4 bars and full available width for #6 bars.
- (c) Subtract one row for Type 2 & 3. Add one row for Type 6.
751.22.3.10.4 Reinforcement Details for Bulb-Tee Girders (Type 7 and 8)
Using Fixed or Expansion Intermediate Bents with Continuous Slab
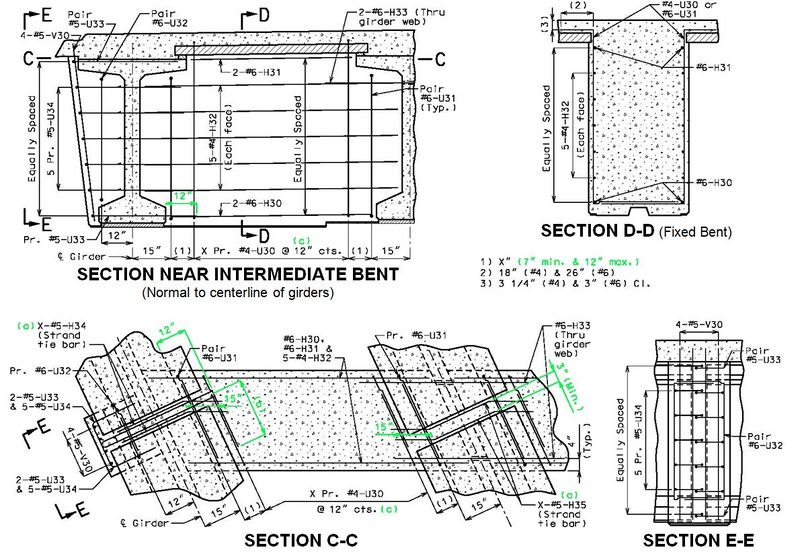
- Detailing Guidance:
- Green items are guidance only and shall not be shown on plans.
- Bar marks shown are for these details only; vary as needed.
- Bars will need to clear any required shear blocks for expansion bents.
- (ɑ) X equals layers of bent up strands.
- (b) 23" minimum for #4 bars and full available width for #6 bars.
- (c) May need to use 11" so as to make spacing work.
751.22.3.10.5 Reinforcement Details for NU Girders
Using Fixed or Expansion Intermediate Bents with Continuous Slab
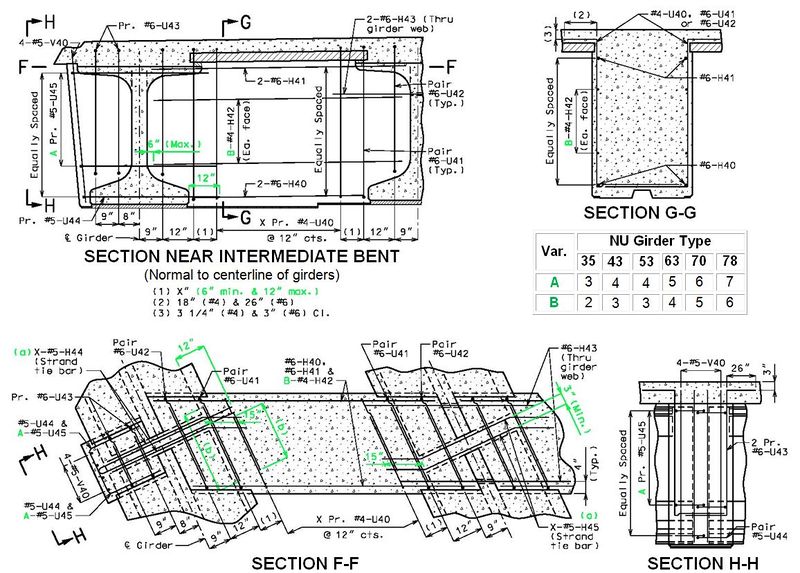
- Detailing Guidance:
- Green items are guidance only and shall not be shown on plans.
- Bar marks shown are for these details only; vary as needed.
- Bars will need to clear any required shear blocks for expansion bents.
- (ɑ) X equals layers of bent up strands.
- (b) 23" minimum for #4 bars and full available width for #6 bars.
751.22.3.10.6 Change in Girder Height at Fixed Bents
- General
Change girder heights within a continuous girder series only when specified on Design Layout or by Structural Project Manager.
Girder heights can only be changed at fixed bents for continuous series.
See EPG 751.11.3.6 Girder/Beam Chairs for additional girder chair details.
Change in Girder Height at Fixed Bents
- Reinforcement
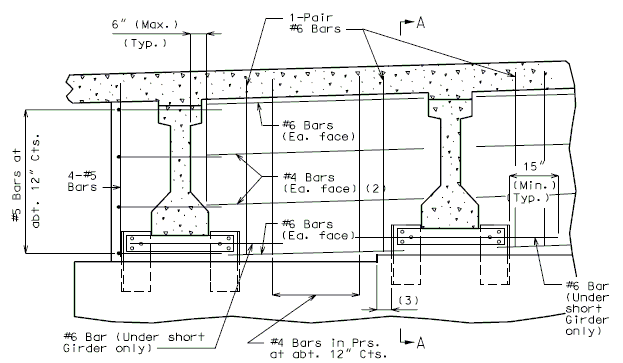
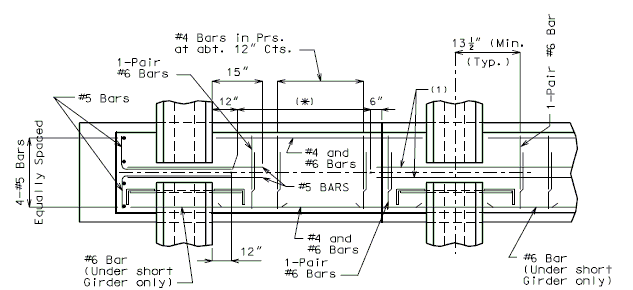
(*) By design, min. #6 dowel bars @ 12" cts. (Typ.)
