751.12 Barriers, Railings, Curbs and Fences: Difference between revisions
m →751.12.5 Two Tube Rail (TL-4 [NCHRP 350]): inserted link |
m →751.12.5 Two Tube Rail (TL-4 [NCHRP 350]): minor clarification, per Bridge |
||
Line 873: | Line 873: | ||
<div id="751.12.5 Two Tube Rail"></div> | <div id="751.12.5 Two Tube Rail"></div> | ||
==751.12.5 Two Tube Rail | ==751.12.5 Two Tube Rail [[:Category:606 Guardrail and Guard Cable#Testing Criteria.|TL-4]] (NCHRP 350)== | ||
'''Guidance''' | '''Guidance''' |
Revision as of 08:47, 12 May 2014
751.12.1 Standard Safety Barrier Bridge Curbs
751.12.1.1 Standard Safety Barrier Curbs used in Missouri
![]() | |
Type A Test Level TL-4 |
Type B Test Level TL-4 |
NJ Shape | |
---|---|
![]() | |
Type C Test Level TL-5 |
Type D Test Level TL-5 |
Note: | For Type F (Temporary Barrier Curb), refer to Missouri Standard Plans 617.20. |
---|---|
For Thrie Beam Rails, see Widening & Repair information. | |
See Structural Project Manager before using Type C or D barriers. |
751.12.2 Safety Barrier Bridge Curbs (NJ Shape)
751.12.2.1 General Design
New safety barrier curbs "shall be shown to be structurally and geometrically crashworthy". Therefore, the shape of the safety barrier curb is selected based on crash-tested, or equivalent crash-tested geometry.
The safety barrier curb used on new bridges shall be the 16” New Jersey (MO) safety shape barrier curb which has been crash-tested and FHWA approved as meeting test level TL-4.
Test level TL-4 shall be used for safety barrier curb design. TL-4 is defined by AASHTO as being “generally acceptable for the majority of applications on high-speed highways, freeways, expressways, and interstate highways with a mixture of trucks and heavy vehicles”.
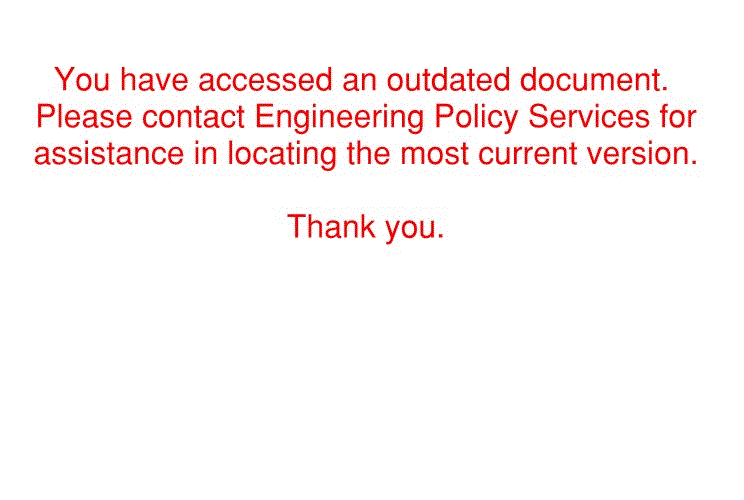
Concrete | |
---|---|
Unit weight of reinforced concrete, | = 150 |
for modulus of elasticity, | = 145 |
Safety Barrier Curbs | |
Safety Barrier Curbs shall consist of: | |
Class B-1 Concrete | = 4.0 ksi |
= 8 | |
Median Barrier Curbs | |
Median Barrier Curbs shall consist of: | |
Class B-1 Concrete | = 4.0 ksi |
= 8 | |
Reinforcing steel | |
Minimum yield strength, | = 60.0 ksi |
Steel modulus of elasticity | = 29000 ksi |
751.12.2.2 Standard Reinforcement Details
![]() |
![]() |
![]() |
R-Bar Required for Slip Form Option |
R1-Bar Shape 19 |
R2-Bar Shape 15 |
---|---|---|
R1 & R2-Bars permissible only when Slip Forming not allowed (*) | ||
![]() | ||
16" Safety Barrier Curb |
(*) The single R bar adds to the rigidity of the reinforcement during construction and it is believed to help prevent cracking. The single bar also appears to assist maintaining uniform reinforcement cover.
