902.15 Designing a Traffic Signal: Difference between revisions
m Updated links to standard plans |
m →Table 902.15.6.2.3 Equipment -Power Requirements: updated alignment |
||
(7 intermediate revisions by 3 users not shown) | |||
Line 11: | Line 11: | ||
:* Obtain traffic counts. | :* Obtain traffic counts. | ||
:* Analyze signal warrants, if necessary . | :* Analyze signal warrants, if necessary. | ||
:* Determine the type of interconnection system to include, if needed. | :* Determine the type of interconnection system to include, if needed. | ||
Line 107: | Line 107: | ||
===902.15.1.2 Final Plans=== | ===902.15.1.2 Final Plans=== | ||
'''Guidance | '''Guidance.''' Refer to [[103.1 Bid Opening and Award Process|EPG 103.1 Bid Opening and Award Process]] for information on preparing final plans. In addition to what is shown on the preliminary plans, the following [https://www.modot.org/d-sheets "D-Sheets"] are to be included: | ||
* | * Form D-37A - Details locations and types of pull boxes, bases, posts, arms, and indications | ||
* | * Form D-37B - Conduit and cable types and quantities are charted here | ||
* | * Form D-37C - Items relating to the signal controller from the power supply, cabinet, coordination interface, detectors, and load switches are detailed. | ||
* | * Form D-37D - Schematic of the conduit and cable installations. No geometric or signal head details are shown. | ||
* Phasing sheets (D-38 series) | * Phasing sheets (D-38 series) | ||
:: | ::Form D-38 | ||
:: | ::Form D-38A | ||
:: | ::Form D-38B | ||
:: | ::Form D-38C | ||
:: | ::Form D-38D | ||
:: | ::Form D-38E | ||
==902.15.2 Location of Signals and Appurtenances== | ==902.15.2 Location of Signals and Appurtenances== | ||
Line 148: | Line 146: | ||
'''Guidance.''' Controllers are placed in non-hazardous locations and oriented so the signal controlled traffic movements can be observed while standing by the controller. | '''Guidance.''' Controllers are placed in non-hazardous locations and oriented so the signal controlled traffic movements can be observed while standing by the controller. | ||
'''Standard.''' | '''Standard.''' It is the expectation that signal controllers shall not be located in the clear zone; however, if this standard cannot be met there are countermeasures that shall be considered. The first countermeasure to be considered is placing a barrier around the controller. Central Office Design can be consulted for barrier options. The other countermeasure is a unique controller base or cabinet design. Central Office Highway Safety and Traffic can be consulted in deciding the best option for the location. | ||
[[image:902.11.7.4.jpg|right|175px|thumb|<center>'''Cabinet base'''</center>]] | [[image:902.11.7.4.jpg|right|175px|thumb|<center>'''Cabinet base'''</center>]] | ||
'''Guidance.''' [https://www.modot.org/ | '''Guidance.''' [https://www.modot.org/media/16910 Standard Plan 902.10] and [https://www.modot.org/media/16914 Standard Plan 902.30] show cabinet bases. The designer coordinates with traffic to determine the type of base to be used and indicates that information on the D-37C sheet. | ||
===902.15.2.3 Service Pole and Power Supply Assembly=== | ===902.15.2.3 Service Pole and Power Supply Assembly=== | ||
'''Standard.''' If the power source is off | '''Standard.''' If the power source is off the right of way, a service pole or pedestal for the power supply assembly shall be located 2 ft. to 4 ft. inside the right of way line as near as practical to the controller location. If the power source is on the right of way, the power supply assembly shall be located as close as possible to the power source. The placement of the power supply is compatible with adjacent design features. Power supplies shall not be installed in medians or right turn islands. Only Type 1 (pole-mounted) or Type 2 (pedestal-mounted) secondary service power supplies are used. | ||
'''Guidance.''' The Type 2 power supply is the preferred design. If the power source is distant from the controller location, a complete conduit run is provided from the power supply to the controller. | '''Guidance.''' The Type 2 power supply is the preferred design. If the power source is distant from the controller location, a complete conduit run is provided from the power supply to the controller. | ||
Line 169: | Line 167: | ||
==902.15.3 Detectors== | ==902.15.3 Detectors== | ||
'''Support.''' Detectors are devices used with actuated controllers to sense the presence of vehicles or pedestrians to | '''Support.''' Detectors are devices used with actuated controllers to sense the presence of vehicles or pedestrians to assign right of way on the basis of actual demand. Detector location is dependent upon stop line and crosswalk location, therefore, stop line and crosswalk locations are to be reviewed with district Traffic before locating detectors. | ||
There are several different types of vehicle detection technology available. Each has distinct advantages particularly suited to certain circumstances or conditions. Inductive loops have been the prevalent technology for several years, but other options such as video, microwave and radar are available. Table 902.15.3.1 outlines the strengths and weaknesses of each detector type. | There are several different types of vehicle detection technology available. Each has distinct advantages particularly suited to certain circumstances or conditions. Inductive loops have been the prevalent technology for several years, but other options such as video, microwave and radar are available. Table 902.15.3.1 outlines the strengths and weaknesses of each detector type. | ||
Line 177: | Line 175: | ||
===902.15.3.1 Optional Bidding of Traffic Signal Detectors=== | ===902.15.3.1 Optional Bidding of Traffic Signal Detectors=== | ||
'''Guidance.''' So that every effort is made to increase the competition for installation of traffic signal detectors on signal projects, contractors should be allowed to bid optional traffic signal detectors. The core team should look at signal detector options or combination of options that bring the best value to the project. While optional bidding is generally advantageous for all projects, circumstances occasionally arise that cause one signal detector type to be preferred over others or the number of alternate detectors to be bid upon for a project are limited. The core team decision, which will include the concurrence of the Design Liaison Engineer, is documented | '''Guidance.''' So that every effort is made to increase the competition for installation of traffic signal detectors on signal projects, contractors should be allowed to bid optional traffic signal detectors. The core team should look at signal detector options or combination of options that bring the best value to the project. While optional bidding is generally advantageous for all projects, circumstances occasionally arise that cause one signal detector type to be preferred over others or the number of alternate detectors to be bid upon for a project are limited. The core team decision, which will include the concurrence of the Design Liaison Engineer, is documented with a memo in eProjects. | ||
Considerations for not allowing optional bids on signal detectors or limiting the types of signal detectors to be bid upon in a given project need to be evaluated for each intersection within that project. Strengths and weaknesses for each type of signal detector are provided in the table below. Consideration should be given to initial construction cost, long-term maintenance cost and continuity. | Considerations for not allowing optional bids on signal detectors or limiting the types of signal detectors to be bid upon in a given project need to be evaluated for each intersection within that project. Strengths and weaknesses for each type of signal detector are provided in the table below. Consideration should be given to initial construction cost, long-term maintenance cost and continuity. | ||
Line 187: | Line 185: | ||
! style="background:#BEBEBE"|Type of Detector!! style="background:#BEBEBE"|Strengths!!style="background:#BEBEBE"|Weaknesses | ! style="background:#BEBEBE"|Type of Detector!! style="background:#BEBEBE"|Strengths!!style="background:#BEBEBE"|Weaknesses | ||
|- | |- | ||
| rowspan="11"| '''Inductive Loop '''|| Flexible design satisfies large variety of applications|| Installation requires pavement cut. | | rowspan="11"| '''Inductive Loop '''|| Flexible design satisfies large variety of applications.|| Installation requires pavement cut. | ||
|- | |- | ||
| Mature, well-understood technology.|| Improper installation decreases pavement life. | | Mature, well-understood technology.|| Improper installation decreases pavement life. | ||
Line 219: | Line 217: | ||
| Long service life.|| Requires installation expertise. | | Long service life.|| Requires installation expertise. | ||
|- | |- | ||
| Milling and grinding operations have no | | Milling and grinding operations have no effect. || align="center"|- | ||
|- | |- | ||