(1) At each layer of bent strands. (2) For bulb-tee girders, use 3-#4 bars in each diaphragm face. (3) 3" min. when using beam step. (4) By design, min. #6 @ 12" cts. dowel bars (Typ.) |
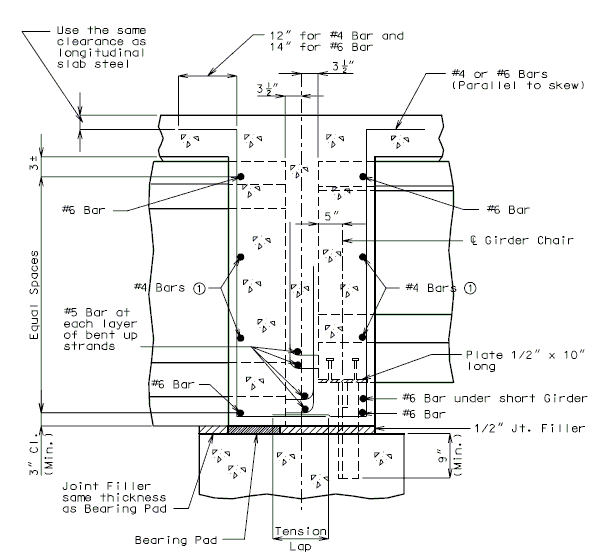
Note: Girder heights can change a maximum of one girder type.
(1) For bulb-tee girders, use 3-#4 bars in each diaphragm face. |
Change in Girder Height at Fixed Bents
- Edge Distance Details
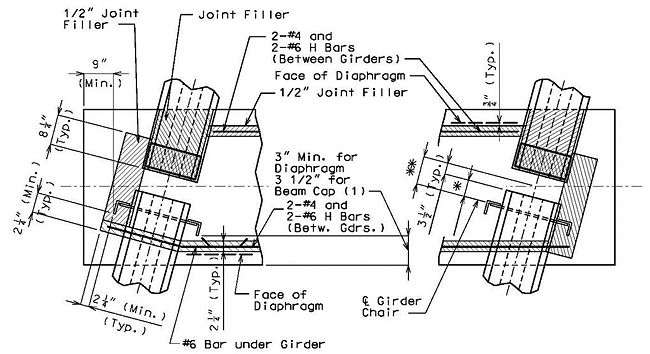
NOTE: | Field bending may be required for #4 and #6 H Bars in skewed structures near short exterior girder. |
* | 5” (Min.) for MoDOT Standard P/S Girders and 3 ½” (Min.) for NU Standard P/S Girders (Typ.) |
** | 8 ½” (Min.) for MoDOT Standard P/S Girders and 7” (Min.) for NU Standard P/S Girders (Typ.) |
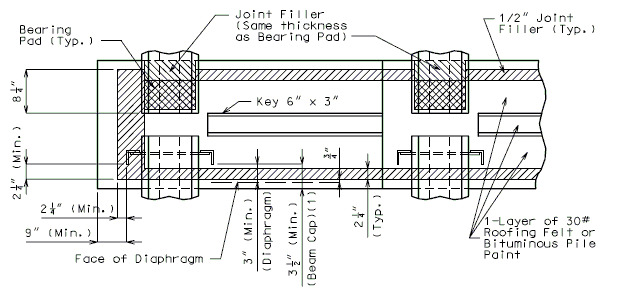
(1) When beam width is controlled by girder chair clearance, make diaphragm flush with beam cap.