Note: | Use same grade reinforcing steel in Barrier Curb as in slab. Splice length for #5 bars in Barrier Curb = 35". |
Dimensions shown are also typical for structures with latex or low slump concrete (except as indicated). |
751.12.2.3 End Bent Reinforcement
![]() |
![]() | ||
End Elevation | Elevation of Barrier Curb | ||
---|---|---|---|
![]() |
![]() |
![]() | |
Section A-A | Section B-B | Section C-C | |
* | Spaced with #5-K4 bars. | ||
** | Fit bar to follow transition face of curb. |
![]() | ||||||
Elevation of Barrier Curb | ||||||
---|---|---|---|---|---|---|
![]() |
![]() |
![]() | ||||
End Elevation | Section A-A | Section B-B | ||||
![]() |
![]() |
* | Spaced with #5-K4 bars. | |||
** | Fit bar to follow transition face of curb. | |||||
Section C-C | Section D-D |
![]() |
![]() | ||
End Elevation | Elevation of Barrier Curb | ||
---|---|---|---|
![]() |
![]() |
![]() | |
Section A-A | Section B-B | Section C-C | |
* | Spaced with #5-K4 bars. | ||
** | Fit bar to follow transition face of curb. |
751.12.2.4 Slip-Form Reinforcement Details
![]() |
Section at End Bent (Optional Slip-Form Barrier) |
---|
![]() |
Section Near Joints (Optional Slip-Form Barrier) |
![]() |
Section A-A |
(*) Each side of Joint Location. |
NOTE TO DETAILER:
Optional Slip-Form Safety Barrier Curb details shall be placed on all jobs (except Prestressed Double-Tee Structures) where applicable.
Add #5 cross bracing bars for Slip-Form option. Base the length of these bars on the shortest distance between joints throughout the structure. Show the C-Bars in the Bar List and note that these bars are for the Slip-Form option only.
751.12.2.5 SBC for Wing with Detached Wing Wall
751.12.2.6 Guardrail Attachment Detail
![]() |
![]() |
Part Elevation A-A | Part Elevation |
---|---|
![]() | |
Part Plan | |
![]() | |
Auxiliary View |
751.12.2.7 Joint & Rustication Details
Curb Expansion Joints. Openings required for expansion shall be provided in the barrier curb in conjunction with deck joints. For details of expansion joints in barrier curb see expansion device details.
Curb Joints. 1/4 in. joints are located in the barrier curb at locations of negative moments to prevent cracking in the barrier curb. These joints are required when decks are continuous over intermediate bents for both continuous and simple span structures. These joints are also required at the front face of integral end bents. For details of 1/4 in. curb joints at integral end bents see integral end bent details.
Rustication. Rustication shall be used on grade separations only. Rustication shall be terminated four feet from the end of the barrier curb.
* | One space = 1/4 Span to nearest 1 in. increment (Span < 40 ft.) |
One space = 10 ft. (Span = 40 ft. to 125 ft.) | |
Two spaces = 10 ft. (Span > 125 ft.) |
Optional Slip-Form Barrier Curbs | |
---|---|