| rowspan="11"| '''Microwave '''||Typically insensitive to inclement weather at the relatively short ranges encountered in traffic management applications.|| CW Doppler sensors cannot detect stopped vehicles. | | rowspan="11"| '''Microwave '''||Typically insensitive to inclement weather at the relatively short ranges encountered in traffic management applications.|| Continuous Wave (CW) Doppler sensors cannot detect stopped vehicles. | ||
|- | |- | ||
| Direct measurement of speed.|| Requires precise positioning. | | Direct measurement of speed.|| Requires precise positioning. | ||
Line 249: | Line 247: | ||
| rowspan="2"| ''' Ultrasonic ''' || Multiple lane operation available.|| Environmental conditions such as temperature change and extreme air turbulence can affect performance. Temperature compensation is built into some models. | | rowspan="2"| ''' Ultrasonic ''' || Multiple lane operation available.|| Environmental conditions such as temperature change and extreme air turbulence can affect performance. Temperature compensation is built into some models. | ||
|- | |- | ||
| Capable of | | Capable of over-height vehicle detection.|| Large pulse repetition periods may degrade occupancy measurement on freeways with vehicles traveling at moderate to high speeds. | ||
|- | |- | ||
| rowspan="8"| '''Video Image Processor '''|| Monitors multiple lanes and multiple detection zones/lane.|| Installation and maintenance,including periodic lens cleaning, require lane closure when camera is mounted over roadway (lane closure may not be required when camera is mounted at side of roadway) | | rowspan="8"| '''Video Image Processor '''|| Monitors multiple lanes and multiple detection zones/lane.|| Installation and maintenance, including periodic lens cleaning, require lane closure when camera is mounted over roadway (lane closure may not be required when camera is mounted at side of roadway) | ||
|- | |- | ||
| Easy to add and modify detection zones.|| Performance affected by inclement weather such as fog, rain, and snow; vehicle shadows; vehicle projection into adjacent lanes; occlusion; day-tonight transition; vehicle/road contrast; and water, salt grime, icicles, and cobwebs on camera lens. | | Easy to add and modify detection zones.|| Performance affected by inclement weather such as fog, rain, and snow; vehicle shadows; vehicle projection into adjacent lanes; occlusion; day-tonight transition; vehicle/road contrast; and water, salt grime, icicles, and cobwebs on camera lens. | ||
Line 271: | Line 269: | ||
====902.15.3.1.1 Project Details==== | ====902.15.3.1.1 Project Details==== | ||
'''Guidance.''' It is likely there will be specific requirements for certain approaches in any project. Section 2.1 of the JSP, Optional Traffic Signal Detectors, should list the details for all detector locations that will not be covered by the chosen option or options. Examples include utilizing existing detection for unaffected approaches, limiting or disqualifying options for back detection, or requiring advanced options (volume, speed, occupancy, etc.) as needed. | '''Guidance.''' It is likely there will be specific requirements for certain approaches in any project. Section 2.1 of the JSP, [https://epg.modot.org/forms/JSP/JSP0709.docx Optional Traffic Signal Detectors], should list the details for all detector locations that will not be covered by the chosen option or options. Examples include utilizing existing detection for unaffected approaches, limiting or disqualifying options for back detection, or requiring advanced options (volume, speed, occupancy, etc.) as needed. | ||
====902.15.3.1.2 Plans | ====902.15.3.1.2 Plans for Projects with Optional Detection==== | ||
'''Guidance.''' Plans for all projects with optional signal detectors should contain: | '''Guidance.''' Plans for all projects with optional signal detectors should contain: | ||
Line 283: | Line 281: | ||
:* Applicable Job Special Provision (OPTIONAL TRAFFIC SIGNAL DETECTORS JSP-07-XX) should be inserted in the Job Special Provisions. | :* Applicable Job Special Provision (OPTIONAL TRAFFIC SIGNAL DETECTORS JSP-07-XX) should be inserted in the Job Special Provisions. | ||
:* Final plans will be changed to reflect the type of detector chosen. | :* Final plans will be changed to reflect the type of detector chosen. | ||
===902.15.3.2 Induction Loop Detectors=== | ===902.15.3.2 Induction Loop Detectors=== | ||
Line 353: | Line 351: | ||
===902.15.3.4 Video Detectors=== | ===902.15.3.4 Video Detectors=== | ||
'''Support.''' Video detection systems can be desirable for pavement preservation, maintenance, or safety reasons. Advantages of this system are saw cuts are not necessary in new pavement | '''Support.''' Video detection systems can be desirable for pavement preservation, maintenance, or safety reasons. Advantages of this system are saw cuts are not necessary in new pavement or where pavement is in poor condition and sawing could cause further deterioration. Detection zones can be changed to accommodate intersection geometric changes and changes in traffic flow. Troubleshooting the detector can also take place at the cabinet rather than in the roadway. Video detection can be used in locations where joint placement prohibits the use of sawed loops. Finally, video detection can have safety advantages, as work in the roadway might not be required for installation or maintenance. Video detection systems are paid for as a lump sum unit, which includes the cameras, wire, cable, mounting equipment, monitors, processor units, etc. One camera can be capable of covering more than one detection zone. When plans include retrofitting a new detection system into an existing signalized intersection, check with district Traffic to determine if the existing controller equipment is compatible with the operation of a video detection system before making that selection. | ||
===902.15.3.5 Microloop Detectors=== | ===902.15.3.5 Microloop Detectors=== | ||
Line 367: | Line 365: | ||
'''Support.''' Concrete and preformed pull boxes are shown on [https://www.modot.org/media/16912 Standard Plan 902.20] and are defined in the standard specifications. The type of pull box to be used is specified on the plans and on the D-37A sheet. | '''Support.''' Concrete and preformed pull boxes are shown on [https://www.modot.org/media/16912 Standard Plan 902.20] and are defined in the standard specifications. The type of pull box to be used is specified on the plans and on the D-37A sheet. | ||
'''Guidance.''' It is desirable to locate a pull box out of the travelway of vehicles. When a pull box is located in the travelway, auxiliary lanes or shoulders, a concrete pull box is specified. When a pull box is located outside the shoulder, behind curb or guardrail, or in non-mountable islands, a preformed pull box is specified. In impervious soil, a pull box with a concrete bottom (Type II drain) is used with a 2 in. pipe drain to an adjacent ditch, slope, or drain structure. Both concrete and preformed pull boxes can be installed with Type II drains. | '''Guidance.''' It is desirable to locate a pull box out of the travelway of vehicles. When a pull box is located in the travelway, auxiliary lanes or shoulders, a concrete pull box is specified. When a pull box is located outside the shoulder, behind curb or guardrail, or in non-mountable islands, a preformed pull box is specified. In impervious soil, a pull box with a concrete bottom (Type II drain) is used with a 2 in. pipe drain to an adjacent ditch, slope, or drain structure. Both concrete and preformed pull boxes can be installed with Type II drains. One of three types of Type II drains can be used depending on the adjacent drainage features. Type A is used where there are no adjacent drainage features. Type B is used where the pull box is adjacent to a ditch or slope. Type C is used where the pull box is adjacent to a storm sewer. The elevation of the controller must be higher than the elevation of any pull box in the conduit run. | ||
'''Standard.''' Regardless of the type of soil, if the intersection is adjacent to any ditch, slope, or drainage structure, at least one pull box in the conduit system shall have a Type II drain into the adjacent drainage feature. Pull boxes, controllers and other signal appurtenances are not installed in drainage ditches. | '''Standard.''' Regardless of the type of soil, if the intersection is adjacent to any ditch, slope, or drainage structure, at least one pull box in the conduit system shall have a Type II drain into the adjacent drainage feature. Pull boxes, controllers and other signal appurtenances are not installed in drainage ditches. | ||
Line 391: | Line 389: | ||
===902.15.5.1 Conduit Size=== | ===902.15.5.1 Conduit Size=== | ||
'''Guidance.''' Standard conduit size, except those between a loop detector and the first adjacent pull box to the loop detector, is 3 | '''Guidance.''' Standard conduit size, except those between a loop detector and the first adjacent pull box to the loop detector, is 3 inches. Except for unusual cases, it is preferable to limit the maximum conduit size to 4 inches. When more area is required than is available in this size conduit, parallel lines of conduit providing the required area are used. | ||