751.22.3.10.7 End and Edge Detail
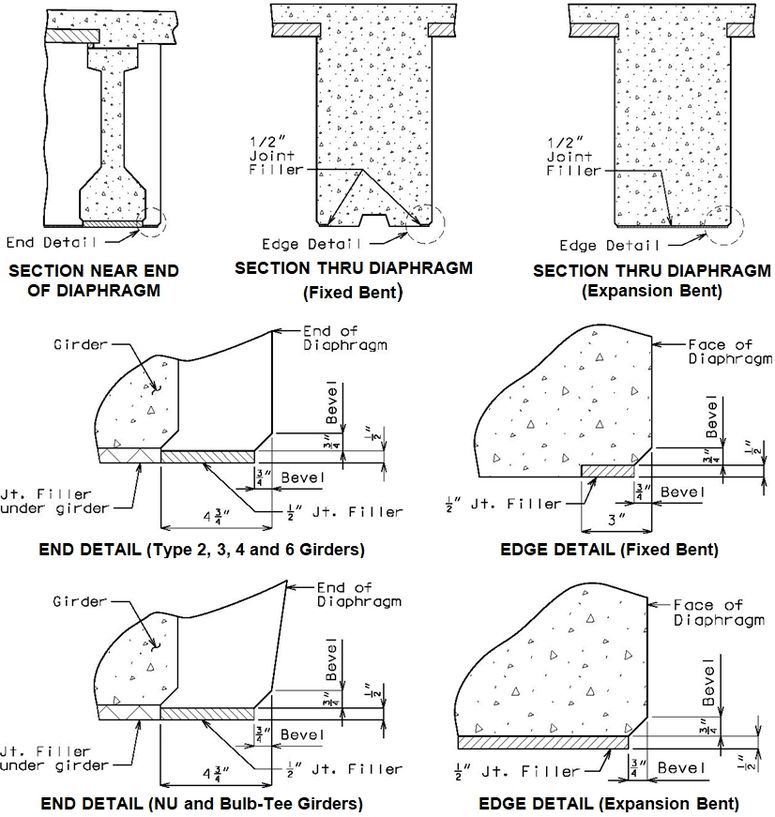
751.22.3.11 Non-integral End Bent Diaphragms
(End Diaphragm with no Expansion Devices)
Dimensions:

PART ELEVATION FOR BULB-TEE GIRDERS |
PART ELEVATION NEAR END BENT |
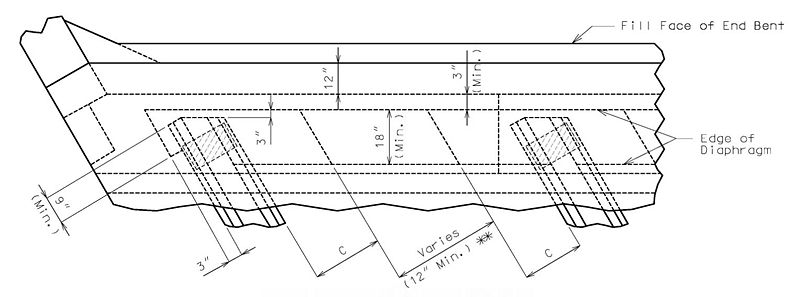
![]() PART SECTION A-A |
* A sloped diaphragm allows clearance for the future placement of jacks needed to replace bearings. ** For Bulb-Tee Girder, spacings less than 8'-8" dimensions A, B & C may have to be modified. |
|
(End Diaphragm with no Expansion Devices)
Coil Tie Rods:

NOTE: | For location of the Coil Tie Rods in a plan view, see Coil Ties. |
* 6" (Min.) shall be used for all I-Girders including Bulb-Tee and NU Girders. |
![]() |
![]() | |
EXTERIOR GIRDERS | INTERIOR GIRDERS | |
PART SECTION A-A | DETAILS OF COIL TIE RODS IN BULB-TEE GIRDERS |
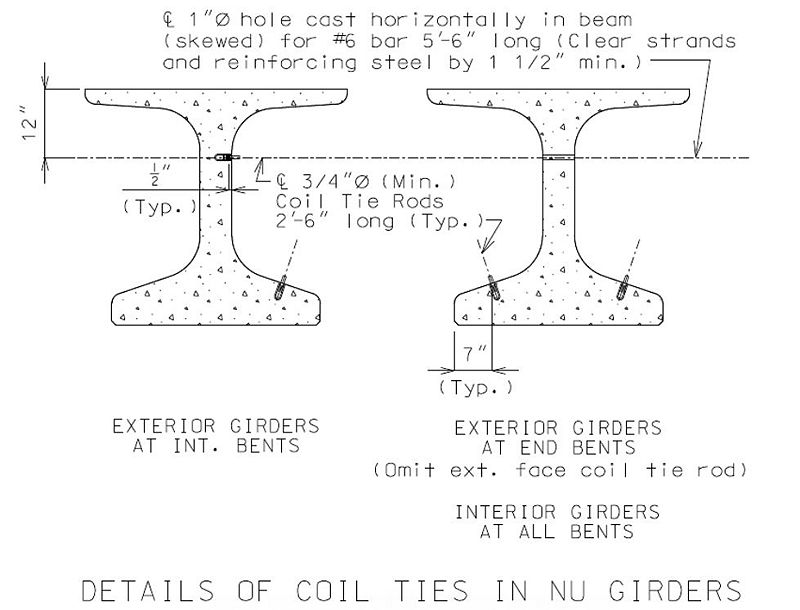
(End Diaphragm with no Expansion Devices)
Reinforcement:
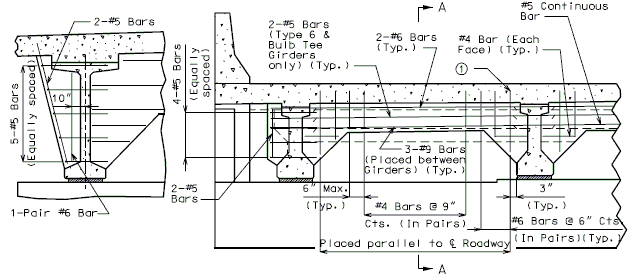
PART ELEVATION NEAR END BENT FOR BULB-TEE GIRDERS |
PART ELEVATION NEAR END BENT |
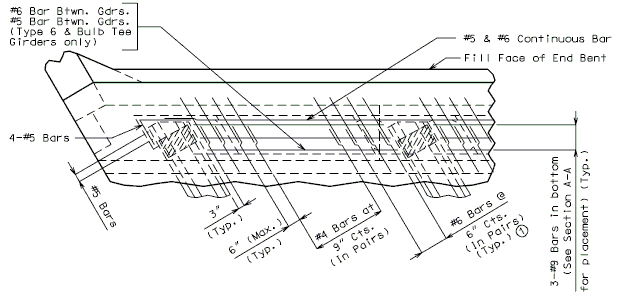
(1) For Bulb-Tee Girders, the first #6 Bar shall be placed 10" from the centerline of Web (Top Flange will prevent some Bars from extending into the Slab). | |
![]() |
|
NOTE: Bars across end of girders to be continuous. | |
(*) Use the same clearance as longitudinal slab steel. (**) Show this dimension Bridge Plan Sheets. |