![]() | |
Section A-A | Section Thru Joint |
![]() | |
Part Section Showing Placement of Joints |
![]() |
Note: Rustication to be used on highway grade separation only. End rustication 4'-0" from end of wing. |
Part Section Showing Rustication Details |
---|
751.12.2.8 Plastic Waterstop
To eliminate water seepage problems, use a plastic waterstop, as specified, and in accordance with details shown below.
Use a plastic waterstop at all safety barrier curb joints on grade separations, except over railroads and county roads.
Use a plastic waterstop on lower safety barrier curb joint only, for structures with superelevation on grade separations.
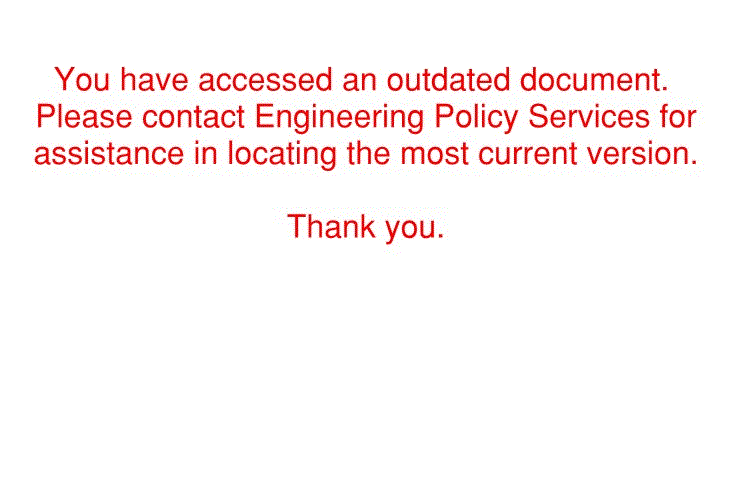
751.12.2.9 Details of Mounting Light Poles on Safety Barrier Curbs
751.12.2.10 Superelevation Details
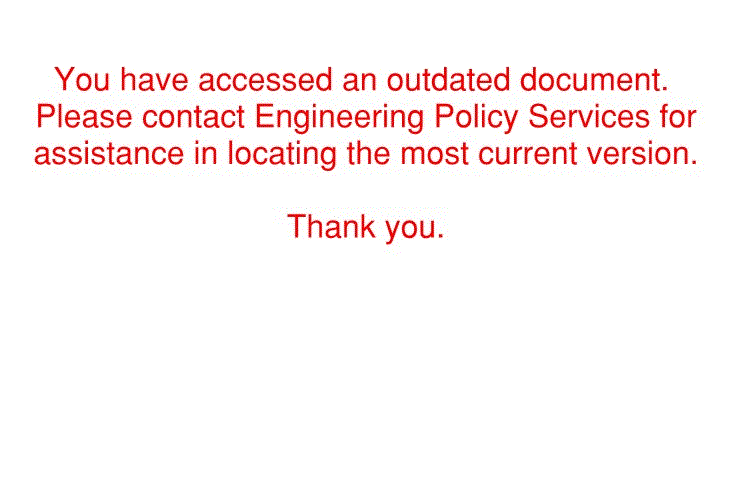
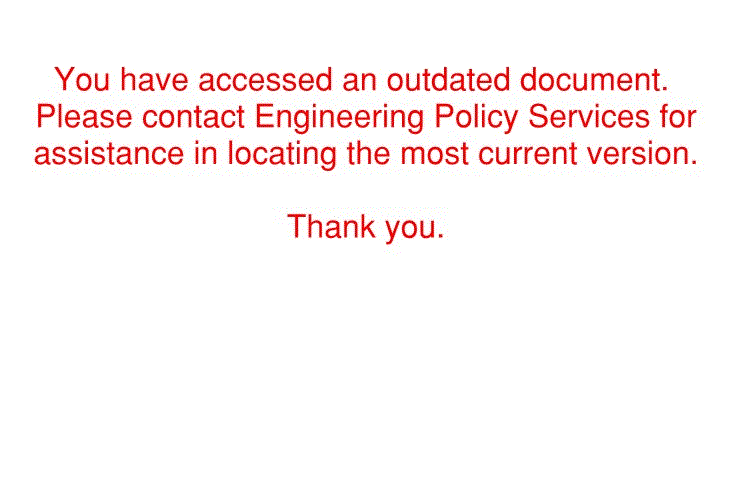
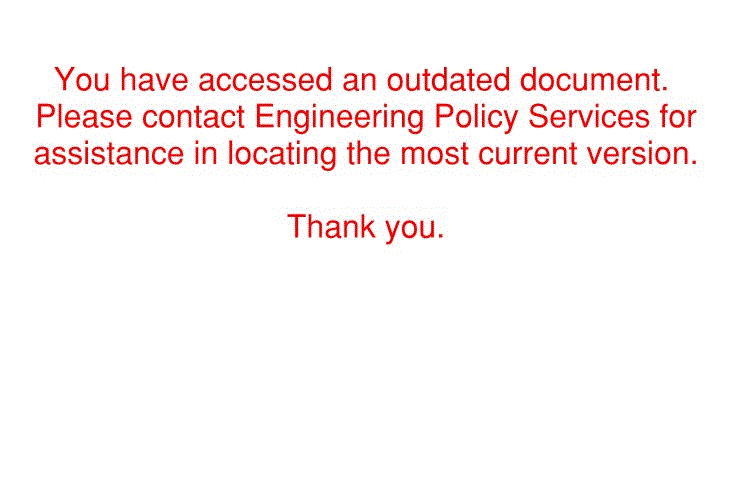
"A" | = 2'-8" + (Superelev. Slope x 16") |
"B" | = 2'-8" - (Superelev. Slope x 16") |
"C" | = 8 1/2" + (Superelev. Slope x 16") |
"D" | = 8 1/2" - (Superelev. Slope x 16") |
751.12.3 Medians
751.12.3.1 Double Faced Median Barrier Curb (NJ Shape)
Note: | Use same grade reinforcing steel in barrier curb as in slab. |
Splice length for #5-R bars in barrier curb = 35". | |
Do not use this barrier curb over precast prestressed panels. |
Note to detailer: | Provide slip-form option for double faced median safety barrier curb. For slip-form option additional #5 cross bracing bars shall be placed on both sides of all joints and R2 bars shall be one bar. |
![]() |
![]() |
R2 Bar Shape 15 |
R4 Bar Shape 27 |
---|---|
![]() | |
Section Thru Double Faced Median Barrier Curb | |
Twin Bridge Median Barrier Curb Details | |
![]() | |
Section Thru Median with Open Joint |
751.12.3.2 Concrete Median Curbs
751.12.4 Chain Link Fence
![]() | |
Superstructure Near Steps | |
---|---|
![]() | |
Superstructure at or Near End Panel | |
![]() |
Design Crieria: Fence fabric weight = 10#/lin. ft. Eff. wind area = 0.11 area/sq.ft. |
Detail "A" |
751.12.5 Two Tube Rail TL-4 (NCHRP 350)
Guidance
- Meets TL-4 (NCHRP 350)
- Typically used on spread box beam bridges.
- May be used on adjacent box beam bridges where reinforcement is embedded in the beam.
- Use only in certain applications because of cost.
- Acceptable for use when roadway width or site distance is a concern.
- Curb is intrinsic to TL rating and shall be used. Curb shall be used to prevent drainage over deck.
Bridge Standard Drawings - Two Tube Rail (DGN and PDF) | |
---|---|
Standard Drawing Guidance may not be available on<br\>Bridge Standard Drawings (PDF) due to formatting. | All Bridge Standard Drawings (DGN and PDF) |
(PDF) | |
Two Tube Rail Plan and Elevation Details – TTR1 | |
Two Tube Rail Transition Details – TTR2 | |
Two Tube Rail Details – TTR3 |