Conduit, used solely for loop detectors lead in, can be 1 | Conduit, used solely for loop detectors lead in, can be 1 inch. A conduit run is required for each loop detector. Conduit used solely for interconnect cable, can be 2 inches. | ||
If conduit is being installed in an existing median, use conduit in trench or pushed conduit as required. | If conduit is being installed in an existing median, use conduit in trench or pushed conduit as required. | ||
===902.15.5.2 Conduit Locations=== | ===902.15.5.2 Conduit Locations=== | ||
Line 403: | Line 401: | ||
'''Standard.''' A minimum of two 3 in. conduits are provided from the first pull box to the controller. A separate conduit containing the power supply cables is provided from the power supply assembly to the controller. | '''Standard.''' A minimum of two 3 in. conduits are provided from the first pull box to the controller. A separate conduit containing the power supply cables is provided from the power supply assembly to the controller. | ||
'''Option.''' It may run directly from the service pole to the controller without entering a pull box unless the distance from the power supply to the controller is greater than 200 | '''Option.''' It may run directly from the service pole to the controller without entering a pull box unless the distance from the power supply to the controller is greater than 200 feet. Pull boxes are provided so conduit runs are no more than 200 ft. long. | ||
'''Support.''' Conduit slopes are determined in the field by the engineer. | '''Support.''' Conduit slopes are determined in the field by the engineer. | ||
Line 557: | Line 555: | ||
|} | |} | ||
====<center>''Table 902.15.6.2.3 Equipment -Power Requirements''==== | ====<center>''Table 902.15.6.2.3 Equipment -Power Requirements''</center>==== | ||
{| border="1" class="wikitable" style="margin: 1em auto 1em auto | {| border="1" class="wikitable" style="margin: 1em auto 1em auto" | ||
|+ | |+ | ||
!style="background:#BEBEBE"| !! style="background:#BEBEBE"|ITEM!!style="background:#BEBEBE" width=90|WATTS!!style="background:#BEBEBE" width=90|AMPS | !style="background:#BEBEBE"| !! style="background:#BEBEBE"|ITEM!!style="background:#BEBEBE" width=90|WATTS!!style="background:#BEBEBE" width=90|AMPS | ||
Line 574: | Line 572: | ||
|| Cabinet Fan, Outlet and Cabinet Lamp|| 240 || align="center"|2.0 | || Cabinet Fan, Outlet and Cabinet Lamp|| 240 || align="center"|2.0 | ||
|} | |} | ||
====<center>''Table 902.15.6.2.4 Circuit Breaker Sizing''</center>==== | ====<center>''Table 902.15.6.2.4 Circuit Breaker Sizing''</center>==== | ||
Line 668: | Line 665: | ||
:I = Maximum load in amps | :I = Maximum load in amps | ||
:V = 6 volts(5% of 120V), the maximum allowed voltage drop | :V = 6 volts (5% of 120V), the maximum allowed voltage drop | ||
After the required area is computed, use Table 902.15.6.2.2 to determine the size wire to be used. If the maximum factored amperage exceeds the maximum load for that wire size as shown in Table 902.15.6.2.2, use the wire size required to carry the load. | After the required area is computed, use Table 902.15.6.2.2 to determine the size wire to be used. If the maximum factored amperage exceeds the maximum load for that wire size as shown in Table 902.15.6.2.2, use the wire size required to carry the load. | ||
==902.15.7 | ==902.15.7 Traffic Signal Installations== | ||
'''Guidance.''' | '''Guidance.''' Permanent signals are installations using steel mast arm poles or steel span wire, underground conduit and basic intersection lighting. Temporary signals are installed using wood poles. They are used for construction projects or where a project will be replacing them in the near future. Mast arm pole signal installations are preferable, but each case is decided on its own merits and the funding available. If a street is to be widened or an intersection is to be reconstructed in the near future, the temporary traffic signal installation is designed to conform to the final layout, as nearly as is practical, and if future interconnection can be predicted, the temporary traffic signal controller is equipped for this eventuality. | ||
The signals, lighting, and intersection geometrics are constructed according to current Design standards. Permanent signals are typically installed with construction projects or at locations where there are no programmed major roadway projects that would affect the signals. | |||
===902.15.7.1 Span Wire Signals=== | |||
'''Guidance.''' Span wire signals are installed with wood or steel span wire poles and overhead wiring. Temporary signals are designed as wood pole span wire signals as shown in the standard plans. A steel span wire post is recommended where guy wires for a wood pole cannot be used, especially for long spans. | |||
Span wire signals can be installed by contract, by MoDOT forces, or a combination of the two. Span wire signals are typically installed where limited right-of-way or limited space for underground conduit necessitate their use. Temporary span wire signals can be installed where there is a future construction project that will install signals or where there is no work currently programmed. If no work is programmed, it would be preferable to pursue the programming of a permanent signal installation. | |||
''' | '''Standard''' Diagonal span wire signals, excluding intersection control beacons, shall not be used. Span wire signals are to be installed with basic lighting on the signal poles (silhouette lighting) or direct reflectance lighting if raised islands are installed unless other basic lighting is in place. Off-signal, direct reflectance lighting could be needed if raised islands are present. | ||
If the | A pole on state right of way owned by other shall not be used to support span wire signals. If an adjustment of the location for a department installed pole cannot be made, the existing pole shall be moved at the expense of the owner. | ||
'''Option.''' For temporary span wire traffic signals, the power supply may be installed on one of the span wire poles if it is close to the right of way line or utility company facility. If not, a separate power supply is to be installed at the right of way line or utility company facility. If possible, the power supply is to be installed to be compatible with future construction. | |||
If the signal controller can be located to be compatible with future construction, then it may be installed on a concrete base at the permanent location. | |||
''' | ==902.15.8 Modifying Existing Traffic Signal Installations== | ||
'''Guidance.''' The preliminary layout for modifying existing traffic signal installations shows both the existing and proposed installation. The final plans show existing appurtenances to remain in place, be abandoned or removed. Existing features are shown as dashed lines and new features as solid lines. Temporary signals are investigated and considered when existing signals are to be modified. Using existing conduit during signal modifications should be carefully evaluated and new conduit should be considered. | |||
==902.15.9 Temporary Signals During Upgrades== | ==902.15.9 Temporary Signals During Upgrades== | ||
Line 760: | Line 758: | ||
==902.15.16 Job Special Provisions== | ==902.15.16 Job Special Provisions== | ||
'''Guidance.''' All Job Special Provisions (JSPs) should be reviewed by district Traffic for applicability and thoroughness. Special equipment not yet accounted for in the Standard Specification must be detailed by a JSP in order to have a bid quantity. JSPs should also be used to | '''Guidance.''' All Job Special Provisions (JSPs) should be reviewed by district Traffic for applicability and thoroughness. Special equipment not yet accounted for in the Standard Specification must be detailed by a JSP in order to have a bid quantity. JSPs should also be used to ensure MoDOT communication lines through project limits are kept intact (if required). Any other special construction methods needed to ensure a properly operating signal must be detailed by a JSP. | ||
[[Category:902 Signals|902.15]] | [[Category:902 Signals|902.15]] |
Latest revision as of 14:52, 28 May 2024
Signal Design Worksheet |
Signal Design Worksheet Examples |
902.15.1 Preparation of Plans
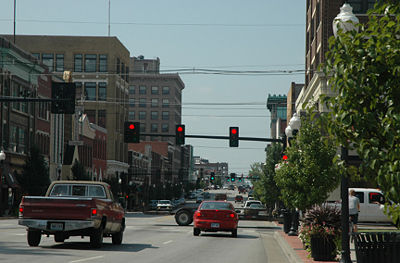
Guidance. Design should be accomplished as listed below:
- Obtain traffic counts.
- Analyze signal warrants, if necessary.
- Determine the type of interconnection system to include, if needed.
- Determine the number of signal phases and phasing sequence required to accommodate various traffic movements.
- Determine appropriate left turn phasing control and indications to use.
- Determine the signal indications, location and type mounting of each signal face.
- Determine the type and location of detectors.
- Determine the location of power supply assembly and signal controller.
- Determine the type and location of pull boxes and conduit runs.
- Determine the number and sizes of conductor cables required.
- Determine the breaker ratings for the power supply assembly and controller.
- Verify vehicle turning paths, especially regarding left turning movements and whether u-turns are allowed at the signal.