- PART SECTION A-A
(End Diaphragm with Expansion Devices)
Dimensions:

PART ELEVATION FOR BULB-TEE GIRDERS |
PART ELEVATION NEAR END BENT |

![]() PART SECTION A-A |
* For Bulb-Tee Girder, spacings less than 8'-8" dimensions A, B & C may have to be modified. |
| |||||||||||||||||||||||||||||||||||||||||||||||
** A sloped diaphragm allows clearance for the future placement of jacks needed to replace bearings. | |||||||||||||||||||||||||||||||||||||||||||||||||
*** Make sure the diaphragm is wide enough to provide cover for the coil tie rods. | |||||||||||||||||||||||||||||||||||||||||||||||||
*** Not given on plans. |
(End Diaphragm with Expansion Devices)
Coil Tie Rods:

NOTE: | For location of the Coil Tie Rods in a plan view, see Coil Ties. |
* 6" (Min.) shall be used for all I-Girders including Bulb-Tee and NU Girders. |
![]() |
![]() | |
EXTERIOR GIRDERS | INTERIOR GIRDERS | |
PART SECTION A-A | DETAILS OF COIL TIE RODS IN BULB-TEE GIRDERS |
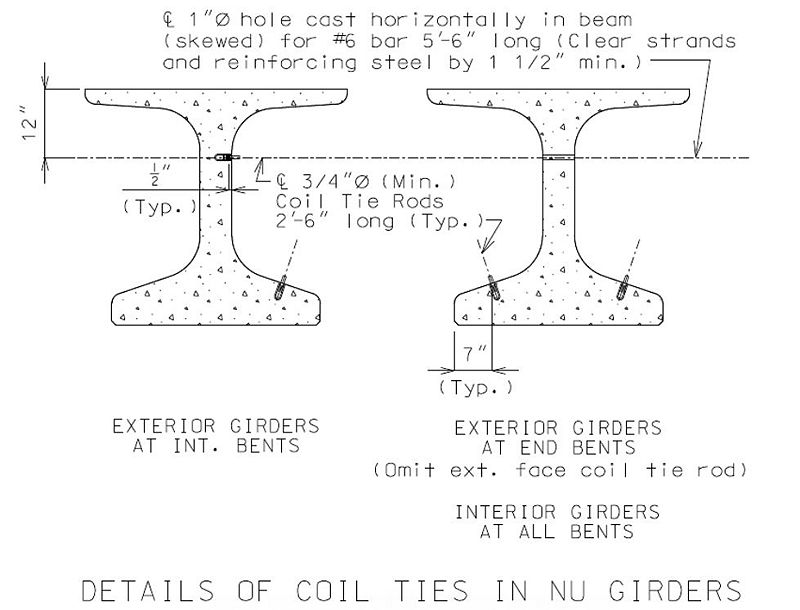
(End Diaphragm with Expansion Devices)
Reinforcement:
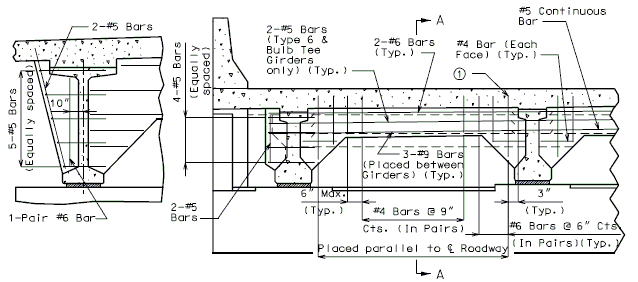
PART ELEVATION NEAR END BENT FOR BULB-TEE GIRDERS |
PART ELEVATION NEAR END BENT |
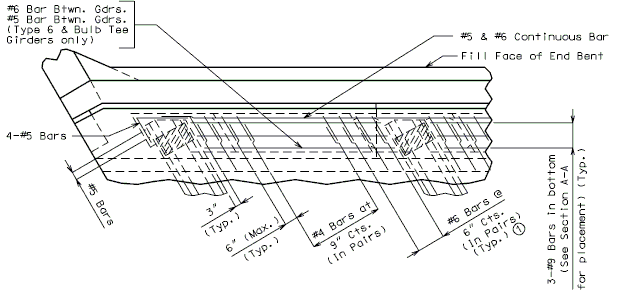
(1) For Bulb-Tee Girders, the first #6 Bar shall be placed 10" from the centerline of Web (Top Flange will prevent some Bars from extending into the Slab). | |
![]() |
|
NOTE: Epoxy Coat all Reinforcing Steel in the End of Diaphragms.
NOTE: Bars across end of girders to be continuous. | |
(*) Use the same clearance as longitudinal slab steel. (**) Show this dimension Bridge Plan Sheets. |
- PART SECTION A-A
751.22.3.12 Non-integral Intermediate Bent Diaphragms
(End Diaphragms with Expansion Device)
Dimensions:
- NOTE: Slope at top of Beam Cap and Protective
Coating to be used on Structures with Expansion
Devices.
- NOTE: Slope at top of Beam Cap and Protective
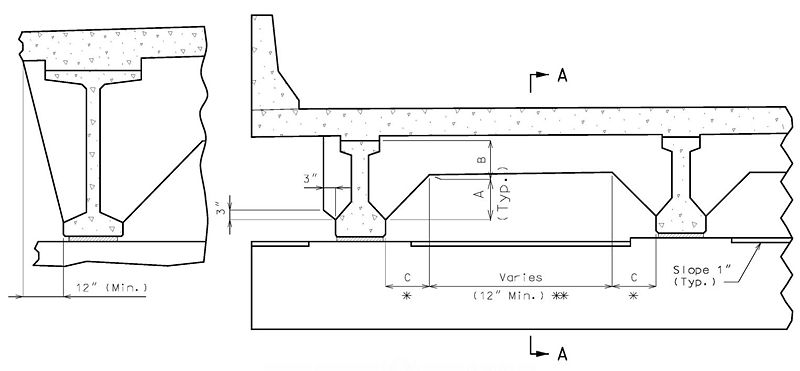
PART ELEVATION FOR BULB-TEE GIRDERS |
PART ELEVATION NEAR INT. BENT |
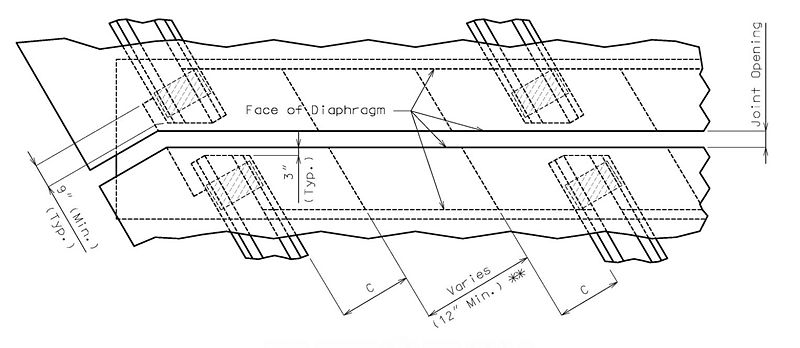
![]() PART SECTION A-A |
* A sloped diaphragm allows clearance for the future placement of jacks needed to replace bearings. |
| |||||||||||||||||||||||||||||||||||||||||||||||
** For Bulb-Tee Girder, spacings less than 8'-8" dimensions A, B & C may have to be modified. | |||||||||||||||||||||||||||||||||||||||||||||||||
*** Make sure the diaphragm is wide enough to provide enough cover for the Coil Tie Rods. | |||||||||||||||||||||||||||||||||||||||||||||||||
**** Not given on plans. |
(End Diaphragms with Expansion Device)
Coil Tie Rods:

NOTE: | For location of the Coil Tie Rods in a plan view, see Coil Ties. |
* 6" (Min.) shall be used for all I-Girders including Bulb-Tee and NU Girders. |
![]() |
![]() | |
EXTERIOR GIRDERS | INTERIOR GIRDERS | |
PART SECTION A-A | DETAILS OF COIL TIE RODS IN BULB-TEE GIRDERS |
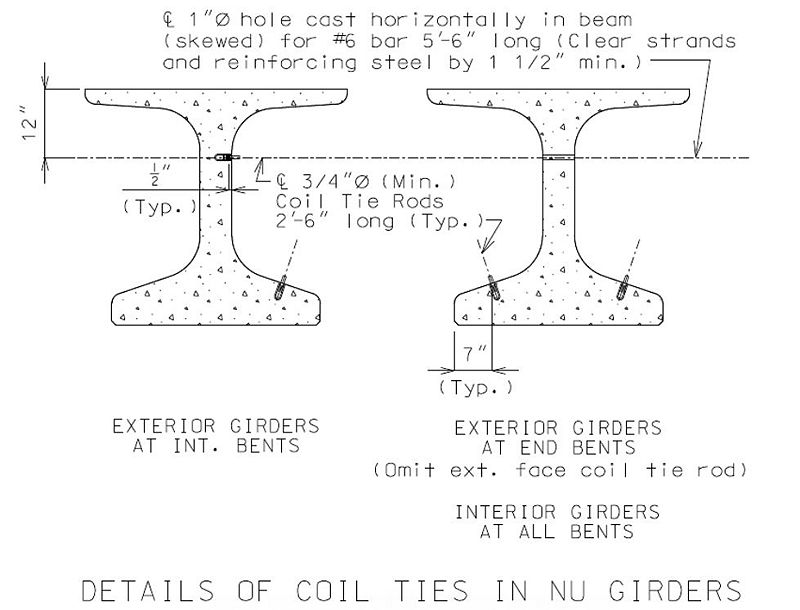
(End Diaphragms with Expansion Device)
Reinforcement:
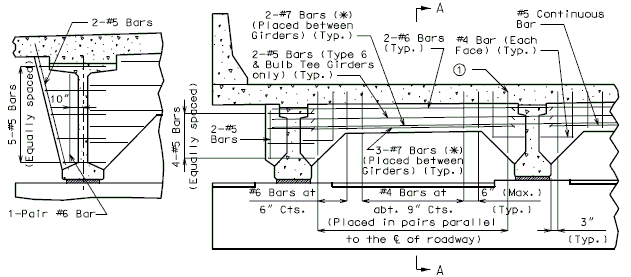
PART ELEVATION NEAR INT. BENT FOR BULB-TEE GIRDERS |
PART ELEVATION NEAR INT. BENT |
- Note: Slope at top of beam cap and protective coating to be used on structures with expansion devices.