902.15.1.1 Preliminary Layout
Guidance. The first step in beginning the design is preparation of a preliminary layout. If drainage or pavement detail design plans are prepared using a scale of 1 in. = 20 ft., reproductions of these plans should be used for design of the traffic signal installation with considerable savings in work and time, provided the reproduction is made at an early design stage before details that are not pertinent to the traffic signal installation have been added to the plans.
Signal faces, posts, detectors, and pull boxes are numbered to provide a means of tabulating quantities. A suggested method of numbering is to number the posts and pull boxes first.
Standard. Signal faces and detectors are numbered to reflect the associated signal phase number (see EPG 902.5.3 Signal Phasing). Signal heads located in front of left turn auxiliary lanes are numbered to reflect a separate left turn phase even if the left turn phase is not being used. Pedestrian heads are numbered to reflect the phase they are associated with.
Guidance. The following applicable features should be shown on the preliminary layout:
- Pavement outlines, existing and proposed, with lane widths and curb types noted
- Sidewalks, crosswalks, stop lines, lane lines
- Islands, noting type (i.e. raised with 6 in. curb, mountable, flush, etc.)
- Approach grades for all approaches
- Vehicle speeds for all approaches
- Parking conditions
- Bus stops
- Entrances, utilities, drainage structures
- Location of nearby railroad or fire station
- Distance to nearest traffic signals for all approaches
- Land use, such as parking lots, service stations, etc.
- Sight-distance restrictions, including adjacent buildings
- Proposed traffic phasing and type of controller (might be shown on a D-38 sheet instead)
- Arrows showing pavement lane use
- Location of signal posts, controller, power supply, signal faces and their indications
- Type, size and locations of detectors
- Pull box locations and conduit runs
- Traffic volumes for construction and design years with peak hour
- Title block stating location
- Sign location and type
- Turning radii dimensions
- Existing signals
- Interconnection to other signals
- Right of way limits and type
- North arrow
- All streets identified
- Number signal faces, posts, detectors, and pull boxes.
Traffic should review the preliminary signal layout if the district chooses additional review. Representatives of Design and Traffic are available to furnish advice during design and plan preparation. The preliminary signal layout is approved in the district.
902.15.1.2 Final Plans
Guidance. Refer to EPG 103.1 Bid Opening and Award Process for information on preparing final plans. In addition to what is shown on the preliminary plans, the following "D-Sheets" are to be included:
- Form D-37A - Details locations and types of pull boxes, bases, posts, arms, and indications
- Form D-37B - Conduit and cable types and quantities are charted here
- Form D-37C - Items relating to the signal controller from the power supply, cabinet, coordination interface, detectors, and load switches are detailed.
- Form D-37D - Schematic of the conduit and cable installations. No geometric or signal head details are shown.
- Phasing sheets (D-38 series)
- Form D-38
- Form D-38A
- Form D-38B
- Form D-38C
- Form D-38D
- Form D-38E
902.15.2 Location of Signals and Appurtenances
902.15.2.1 Signal Post Bases
Support. Bases for mast arm signals located in islands or behind curbs are Type A. Type F (flush-mounted) bases are used beyond shoulders or sidewalk locations where the only location for the post is in a sidewalk. Type C bases are used for post top-mounted signals.
Guidance. A signal head or its bracket should not obstruct the crosswalk or sidewalk. A luminaire can be placed on a mast arm signal post to provide basic lighting without affecting the base design. Care should be taken to avoid conflicts with overhead utilities when installing lights on signal posts.
Standard. Signal post bases are not installed in medians narrower than 4 ft., face-to-face with curbs, and are preferably installed only in medians 6 ft. wide or more. Wherever practical, signal post bases are not to be located in median islands or divided highway medians. Median-located signal post bases shall have 7 ft. to 10 ft. of clearance to the median nose. All post bases shall be located a minimum 2 ft. behind curbs or 2 ft. beyond the shoulder.
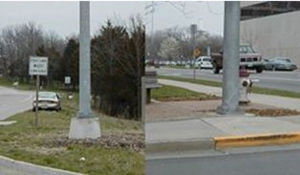
902.15.2.2 Location of Controllers
Guidance. Controllers are placed in non-hazardous locations and oriented so the signal controlled traffic movements can be observed while standing by the controller.
Standard. It is the expectation that signal controllers shall not be located in the clear zone; however, if this standard cannot be met there are countermeasures that shall be considered. The first countermeasure to be considered is placing a barrier around the controller. Central Office Design can be consulted for barrier options. The other countermeasure is a unique controller base or cabinet design. Central Office Highway Safety and Traffic can be consulted in deciding the best option for the location.
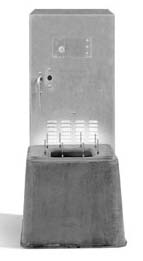
Guidance. Standard Plan 902.10 and Standard Plan 902.30 show cabinet bases. The designer coordinates with traffic to determine the type of base to be used and indicates that information on the D-37C sheet.
902.15.2.3 Service Pole and Power Supply Assembly
Standard. If the power source is off the right of way, a service pole or pedestal for the power supply assembly shall be located 2 ft. to 4 ft. inside the right of way line as near as practical to the controller location. If the power source is on the right of way, the power supply assembly shall be located as close as possible to the power source. The placement of the power supply is compatible with adjacent design features. Power supplies shall not be installed in medians or right turn islands. Only Type 1 (pole-mounted) or Type 2 (pedestal-mounted) secondary service power supplies are used.
Guidance. The Type 2 power supply is the preferred design. If the power source is distant from the controller location, a complete conduit run is provided from the power supply to the controller.
Option. For temporary traffic signal installations, it is permissible to use overhead cables between the power supply and the controller.
Standard. The location of the service pole or pedestal, and the equipment to be mounted thereon, and the furnishing of power to this assembly shall all be approved or agreed to in writing by the utility company concerned before final plans are submitted to Design. A copy of this letter shall be sent to Design with the final plans.
902.15.2.4 Signal Appurtenances on Bridges
Standard. When traffic signal appurtenances are constructed on a bridge, a detailed layout shall be submitted to Bridge and Design. The preliminary traffic signal layout is to be reviewed by Design prior to submittal of the layout to Bridge. Bridge will provide detail design of the appurtenances on or through the structure. The District's submittal to Bridge shall reflect the location and size of conduits, post bases, pull boxes, and junction boxes.
902.15.3 Detectors
Support. Detectors are devices used with actuated controllers to sense the presence of vehicles or pedestrians to assign right of way on the basis of actual demand. Detector location is dependent upon stop line and crosswalk location, therefore, stop line and crosswalk locations are to be reviewed with district Traffic before locating detectors.
There are several different types of vehicle detection technology available. Each has distinct advantages particularly suited to certain circumstances or conditions. Inductive loops have been the prevalent technology for several years, but other options such as video, microwave and radar are available. Table 902.15.3.1 outlines the strengths and weaknesses of each detector type.
The decision to select a detection system is usually at the contractors option unless certain situations exist that require a particular type.
902.15.3.1 Optional Bidding of Traffic Signal Detectors
Guidance. So that every effort is made to increase the competition for installation of traffic signal detectors on signal projects, contractors should be allowed to bid optional traffic signal detectors. The core team should look at signal detector options or combination of options that bring the best value to the project. While optional bidding is generally advantageous for all projects, circumstances occasionally arise that cause one signal detector type to be preferred over others or the number of alternate detectors to be bid upon for a project are limited. The core team decision, which will include the concurrence of the Design Liaison Engineer, is documented with a memo in eProjects.
Considerations for not allowing optional bids on signal detectors or limiting the types of signal detectors to be bid upon in a given project need to be evaluated for each intersection within that project. Strengths and weaknesses for each type of signal detector are provided in the table below. Consideration should be given to initial construction cost, long-term maintenance cost and continuity.