- (1) For Bulb-Tee Girders, the first #6 Bar shall be placed 10" from the centerline of Web (Top Flange will
prevent some Bars from extending into the Slab).
- (1) For Bulb-Tee Girders, the first #6 Bar shall be placed 10" from the centerline of Web (Top Flange will
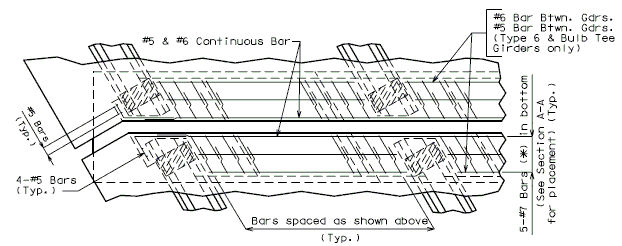
![]() |
![]() |
PART SECTION A-A | DETAIL "A" |
(*) See Detail "A" for the placement of reinforcement.
(**) Use the same clearance as longitudinal slab steel. NOTE: Epoxy coat all reinforcing steel in the end diaphragms. |
(End Diaphragm with Finger Plate Expansion Device)
Diaphragm Reinforcements:
CLOSED DIAPHRAGM:
- (NOTE: Use only when expansion device connects prestress girder series and steel girder series.)
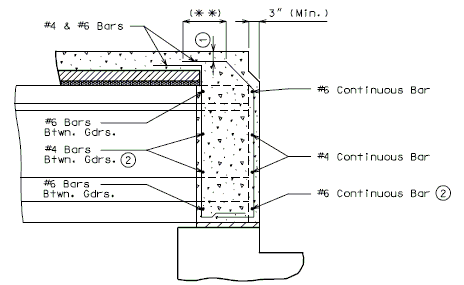
NOTE: See preceding sheets for bar spacing and detail not shown.
A protective coating shall be applied to concrete surface exposed to drainage from roadway. Indicate surface to be coated on plans. Epoxy coat all reinforcing steel in the end diaphragms. |
(2) For Bulb-Tee Girders use 3-#4 Bars in each face. |
OPEN DIAPHRAGM
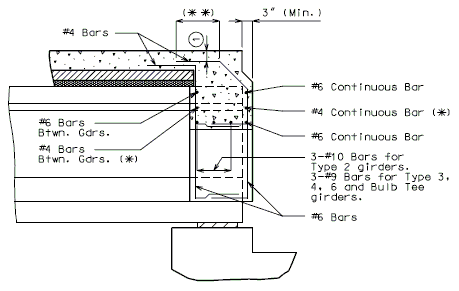
(*) | Use only on Type 6 Girder | |
(**) | 12" for #4 Bars 14" for #6 Bars (Shown on Plans) |
(1) Use the same clearance as longitudinal slab steel.
751.22.3.13 Intermediate Diaphragms
Use steel intermediate diaphragm for prestressed spans over 50 feet except for NU 35 and NU 43 girders.
Bridge Standard Drawings |
Steel Intermediate Diaphragms |
Use straight diaphragm normal to girders for skews thru 20°.
Use stepped diaphragm for skews over 20°.
Spans of 90 feet or less require one intermediate diaphragm per span.
Spans over 90 feet require two intermediate diaphragms per span.
Spans over 140 feet require three intermediate diaphragms per span.
Space diaphragms equally as allowed by clearance to harped strands.
Maximum spacing is 50 feet (from support and between diaphragms).
NU 35 and NU 43 Girders
Permanent intermediate diaphragms are not required for NU 35 and NU 43 standard girders. Temporary intermediate diaphragms/bracing are required for construction of the bridge deck. See EPG 751.50 Note H2c2.2.