Table 902.15.3.1 Strengths and Weaknesses of Signal Detectors
Type of Detector | Strengths | Weaknesses |
---|---|---|
Inductive Loop | Flexible design satisfies large variety of applications. | Installation requires pavement cut. |
Mature, well-understood technology. | Improper installation decreases pavement life. | |
Large experience base. Provides basic traffic parameters (e.g., volume, presence, occupancy, speed, headway and gap). | Installation and maintenance require lane closure. | |
Insensitive to inclement weather such as rain, fog and snow. | Wire loops subject to stresses of traffic and temperature. | |
Provides best accuracy for count data as compared with other commonly used techniques. | Multiple detectors usually required to monitor a location. | |
Common standard for obtaining accurate occupancy measurements. | Detection accuracy may decrease when design requires detection of a large variety of vehicle classes. | |
High frequency excitation models provide classification data. | Requires new installation when changing geometrics. | |
Low initial cost. | Milling and grinding operations damage installation. | |
Easy set-up and installation. | Remote monitoring unavailable. | |
Very reliable. | - | |
Large detection area. | - | |
Microloop | Can be used where loops are not feasible (e.g., bridge decks, poor pavement condition). | Installation requires pavement cut or tunneling under roadway. |
Some models are installed under roadway without need for pavement cuts. However, boring under roadway is required. | Cannot detect stopped vehicles unless special sensor layouts and signal processing software are used. | |
Insensitive to inclement weather such as snow, rain and fog. | Small detection area. | |
Less susceptible than loops to stresses of traffic. | Requires extensive training. | |
Long service life. | Requires installation expertise. | |
Milling and grinding operations have no effect. | - | |
Microwave | Typically insensitive to inclement weather at the relatively short ranges encountered in traffic management applications. | Continuous Wave (CW) Doppler sensors cannot detect stopped vehicles. |
Direct measurement of speed. | Requires precise positioning. | |
Multiple lane operation available. | Detects only similar movements. | |
Milling and grinding operations have no effect. | Multiple units needed to detect several movements. | |
May not require traffic control to install. | - | |
Cost less than a microloop. | - | |
Best suited for short-term installations. | - | |
Best for reusability. | - | |
Reliable and accurate. | - | |
Large detection area. | - | |
Good for advance detections zones (dilemma zone detection). | - | |
Radar | Transmits multiple beams for accurate measurement of vehicle position, speed and class. | Operation may be affected by fog when visibility is less than 20 ft. or blowing snow is present. |
Multiple lane operation available. | Installation and maintenance, including periodic lens cleaning, require lane closure. | |
Ultrasonic | Multiple lane operation available. | Environmental conditions such as temperature change and extreme air turbulence can affect performance. Temperature compensation is built into some models. |
Capable of over-height vehicle detection. | Large pulse repetition periods may degrade occupancy measurement on freeways with vehicles traveling at moderate to high speeds. | |
Video Image Processor | Monitors multiple lanes and multiple detection zones/lane. | Installation and maintenance, including periodic lens cleaning, require lane closure when camera is mounted over roadway (lane closure may not be required when camera is mounted at side of roadway) |
Easy to add and modify detection zones. | Performance affected by inclement weather such as fog, rain, and snow; vehicle shadows; vehicle projection into adjacent lanes; occlusion; day-tonight transition; vehicle/road contrast; and water, salt grime, icicles, and cobwebs on camera lens. | |
Rich array of data available. | Requires 50- to 70-ft. camera mounting height (in a side-mounting configuration) for optimum presence detection and speed measurement. | |
Provides wide detection area when information gathered at one camera location can be linked to another. | Some models susceptible to camera motion caused by strong winds or vibration of camera mounting structure. | |
Good for poor pavement conditions and bridge decks. | Generally cost-effective when many detection zones within the camera field-of-view or specialized data are required. | |
May not require traffic control to install or maintain. | - | |
Remote viewing, configuration and monitoring available. | - | |
Milling and grinding operations have no affect. | - |
902.15.3.1.1 Project Details
Guidance. It is likely there will be specific requirements for certain approaches in any project. Section 2.1 of the JSP, Optional Traffic Signal Detectors, should list the details for all detector locations that will not be covered by the chosen option or options. Examples include utilizing existing detection for unaffected approaches, limiting or disqualifying options for back detection, or requiring advanced options (volume, speed, occupancy, etc.) as needed.
902.15.3.1.2 Plans for Projects with Optional Detection
Guidance. Plans for all projects with optional signal detectors should contain:
- Typical layout showing location of all detection zones desired.
- All pay items for signal detectors should be per each.
- Applicable Job Special Provision (OPTIONAL TRAFFIC SIGNAL DETECTORS JSP-07-XX) should be inserted in the Job Special Provisions.
- Final plans will be changed to reflect the type of detector chosen.
902.15.3.2 Induction Loop Detectors
Support. This detector can be used for single and multiple lane detection. Operative speed is 0 to 80 mph and detection is non-directional. The zone of influence can be reduced so actuation will not occur unless the loop is driven upon. This actuation can be presence as well as motion. The cost of this type detector is dependent on the number and size of loops.
Each loop consists of two or more turns of #14 AWG (2.5 mm2) stranded wire placed in sawed slots in the existing pavement, or in the "B" or "C" course of asphaltic resurfacing. Separate conduits for each detector's lead wire to the pull box must be provided to facilitate individual loop replacement. The loop wires are spliced to a shielded #14 AWG (2.5 mm2) lead-in cable in the pull box. The lead-in cable is continuous to the controller cabinet.
Standard loop dimensions are 6 ft. x 30 ft. for stop line detection. Advance loop detectors on high speed approaches, closed loop system detectors, or speed detectors are 6 ft. x 6 feet.
Standard Plan 902.50 shows detector configurations. The dimensions of loops are shown on the plans. Typical layouts for microloop detectors are available.
Option. Where conditions such as the location of a bridge end do not allow 30 ft. for the location of a stop line loop detector, a shorter detector may be used.
Standard. In this case additional detection with a second loop detector or another type of detector is to be installed to provide a 30 ft. minimum detection zone.
Guidance. Each loop or detection zone will require a sensor unit that is housed in the controller cabinet. Sensor units (amplifiers or detectors) with 2-channel card-rack mounted versions will be used. Each 2-channel unit is capable of handling two loops or detection zones. The loop or detection zone associated with each phase is to be shown on the detector schedule on the D-37C sheet. Each loop is assigned a card position and channel on the D-37 sheet. Detection zones are not assigned a card position or channel. Suggested assignments are as follows:
Channel Number | Card Position | |||||||
---|---|---|---|---|---|---|---|---|
1 | 2 | 3 | 4 | 5 | 6 | 7 | 8 | |
1 | Phase 1 | 1 or 6 | 6 | 6 | 3 | 3 or 8 | 8 | 8 |
2 | Phase 5 | 5 or 2 | 2 | 2 | 7 | 7 or 4 | 4 | 4 |
The quantity of 2-channel detectors is indicated below the assignment chart. Even if only one channel of the two-channel card detector is used, the entire unit is counted as a card detector and is paid for as such. The maximum number of card detectors is 8.
902.15.3.2.1 Location of Detectors
Support. Location of detectors is critical with respect to the efficient operation of actuated control; therefore, their location is carefully designed.
Standard. Loop detectors are not to be located in "E" joints, bridge expansion joints or other full depth joints.
902.15.3.2.2 Detectors for Left Turn Lanes
Guidance. These detectors should be placed as close to the stop line as practical, as this is a relatively slow movement. This location allows a minimum green time and thereby provides the most efficient operation.
902.15.3.2.3 Detectors for Through Traffic
Support. Loop detectors, 30 ft. long, located at the stop line in each lane, are normally used to detect through traffic. Full traveled pavement detector coverage is essential for efficient operation.
Guidance. Detectors are placed so no more than a 6 ft. gap in coverage is allowed across the traveled pavement. When a physical barrier is not provided between opposing flows of traffic, the field of detector actuation is to come no closer than 3 ft. to the centerline.
Advance Detectors
Guidance. On approaches with operating speeds of 45 mph or greater, advance detection is to be considered to allow adequate time for a vehicle to pass through the intersection with a green signal indication. An advance detector is located at a distance back from the stop bar determined by the Driver Reaction to Yellow chart. This range of distance from the stop line within which drivers are often indecisive is known as the dilemma zone. To provide dilemma zone protection on high speed approaches, the detector should be placed at least five seconds travel time from the stop line.
Refer to EPG 902.5.37.3 Detection on High-Speed Approaches for additional information.
902.15.3.3 Time Delay Unit
Support. This type of detector amplifier is used with vehicle detectors to delay the input signal from the detector to the controller. This will help prevent "false calls" into the controller which may cause the controller to service a phase where there is no vehicle waiting. Time delay functions are also available within newer signal controller firmware.
Guidance. If controller based time delay functions are not available time delay detectors should be considered for any of the following conditions:
- Exclusive right turn lanes where right turns are permitted on red.
- Exclusive left turn lanes where there is no adjacent divisional median island.
- Exclusive left turn lanes where protected-permissive left turn phasing (with a five-section signal head) is used.
Time delay detectors can be used in other situations as needed. Refer to EPG 902.5.37 Detector Settings for additional information.
902.15.3.4 Video Detectors
Support. Video detection systems can be desirable for pavement preservation, maintenance, or safety reasons. Advantages of this system are saw cuts are not necessary in new pavement or where pavement is in poor condition and sawing could cause further deterioration. Detection zones can be changed to accommodate intersection geometric changes and changes in traffic flow. Troubleshooting the detector can also take place at the cabinet rather than in the roadway. Video detection can be used in locations where joint placement prohibits the use of sawed loops. Finally, video detection can have safety advantages, as work in the roadway might not be required for installation or maintenance. Video detection systems are paid for as a lump sum unit, which includes the cameras, wire, cable, mounting equipment, monitors, processor units, etc. One camera can be capable of covering more than one detection zone. When plans include retrofitting a new detection system into an existing signalized intersection, check with district Traffic to determine if the existing controller equipment is compatible with the operation of a video detection system before making that selection.
902.15.3.5 Microloop Detectors
Support. Microloop detectors can be used at locations where it is undesirable to saw loops in the pavement, such as bridge decks. Typically, 5 probes are used for stop bar detection. Advance detection can be accomplished with as few as1 probe per lane. Where the end of a bridge divides the detection area, a combination of microloop detectors and an induction loop detector can be used. Typically 2 or 3 probes and a short quadrapole detector are used for this configuration. Guidance for typical layouts for microloop detectors is available. Microloops have a narrow range of detection, so standard practice is to stagger them 2 ft. from the centerline of the lane. When possible, probes are not to be installed over traffic on overpass bridges.
Microloops require special lead-in cables that are continuous from the probes to the controller and are provided with the probes. The quantity of lead-in cable is itemized separately on the D-37 sheet. The total quantity is included in the pay item for loop detector lead-in cable.
Special detection equipment is required for these probes in the controller cabinet. This equipment is available in 2-channel rack mounted units. The 2-channel cards are installed in the same card rack as the induction loop detectors. The probes must have separate card positions since probes and induction loops cannot be combined on the same detector card.
902.15.4 Pull Boxes
Support. Concrete and preformed pull boxes are shown on Standard Plan 902.20 and are defined in the standard specifications. The type of pull box to be used is specified on the plans and on the D-37A sheet.
Guidance. It is desirable to locate a pull box out of the travelway of vehicles. When a pull box is located in the travelway, auxiliary lanes or shoulders, a concrete pull box is specified. When a pull box is located outside the shoulder, behind curb or guardrail, or in non-mountable islands, a preformed pull box is specified. In impervious soil, a pull box with a concrete bottom (Type II drain) is used with a 2 in. pipe drain to an adjacent ditch, slope, or drain structure. Both concrete and preformed pull boxes can be installed with Type II drains. One of three types of Type II drains can be used depending on the adjacent drainage features. Type A is used where there are no adjacent drainage features. Type B is used where the pull box is adjacent to a ditch or slope. Type C is used where the pull box is adjacent to a storm sewer. The elevation of the controller must be higher than the elevation of any pull box in the conduit run.
Standard. Regardless of the type of soil, if the intersection is adjacent to any ditch, slope, or drainage structure, at least one pull box in the conduit system shall have a Type II drain into the adjacent drainage feature. Pull boxes, controllers and other signal appurtenances are not installed in drainage ditches.
The number of pull boxes shall be kept to a minimum. Pull boxes are placed at each end of a conduit line under pavement, except where the conduit run terminates in a service pole. A pull box is required adjacent to detectors to permit a splice between the detector leads and the detector lead-in cable from the controller. A pull box is provided near each post base. A pull box is located at the controller and all wiring, except power supply cables, is routed through this pull box. Pull boxes shall be located a minimum of 2 ft. (0.6 m) from the outside edge of the appurtenance they serve to provide a minimum amount of working area and clearance for conduit elbows and bends. Pull boxes for detectors and signal posts are combined in some instances by skewing the conduit to detectors located in or under the pavement from the pull box provided adjacent to the signal post. This is not permitted where the distance involved exceeds 50 feet.
Guidance. When two or more intersections are to be interconnected, pull box spacing is recommended to be 1500 ft. when fiber optic cable is the only cable in the conduit with Class 2 pull boxes. Class 2 pull boxes are adequate to accommodate the minimum bending radius of the fiber optic cable.
Pull box dimensions are shown in the standard plans. Pull boxes are sized according to the following criteria:
- The smallest preformed pull box is a Class 1 pull box. These boxes are used at locations with 22 or fewer entering conductors. Where required, a standard concrete pull box is used.
- When there are more than 22 but fewer than 69 entering conductors a Class 2 preformed pull box is used. This box is probably the most frequently used preformed pull box. Where required, a standard concrete pull box is used.
- When there are 69 or more entering conductors a Class 3 preformed pull box is used. Where required, a double concrete pull box is used.
- When fiber optic cable is to be installed as part of a project, the Class 5 preformed pull box is used at the signal cabinet and Class 2 pull boxes between intersections.
902.15.5 Conduit System
Support. Electrical connections between traffic signals, detectors, the controller, and power supply in each traffic signal installation or system are made by means of cable installed within closed conduit systems. Cable is exposed only on span wire assemblies. A conduit system provides ease of installation, maintenance, and protection from accidental cutting of the cables. Pull boxes are provided to reduce the number of conduit runs and to facilitate cable pulling and splicing detector leads.
902.15.5.1 Conduit Size
Guidance. Standard conduit size, except those between a loop detector and the first adjacent pull box to the loop detector, is 3 inches. Except for unusual cases, it is preferable to limit the maximum conduit size to 4 inches. When more area is required than is available in this size conduit, parallel lines of conduit providing the required area are used.
Conduit, used solely for loop detectors lead in, can be 1 inch. A conduit run is required for each loop detector. Conduit used solely for interconnect cable, can be 2 inches.
If conduit is being installed in an existing median, use conduit in trench or pushed conduit as required.
902.15.5.2 Conduit Locations
Guidance. Pavement crossings are kept to a minimum. Where alternate conduit locations can achieve the same results, a rough cost comparison is made to determine the most economical plan.
Standard. A minimum of two 3 in. conduits are provided from the first pull box to the controller. A separate conduit containing the power supply cables is provided from the power supply assembly to the controller.
Option. It may run directly from the service pole to the controller without entering a pull box unless the distance from the power supply to the controller is greater than 200 feet. Pull boxes are provided so conduit runs are no more than 200 ft. long.
Support. Conduit slopes are determined in the field by the engineer.
902.15.6 Control and Power Cable
902.15.6.1 Control Cable
Standard. All cable runs are continuous between the signal appurtenances and the controller, except for the cables to loop detectors where splices are required with the detector leads. This reduces maintenance and improves servicing by eliminating most splicing. Voltage drop is kept to a minimum by using a common wire size and separate conductors for each signal head. Number 16 AWG minimum size conductors shall be used for all multi-conductor signaling circuits.
The number of conductors required for traffic signal equipment is as follows:
- Vehicle signal - 7
- Pedestrian signal - 5
- Push button detector - 2
- Loop detector lead-in cable - 2 - #14 AWG
- Loop detector in-duct - 1 - #14 AWG
- Remote On-Off switch - 3
- Luminaires on signal posts - 2 - #12 AWG
The number of various cable combinations is kept to a minimum, preferably no more than four types for each contract, and preferably cables with two, three, five and seven conductors.
Support. These combinations have had the most frequent use and are more likely to be available to contractors. The maximum length of cable in the fewest possible sizes generally will result in lower unit bid prices as the cable is furnished in reels of minimum length.