751.22.3.14 Coil Ties
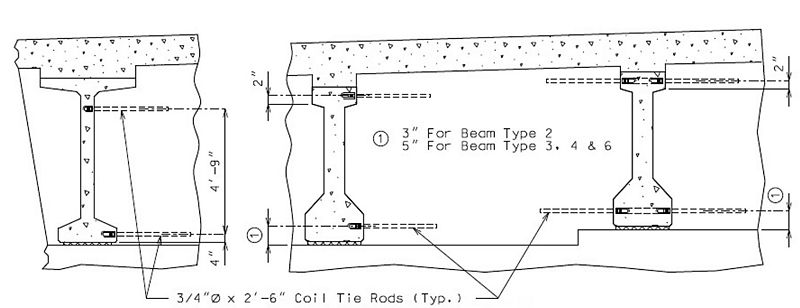
PART ELEVATION FOR BULB-TEE GIRDERS |
PART ELEVATION |
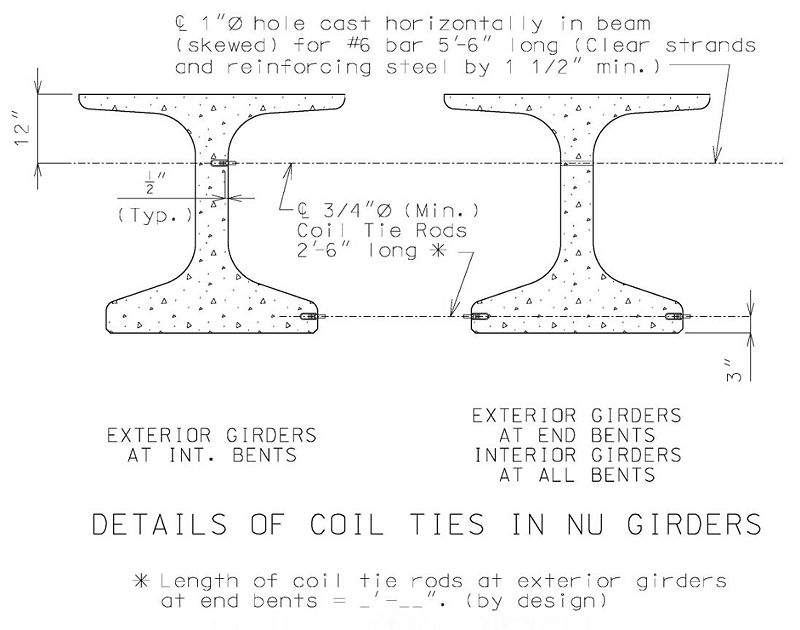
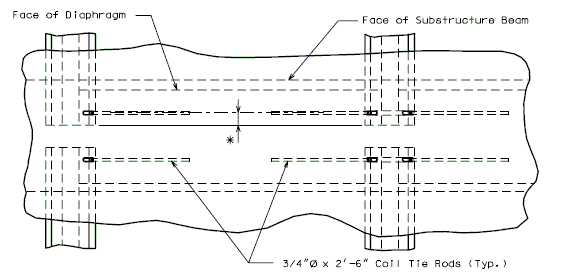
(SQUARE)
* 4" Min. (Typ.) (Do not show Dim. on Plans)
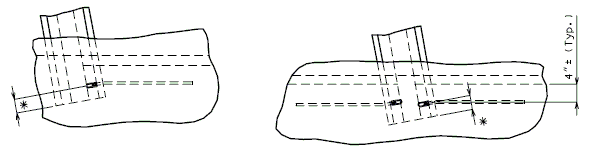
(SKEWED TO 20 DEG.)
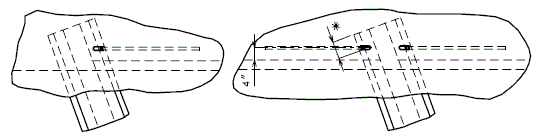
(SKEWED OVER 20 DEG.)
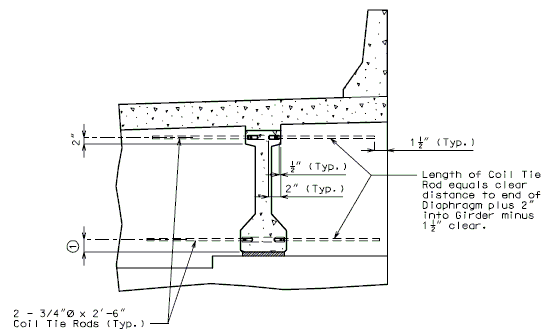
(1) | 3" For Beam Type 2 5" For Beam Type 3, 4 & 6 |
NOTE: | See previous page for location of Coil Tie Rods on Bulb-Tee girders. |
751.22.3.15 Dowel Bars
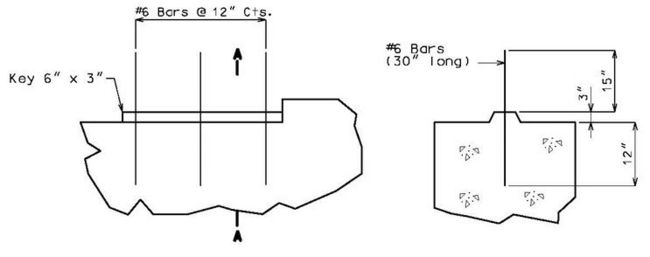
PART ELEVATION (FIXED BENT) |
SECTION A-A |
- Dowel bars shall be used for all fixed intermediate bents under prestressed superstructures. Generally, shear resistance from shear key is not considered for typical bridges in seismic performance Category A.
- Dowel bars shall be determined by design. (Minimum #6 Bars @ 12" Cts.) For shear stress, fv, computation, see EPG 751.9.3.1.2 Dowel Bars.
- fv ≤ v ● Fvn
- Where,
- v = Resistance factor
- fv = Shear stress (ksi)
- Fvn = Nominal shear resistance of dowel bar (ksi)
751.22.3.16 Vent Holes
- Note: Use vent holes on all stream crossing structures.