Available single conductor and multi-conductor cable combinations and their cross-sectional areas are shown below:
Table 902.15.6.1.1 TRAFFIC SIGNAL CABLE AND WIRE
CONDUCTOR TYPE | CABLE SIZE, AWG | AREA, in.2 |
---|---|---|
Single Conductor (stranded), Based on XHHW-2 conductors for power and equipment grounding) | 1c. - #12 | 0.0181 |
1c. - #10 | 0.0243 | |
1c. - #8 | 0.0437 | |
1c. - #6 | 0.0590 | |
1c. - #4 | 0.0814 | |
1c. - #3 | 0.0962 | |
1c. - #2 | 0.114 | |
1c. - #1 | 0.153 | |
1c. - #1/0 | 0.1825 | |
Multi-Conductor Control (stranded), (for signaling circuits) | 2c. - #16 | 0.083 |
3c. - #16 | 0.083 | |
5c. - #16 | 0.117 | |
7c. - #16 | 0.137 | |
Ground Wire (solid) | 1c. - #6 | 0.021 |
1c. - #1 | 0.066 | |
Induction Loop Detector Cable (stranded) | 2c. - #14 (lead-in) | 0.102 |
1c. - #14 (in duct) | 0.023 | |
Interconnect Comm. Cable-Closed Loop Systems (stranded) | 3 pair #16 | 0.208 |
Other types of cables may be required. Obtain specification from manufacturers. | ||
Nominal outside diameter of coax cable shall be 0.305 in. The cable shall be in accordance with Belden Type 8281, West Penn P806 or approved equal. |
Table 902.15.6.1.2 Conduit Sizing
NOMINAL SIZE, in. | INSIDE DIAMETER, in. | INSIDE AREA, in.2. | ALLOWABLE OCCUPIED AREA, in.2 |
---|---|---|---|
3 | 3.042 | 7.27 | 2.91 |
902.15.6.2 Power Cable
Standard. Single conductor cable is used for power cable. Two insulated power cables and a suitably sized ground are required for each traffic signal installation to supply 120 volt, 60 Hz, single-phase alternating current to the controller cabinet. Minimum conductor size for power cable is #8 AWG.
Option. Larger sizes may be required where power requirements are high or where power must be carried over a distance where voltage drop is a consideration. See EPG 902.15.6.5 for sizing power supply cables.
Standard. The maximum allowable voltage drop from the power source to the controller is five percent in order to ensure a high efficiency of operation and long life of the electrical components of the controller.
Guidance. The voltage drop in any electrical circuit is directly dependent upon current and wire resistance. According to Ohm's Law the voltage drop in a line is equal to the current in amperes multiplied by the resistance of the line in ohms. The equation to be used to calculate voltage drop is as follows:
- E = I x R
- E = Voltage
- I = Current (in amperes)
- R = Resistance (in ohms)
The areas of wires in circular mils and the resistance in ohms per 1000 ft. to be used in calculations are shown below:
Table 902.15.6.2.1 Properties for Conductors
SIZE (AWG) | AREA (Circular Mils) | AC RESISTANCE AT 167°F (75°C) (OHMS/1000 ft.) |
---|---|---|
8 | 16,510 | 0.78 |
6 | 26,240 | 0.49 |
4 | 41,740 | 0.31 |
3 | 52,620 | 0.25 |
2 | 66,360 | 0.20 |
1 | 83,690 | 0.16 |
0 | 105,600 | 0.13 |
Table 902.15.6.2.2 Power Cable Sizing
SIZE (AWG) | AREA (Circular Mils) | MAX LOAD (AMPS) |
---|---|---|
8 | 10,381-16,510 | 40 |
6 | 16,511-26,240 | 50 |
4 | 26,241-41,740 | 70 |
3 | 41,741-52,620 | 85 |
2 | 52,621-66,360 | 95 |
1 | 66,361-83,690 | 110 |
1/0 | 83,691-105,600 | 150 |
Table 902.15.6.2.3 Equipment -Power Requirements
ITEM | WATTS | AMPS | |
---|---|---|---|
Controller Breaker | Controller Unit (any type) with accessories | 480 | 4.0 |
Signal Lamp, 12 in. | 20 | 0.17 | |
Lighting Breaker | Luminaire | 150 | 1.3 |
Auxiliary Breaker (15 amps) | Cabinet Fan, Outlet and Cabinet Lamp | 240 | 2.0 |
Table 902.15.6.2.4 Circuit Breaker Sizing
CALCULATED LOAD IN AMPS | CIRCUIT BREAKER TRIP RATING |
---|---|
0-12.00 | 15 |
12.01-16.00 | 20 |
16.01-24.00 | 30 |
24.01-32.00 | 40 |
32.01-40.00 | 50 |
40.01-48.00 | 60 |
48.01-56.00 | 70 |
56.01-64.00 | 80 |
64.01-72.00 | 90 |
72.01-80.00 | 100 |
Support. Example to determine voltage drop.
- Given: 300 ft. from power source to controller cabinet
- #4 AWG Power Supply Cable
- 1 Controller Unit W/Acc., 4.0 amps
- 10 Signal Lamps, 1.7 amps
- 4-150 watt HPS Luminaires, 5.2 amps
- Cabinet Fan, Outlet & Lamp, 2.0 amps
- Total: 12.9 amps
- Voltage Drop (Vd)= I (amps) x R (resistance)
- Vd = 12.9 amps x 2 x 300 ft x 0.31 ohms/1000 ft = 2.4 volts
902.15.6.3 Ground Wire
Standard. A #6 AWG solid or stranded equipment grounding conductor, in conduit, shall be used to connect overhead mounted signal heads on bridge structures to the controller ground. A controller mounted on a structure is grounded by means of a #1 AWG, solid or stranded grounding electrode conductor in conduit connected to a ground rod in the first pull box located off the structure, providing the conductor length does not exceed 200 feet. Over this distance, a larger size wire is used as determined by calculation. Number 6 AWG, solid or stranded equipment grounding conductor shall be used to electrically bond all steel conduits in pull boxes to the power company ground. A properly sized equipment grounding conductor shall be provided in all conduits to provide an effective ground path from each post to the ground bus in the controller cabinet. Plan quantities are not computed for ground wire, but conduit is to be sized accordingly (see Table 902.15.6.1).
902.15.6.4 Circuit Breaker Trip Rating
902.15.6.4.1 At Controller
Guidance. Separate the total amperage load into:
- Controller Breaker - Controller with accessories, and signal lamps.
- Lighting Breaker - Luminaires.
- Auxiliary Breaker - Cabinet fan, lamp and outlet. (15 amps)
Amperage requirements for signal equipment are shown in Table 902.15.6.2.3. To determine the maximum number of lamps illuminated during any one interval of the time cycle, total the number of lamps for each signal head as follows:
- Three-Section Head - 1 Lamp
- Four-Section Head - 1 or 2 Lamps
- Five-Section Head - 2 Lamps
To determine breaker rating, refer to Table 902.15.6.2.4 and select the appropriate breaker size based on the calculated load. Controller and auxiliary circuit breakers are required. When luminaires are specified on signal posts, a separate lighting control cabinet is provided on the outside of the controller cabinet containing a circuit breaker, photocell and other equipment as required. Electrical power to the luminaires is controlled through the photocell switch.
Standard. The breaker rating for the controller, auxiliary and lighting breakers are to be shown on the D-37C sheet. The auxiliary breaker is specified as 15 amps.
Guidance. See Table 902.15.6.2.4 for sizing controller and lighting breakers.
902.15.6.4.2 At Power Supply
Standard. Circuit breakers at the power supply shall be sized to protect the power supply cables.
Guidance. To determine the appropriate trip ratings of the power supply circuit breaker, refer to Table 902.15.6.2.4.
902.15.6.5 Cable Size from Power Supply to Controller
Guidance. Power to the controller is supplied through three single-conductor cables. The maximum factored amperage for the installation is determined by totaling required amperage for the controller(s), accessories, signal lamps, luminaires, and cabinet fan, lamp and outlet and multiplying the total by 1.25. Use Table 902.15.6.2.3 to determine power requirements. The size of each of the cables is to meet or exceed the computed area as determined by the following formula:
- Area (circular mils) = (L x I x 2K)/V = (L x I x 25.8)/6
Where
- K = 12.9 ohm - circular mils per foot @ 75º C
- L = Length from controller to service pole plus (ft) additions
- I = Maximum load in amps
- V = 6 volts (5% of 120V), the maximum allowed voltage drop
After the required area is computed, use Table 902.15.6.2.2 to determine the size wire to be used. If the maximum factored amperage exceeds the maximum load for that wire size as shown in Table 902.15.6.2.2, use the wire size required to carry the load.
902.15.7 Traffic Signal Installations
Guidance. Permanent signals are installations using steel mast arm poles or steel span wire, underground conduit and basic intersection lighting. Temporary signals are installed using wood poles. They are used for construction projects or where a project will be replacing them in the near future. Mast arm pole signal installations are preferable, but each case is decided on its own merits and the funding available. If a street is to be widened or an intersection is to be reconstructed in the near future, the temporary traffic signal installation is designed to conform to the final layout, as nearly as is practical, and if future interconnection can be predicted, the temporary traffic signal controller is equipped for this eventuality.
The signals, lighting, and intersection geometrics are constructed according to current Design standards. Permanent signals are typically installed with construction projects or at locations where there are no programmed major roadway projects that would affect the signals.
902.15.7.1 Span Wire Signals
Guidance. Span wire signals are installed with wood or steel span wire poles and overhead wiring. Temporary signals are designed as wood pole span wire signals as shown in the standard plans. A steel span wire post is recommended where guy wires for a wood pole cannot be used, especially for long spans.
Span wire signals can be installed by contract, by MoDOT forces, or a combination of the two. Span wire signals are typically installed where limited right-of-way or limited space for underground conduit necessitate their use. Temporary span wire signals can be installed where there is a future construction project that will install signals or where there is no work currently programmed. If no work is programmed, it would be preferable to pursue the programming of a permanent signal installation.
Standard Diagonal span wire signals, excluding intersection control beacons, shall not be used. Span wire signals are to be installed with basic lighting on the signal poles (silhouette lighting) or direct reflectance lighting if raised islands are installed unless other basic lighting is in place. Off-signal, direct reflectance lighting could be needed if raised islands are present.
A pole on state right of way owned by other shall not be used to support span wire signals. If an adjustment of the location for a department installed pole cannot be made, the existing pole shall be moved at the expense of the owner.
Option. For temporary span wire traffic signals, the power supply may be installed on one of the span wire poles if it is close to the right of way line or utility company facility. If not, a separate power supply is to be installed at the right of way line or utility company facility. If possible, the power supply is to be installed to be compatible with future construction.
If the signal controller can be located to be compatible with future construction, then it may be installed on a concrete base at the permanent location.
902.15.8 Modifying Existing Traffic Signal Installations
Guidance. The preliminary layout for modifying existing traffic signal installations shows both the existing and proposed installation. The final plans show existing appurtenances to remain in place, be abandoned or removed. Existing features are shown as dashed lines and new features as solid lines. Temporary signals are investigated and considered when existing signals are to be modified. Using existing conduit during signal modifications should be carefully evaluated and new conduit should be considered.
902.15.9 Temporary Signals During Upgrades
Guidance. Existing signals are not to be taken out of service during signal modifications, unless absolutely necessary.
Option. Wood pole cable spans may be used as needed to facilitate the modifications. A scaled layout of the temporary signal is included in the plans showing all items, including cables. These installations are paid for as temporary traffic signals, per lump sum.
902.15.10 Quantities
Guidance. When the plans are completed, the quantities of materials required are tabulated on the D-37 sheets. The use of identification symbols on the D-37 sheets eliminates unnecessary repetition as to location of each appurtenance in the tabulation of conduit and cable quantities. Both conduit and cable quantities are carefully calculated, as plan quantities are the basis of payment. It is not necessary to show signal quantities on the "2-B" sheets of roadway plans.
902.15.11 Conduit
Guidance. These quantities are calculated or scaled from the plans to the nearest linear foot. Measurement is made from center-to-center of all pull boxes, post bases, and controllers. The center-to-center distance is modified to allow for the proper amount of conduit required for construction.
- A quantity of 2 ft. added to the center-to-center distance provides the length necessary to turn the conduit up to ground level for a Type F or Type C base.
- A quantity of 4 ft. added to the center-to-center distance provides the length necessary to turn the conduit up to ground level and to the top of a Type A base or ground mounted controller cabinet base.
- If the conduit runs between two pull boxes, 1 ft. is subtracted from the center-to-center distance at each end, totaling 2 feet.
902.15.12 Cable
Guidance. These quantities are calculated or scaled from the plans to the nearest linear foot. Measurement is made from center of pull box to center of pull box or center of signal post, controller, or service pole. Cable from the controller to the loop detectors is measured to the first pull box adjacent to the detector where the splice to the detector leads is made. Pole and bracket cable must be used from the signal post base to the luminaire. At the signal post base, the pole and bracket cables are spliced to the 2c - #12 AWG using a fused slip connector assembly as shown in Standard Plan 901.02. Signal heads mounted on the side of mast arm signal posts are provided with conductor cable connection to the controller separate from that provided for the overhead mounted signal head if the side mounted signal does not operate identically with the signal on the mast arm. When the signals operate identically during all signal phases, a 7-conductor cable is provided to the signal head on the mast arm from the controller and a 7-conductor jumper cable is provided from the signal head on the mast arm to the side mounted signal. This is done to ensure the mast arm signal will continue to operate in the event of an accident that disables the side mounted signal. If two signal heads mounted on the same mast arm operate identically during all phases, a 7-conductor jumper cable can be provided between terminal compartments and only one 7-conductor cable is required to the controller. A maximum of two 7-conductor jumpers are allowed between three signal heads. The cable length for the jumper is included in the cable quantities for that cable run. A signal head located in front of a left turn auxiliary lane has a separate 7-conductor cable to the controller even if a left turn phase is not being used.
Additional cable quantities are added to the center-to-center measurement to provide slack and to provide for the cable to be turned up and connected to terminal strips in the controller, signal head terminal compartments, signal head disconnect hangers, and detectors, or to the service head of the power supply assembly as follows:
- 6 ft. of each cable passing through each pull box. 3 ft. if the cable terminates in the pull box, as in Lead-In or In-Duct loop detector cable.
- 8 ft. of each cable at the controller.
- 13 ft. of each cable at side mounted and post top mounted vehicular signal heads.
- 10 ft. of each cable at side mounted and post top mounted pedestrian signal heads.
- 9 ft. of each cable to pedestrian pushbutton detectors located on posts.
- 21 ft. of each cable at each signal post with mast arm plus the length of the mast arm or distance to the first signal terminal compartment.
- 35 ft. of each cable at the service pole supporting the power supply assembly.
- 8 ft. of each cable when connecting to a pedestal mounted power supply.
- The length required to turn up the post and connect to span wire mounted detectors or signal heads.
- 30 ft. plus the bracket arm length for cables to luminaires on signal posts.
- 60 ft. of fiber cable at pull boxes adjacent to signal or splice cabinets.
- 10 ft. of fiber cable passing through each pull box.
The cable quantities on each D-37 sheet are totaled to the nearest linear foot. The total of all D-37 sheets is rounded to the nearest 10 linear feet on the estimate.
902.15.13 Color Sequence
Guidance. The color sequence, or interval sequence of signal indications showing all possible variations in indications due to phase skipping or auxiliary equipment, is shown on a D-38 sheet that accompanies the plans. Several standard signal phasing and layout (D-38) sheets are available. If used, these sheets are to be reviewed and modified as necessary according to conditions.
902.15.14 Utility Conflicts
Guidance. Where overhead signal mountings are used, the design should be checked to ensure there is no conflict with existing overhead wiring as well as underground utilities.
902.15.15 Estimate
Guidance. Any estimate dealing with traffic signals should be reviewed by district Traffic for proper inclusion of needed items. Common items such as controller type, cabinet size, signal and pedestrian heads and indications, and non-contractual items can be miscategorized or omitted. Accurate bid items will greatly reduce the need for more expensive change orders during the construction of the signal.
902.15.16 Job Special Provisions
Guidance. All Job Special Provisions (JSPs) should be reviewed by district Traffic for applicability and thoroughness. Special equipment not yet accounted for in the Standard Specification must be detailed by a JSP in order to have a bid quantity. JSPs should also be used to ensure MoDOT communication lines through project limits are kept intact (if required). Any other special construction methods needed to ensure a properly operating signal must be detailed by a JSP.