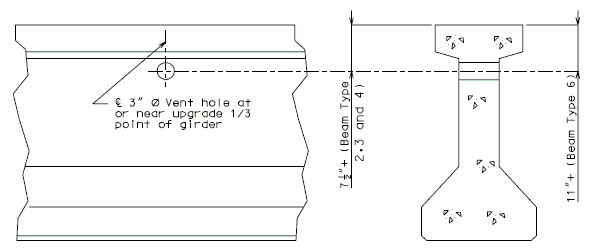
PART ELEVATION OF GIRDER | PART SECTION NEAR VENT HOLE |
- Note: Place vent holes at or near upgrade of 1/3 point of girders and clear
reinforcing steel or strands by 1-1/2" minimum and steel intermediate
diaphragms bolt connection by 6" minimum.
- Note: Place vent holes at or near upgrade of 1/3 point of girders and clear
751.22.3.17 Shear Blocks
A minimum of two Shear Blocks 12" wide x (1) high by width of diaphragm, will be detailed at effective locations on open diaphragm bent caps when adequate structural restraint cannot be provided with anchor bolts.
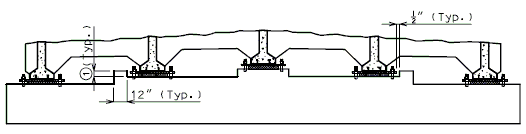
- (1) Height of shear block shall extend a minimum of 1" above the top of the sole plate.
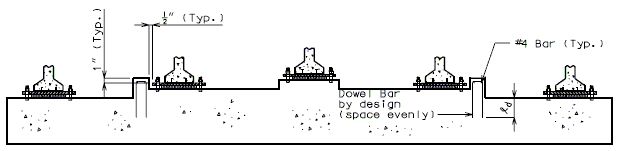
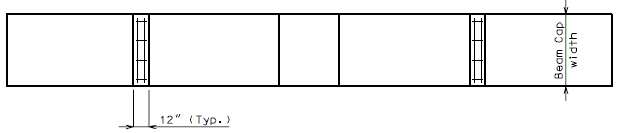
Note: Shear blocks shall be used at bents with open diaphragms when anchor bolts can not be designed to resist earthquake loading. |
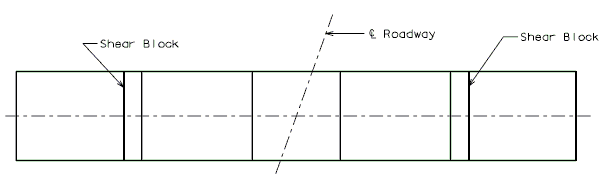
Note: For Expansion Bents with open diaphragms, the steps or Shear Block (if applicable) should be normal to the length of cap. |
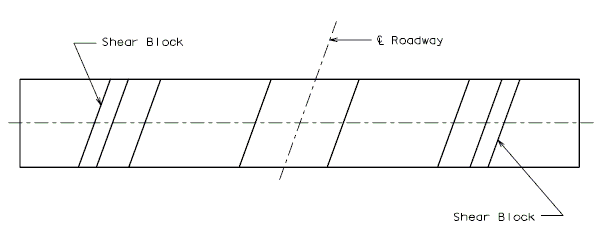
Note: For Closed Diaphragm Expansion Bents, the steps or haunches shall be detailed parallel to the centerline of roadway. For Integral End Bents the steps may be skewed due to stirrups being placed parallel to centerline of roadway. Shear Blocks for Expansion Bents with Closed Diaphragms shall be detailed parallel to the centerline of roadway. Shear Blocks used in conjunction with sole plates and anchor bolts shall be detailed parallel to the edge of sole plate. |
751.22.3.18 Miscellaneous
Dimensional Tolerances
I-Girders, Solid Slab Beams, Voided Slab Beams, Box Beams, Double-Tee Girders, Deck Panels and Miscellaneous Prestress Units, see Sec 1029
Expansion Device Support Slots
Used with preformed compression joint seal, flat plate, strip seal or finger plate expansion devices.
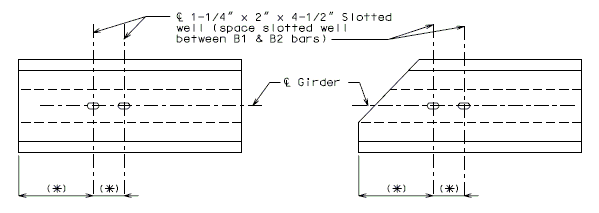
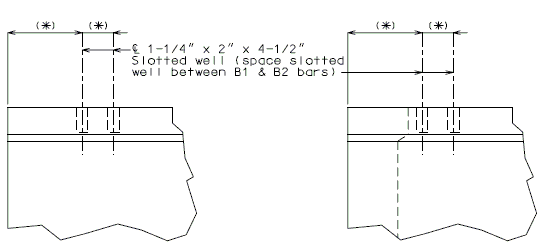
Anchor Bolts
Simple Spans

Note:
It is permissible for the reinforcing bars and or the strands to come in contact with the materials used in forming A.B. holes. If A.B. holes are formed with galvanized sheet metal, the forms may be left in place. Hole (1-1/2"ø) to be grouted with approved non-shrink grout meeting the requirements of ASTM C1107. |